An induction furnace heats metal through electromagnetic induction, a process that generates heat directly within the metal itself. An alternating current flows through a copper coil, creating a rapidly reversing magnetic field. This field induces eddy currents in the conductive metal charge placed inside the furnace. The resistance of the metal to these eddy currents generates heat via Joule heating, melting the metal efficiently and uniformly. The process is highly controllable, with the frequency of the alternating current determining the depth of heat penetration. Induction furnaces are widely used in metal casting and foundry operations due to their precision, energy efficiency, and clean operation.
Key Points Explained:
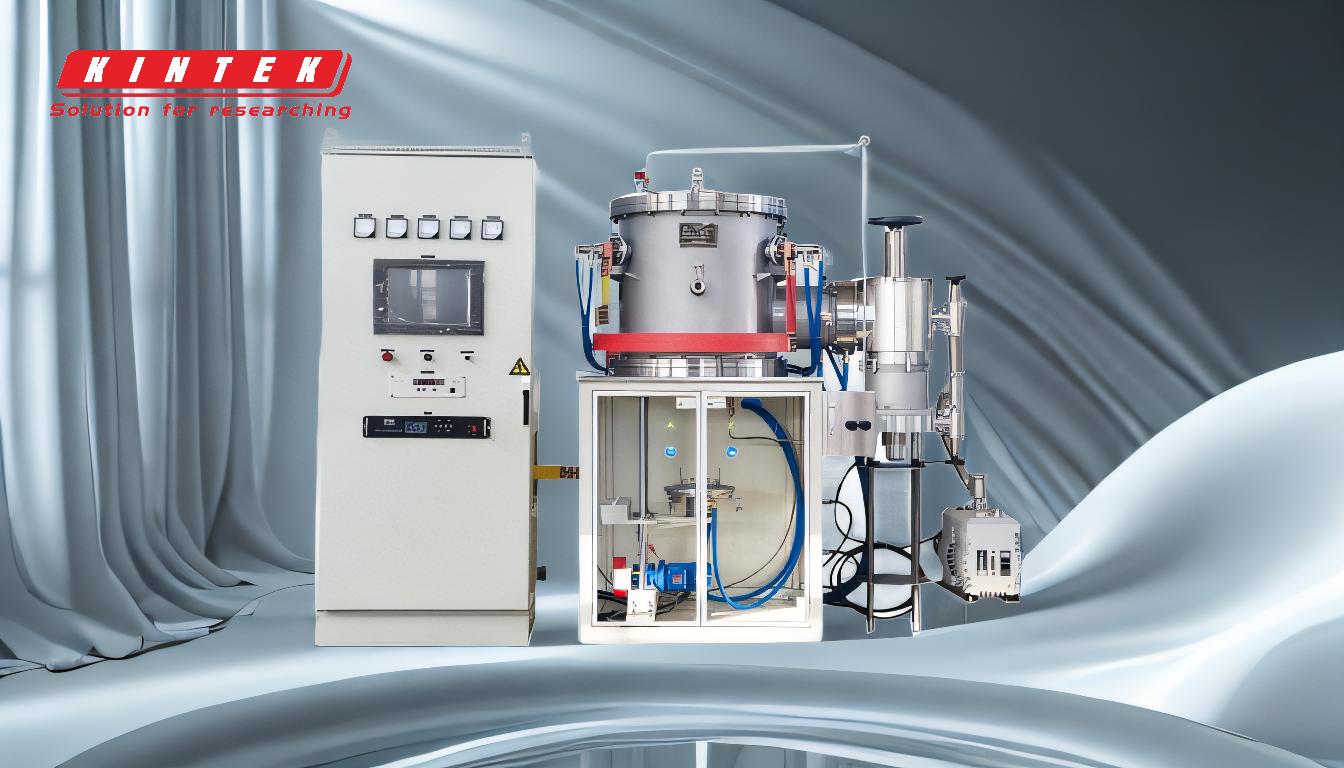
-
Electromagnetic Induction and Eddy Currents:
- The core mechanism of an induction furnace relies on electromagnetic induction. When an alternating current passes through a copper coil, it generates a rapidly reversing magnetic field.
- This magnetic field penetrates the conductive metal charge placed inside the furnace, inducing eddy currents within the metal.
- Eddy currents are loops of electrical current induced within conductors by a changing magnetic field. These currents flow through the metal's resistance, generating heat.
-
Joule Heating:
- The heat generated in the metal is a result of Joule heating (also known as resistive heating). As the eddy currents flow through the metal, they encounter resistance, which converts electrical energy into thermal energy.
- This process ensures that the heat is generated directly within the metal, making the heating process highly efficient and localized.
-
Role of Alternating Current Frequency:
- The frequency of the alternating current plays a critical role in determining the depth of heat penetration into the metal. Higher frequencies result in shallower penetration, while lower frequencies allow deeper penetration.
- This characteristic allows for precise control over the heating process, making induction furnaces suitable for a wide range of applications, from surface hardening to deep melting.
-
Magnetic Hysteresis in Ferromagnetic Materials:
- In ferromagnetic materials like iron, additional heating occurs due to magnetic hysteresis. As the magnetic field reverses, the magnetic domains within the material realign, generating heat.
- This phenomenon contributes to the overall heating efficiency, particularly in metals with high magnetic permeability.
-
Stirring Effect of Eddy Currents:
- Once the metal begins to melt, the eddy currents also create a stirring effect within the molten metal. This ensures uniform temperature distribution and thorough mixing, which is essential for producing high-quality alloys and castings.
-
Components of an Induction Furnace:
- Copper Coil: The primary component that carries the alternating current and generates the magnetic field.
- Crucible: A nonconductive container that holds the metal charge. It is typically made of materials like ceramic or graphite to withstand high temperatures.
- Power Supply: Converts standard electrical power into the required alternating current frequency for the induction process.
-
Advantages of Induction Furnaces:
- Energy Efficiency: Heat is generated directly within the metal, minimizing energy loss.
- Precision: The ability to control frequency and power allows for precise temperature regulation.
- Clean Operation: Since the heat is generated internally, there is no direct combustion, reducing contamination and emissions.
- Uniform Heating: The stirring effect ensures even heat distribution, critical for consistent material properties.
-
Applications:
- Induction furnaces are widely used in metal casting, foundry operations, and alloy production. They are also employed in processes like surface hardening, annealing, and brazing, where precise and localized heating is required.
By leveraging electromagnetic induction, Joule heating, and the unique properties of alternating current, induction furnaces provide a highly efficient and controllable method for heating and melting metals. This makes them indispensable in modern metallurgical processes.
Summary Table:
Key Aspect | Description |
---|---|
Electromagnetic Induction | Alternating current in a copper coil creates a magnetic field, inducing eddy currents in the metal. |
Joule Heating | Eddy currents generate heat through resistance, melting the metal efficiently. |
AC Frequency Role | Higher frequencies = shallow heat; lower frequencies = deep heat penetration. |
Magnetic Hysteresis | Ferromagnetic materials heat further due to magnetic domain realignment. |
Stirring Effect | Eddy currents ensure uniform temperature and mixing in molten metal. |
Components | Copper coil, crucible (ceramic/graphite), and power supply. |
Advantages | Energy-efficient, precise, clean, and uniform heating. |
Applications | Metal casting, foundry operations, alloy production, surface hardening, and more. |
Discover how an induction furnace can revolutionize your metalworking process—contact us today for expert guidance!