The melting point of an arc furnace is not a fixed value, as it depends on the type of furnace (industrial or laboratory) and the materials being melted. Industrial electric arc furnaces (EAFs) typically operate at temperatures up to 1,800°C, which is sufficient for melting most metals used in industrial applications. In laboratory settings, arc furnaces can achieve much higher temperatures, often exceeding 3,000°C, due to their smaller scale and more controlled conditions. The electric arc itself, which is the heat source, can produce temperatures between 3,000°C and 3,500°C during low tension (L.T.) operation. These high temperatures make arc furnaces suitable for melting a wide range of materials, including steel, iron, and other refractory metals.
Key Points Explained:
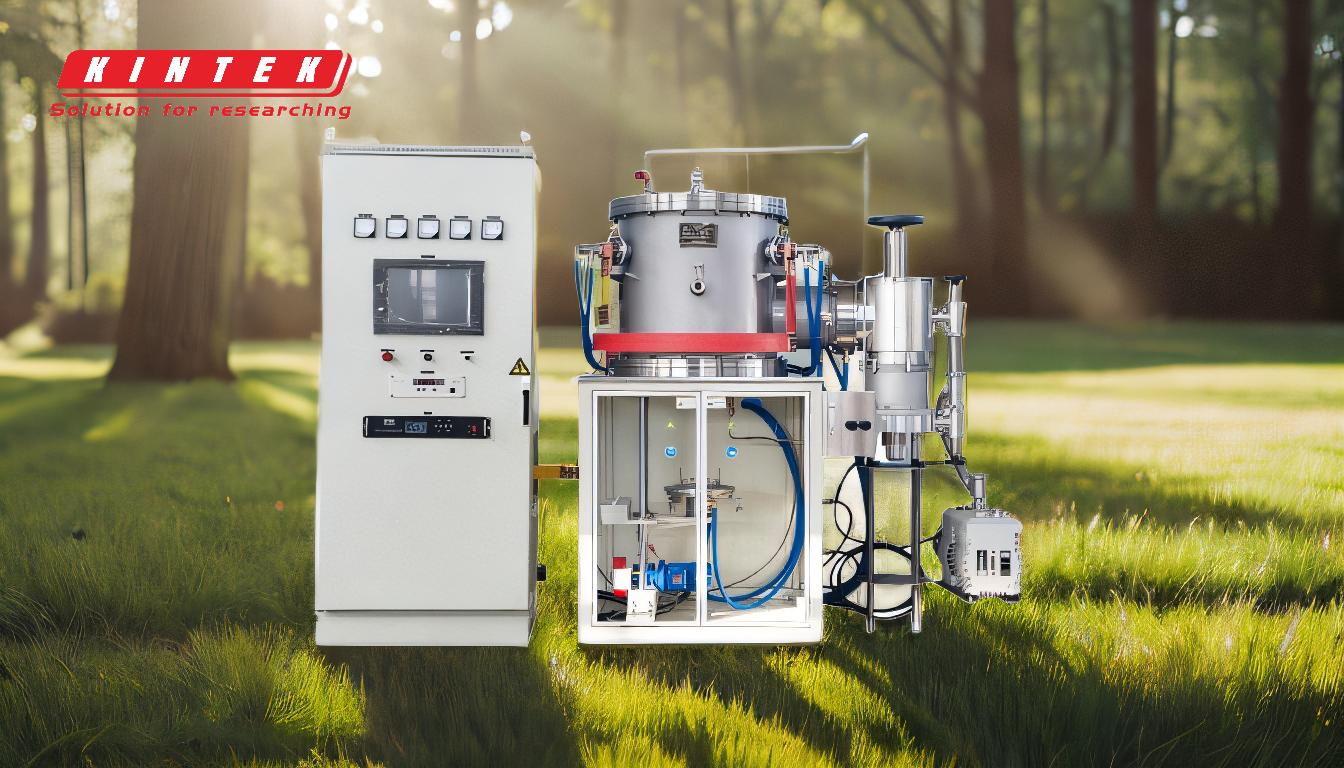
-
Temperature Range in Industrial Arc Furnaces:
- Industrial electric arc furnaces (EAFs) are designed to operate at temperatures up to 1,800°C. This temperature range is sufficient for melting metals such as steel and iron, which are commonly used in industrial manufacturing processes.
- The relatively lower temperature in industrial EAFs is due to the larger scale of these furnaces and the need to balance energy efficiency with the melting requirements of common industrial metals.
-
Temperature Range in Laboratory Arc Furnaces:
- Laboratory arc furnaces, which are smaller and more specialized, can achieve much higher temperatures, often exceeding 3,000°C. These furnaces are used for research and development purposes, where the melting of refractory metals or other high-temperature materials is required.
- The higher temperatures in laboratory settings are made possible by the smaller size of the furnace, which allows for more precise control over the electric arc and the heat generated.
-
Electric Arc Temperature:
- The electric arc itself, which is the primary heat source in an arc furnace, can produce temperatures between 3,000°C and 3,500°C during low tension (L.T.) operation. This high temperature is generated by the electrical discharge between the electrodes and the material being melted.
- The temperature of the electric arc is critical for the efficiency and effectiveness of the furnace, as it directly influences the melting rate and the quality of the molten material.
-
Factors Influencing Melting Point:
- The melting point of an arc furnace is influenced by several factors, including the type of material being melted, the design of the furnace, and the operating conditions (e.g., industrial vs. laboratory).
- For example, refractory metals such as tungsten or molybdenum require much higher temperatures to melt compared to common industrial metals like steel or iron. Therefore, the melting point of the furnace must be adjusted based on the specific application.
-
Applications of Arc Furnaces:
- Arc furnaces are widely used in both industrial and laboratory settings for melting metals and other materials. In industrial applications, they are commonly used in steel production, where they offer advantages such as energy efficiency and the ability to recycle scrap metal.
- In laboratory settings, arc furnaces are used for research purposes, such as the development of new alloys or the study of high-temperature materials.
-
Design and Operation of Arc Furnaces:
- Modern arc furnaces are designed with vertically positioned graphite electrodes that strike directly into the metal bath. The most common design is the three-electrode, three-phase, alternating-current furnace, although single-electrode, direct-current furnaces are also used in some applications.
- The design of the furnace, including the type of electrodes and the power supply, plays a significant role in determining the maximum temperature that can be achieved.
In summary, the melting point of an arc furnace varies depending on whether it is used in an industrial or laboratory setting, with industrial furnaces typically operating at lower temperatures (up to 1,800°C) and laboratory furnaces capable of reaching much higher temperatures (over 3,000°C). The electric arc itself can produce temperatures between 3,000°C and 3,500°C, making arc furnaces highly versatile for a wide range of melting applications.
Summary Table:
Aspect | Industrial Arc Furnace | Laboratory Arc Furnace |
---|---|---|
Temperature Range | Up to 1,800°C | Exceeds 3,000°C |
Primary Use | Melting steel, iron | Research, refractory metals |
Electric Arc Temperature | 3,000°C - 3,500°C | 3,000°C - 3,500°C |
Key Features | Energy-efficient, scalable | Precise, high-temperature |
Need help choosing the right arc furnace for your application? Contact our experts today!