Physical Vapor Deposition (PVD) is a sophisticated coating technique used to deposit thin films of material onto a substrate. The process involves converting a solid precursor material into a vapor phase, which then condenses onto the substrate to form a thin, durable, and high-performance coating. PVD is widely used in industries requiring high-quality, corrosion-resistant, and wear-resistant coatings. The process is carried out in a vacuum chamber to minimize contamination and ensure precise control over the deposition. Key methods include thermal evaporation, sputtering, and electron beam evaporation, each offering unique advantages depending on the application.
Key Points Explained:
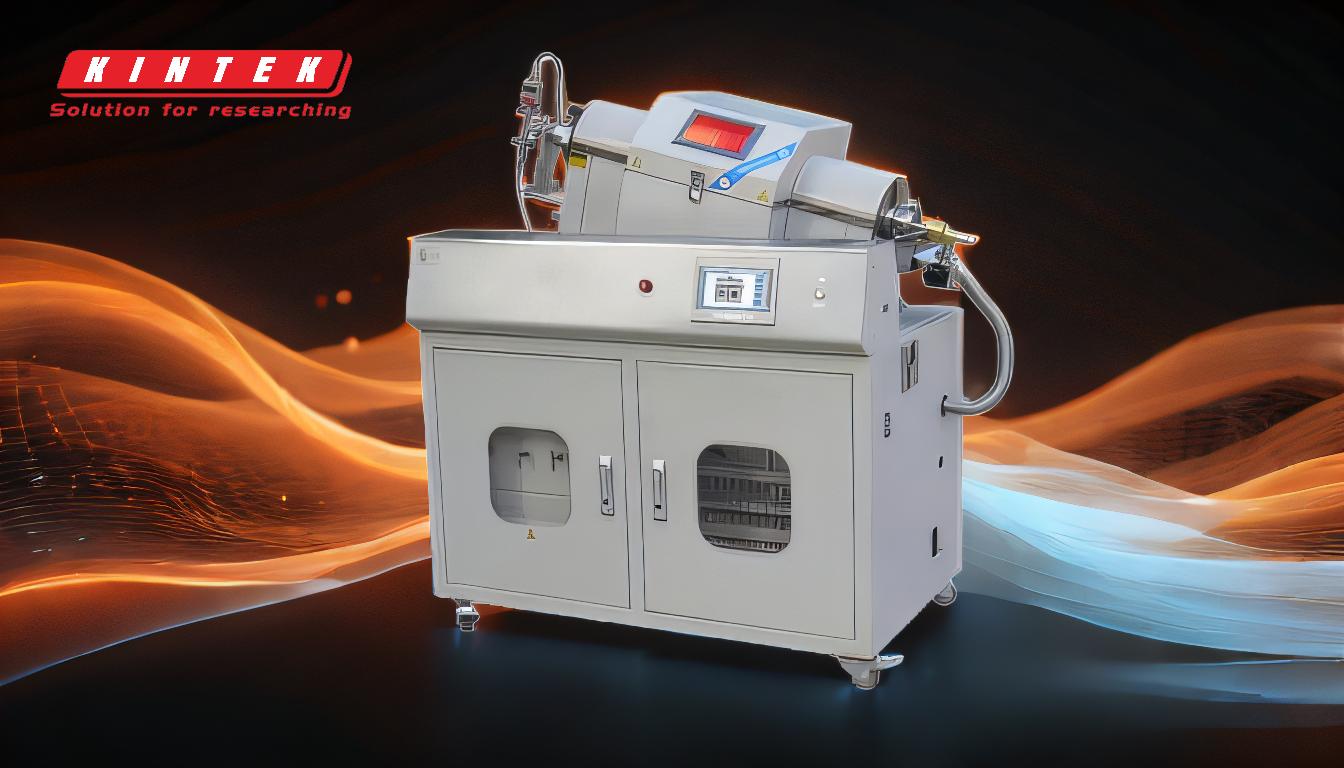
-
Vaporization of Solid Precursor Material:
- The PVD process begins with the vaporization of a solid precursor material. This is achieved through various methods such as thermal evaporation, sputtering, or electron beam bombardment.
- In thermal evaporation, the material is heated to its vaporization point, causing it to turn into a gas.
- Sputtering involves bombarding the target material with high-energy ions, causing atoms to be ejected from the surface and enter the gas phase.
- Electron beam evaporation uses a focused beam of high-energy electrons to vaporize the material.
-
Transport of Vaporized Atoms:
- Once the solid material is vaporized, the resulting atoms or molecules travel through a low-pressure or vacuum environment.
- The vacuum environment is crucial as it minimizes the presence of background gases that could chemically react with the vaporized material, ensuring a pure and uncontaminated deposition.
-
Deposition onto Substrate:
- The vaporized atoms then condense onto the substrate, forming a thin film.
- The substrate can be made of various materials, including metals, ceramics, and polymers, depending on the desired application.
- The deposition process can be controlled to achieve precise thickness and uniformity of the coating.
-
Control of Film Thickness and Rate:
- The thickness and deposition rate of the film are carefully monitored and controlled using tools such as quartz crystal rate monitors.
- These monitors provide real-time feedback on the deposition rate, allowing for adjustments to ensure the desired film thickness and quality.
-
Types of PVD Techniques:
- Thermal Evaporation: Involves heating the material until it vaporizes. This method is suitable for materials with relatively low melting points.
- Sputtering: Uses ion bombardment to eject atoms from the target material. This technique is versatile and can be used for a wide range of materials, including those with high melting points.
- Electron Beam Evaporation: Utilizes a focused electron beam to vaporize the material. This method is particularly useful for materials that require high energy to vaporize.
-
Advantages of PVD:
- High-Quality Coatings: PVD produces thin films with excellent adhesion, uniformity, and durability.
- Versatility: The process can be used to deposit a wide range of materials, including metals, ceramics, and alloys.
- Environmental Benefits: PVD is a clean process that produces minimal waste and does not involve harmful chemicals.
- Enhanced Material Properties: PVD coatings can improve the hardness, wear resistance, and oxidation resistance of the substrate material.
-
Applications of PVD:
- Industrial Coatings: PVD is used to coat cutting tools, molds, and machine components to enhance their durability and performance.
- Electronics: The process is employed in the fabrication of semiconductors, optical coatings, and thin-film solar cells.
- Decorative Coatings: PVD is used to apply decorative and functional coatings on watches, jewelry, and architectural components.
- Medical Devices: PVD coatings are applied to medical implants and instruments to improve biocompatibility and resistance to wear.
In summary, Physical Vapor Deposition (PVD) is a versatile and precise coating technique that involves the vaporization of a solid material, transport of the vaporized atoms in a vacuum, and deposition onto a substrate. The process offers numerous advantages, including high-quality coatings, versatility, and environmental benefits, making it a valuable method in various industries.
Summary Table:
Key Aspect | Details |
---|---|
Process | Vaporization of solid material, transport in vacuum, deposition on substrate |
Key Methods | Thermal evaporation, sputtering, electron beam evaporation |
Advantages | High-quality coatings, versatility, environmental benefits |
Applications | Industrial coatings, electronics, decorative coatings, medical devices |
Discover how PVD can enhance your products—contact our experts today!