The most common type of graphite is synthetic graphite, which is widely used across various industries due to its excellent thermal stability, high compressive strength, and versatility. It is particularly favored in high-temperature applications, such as in graphite furnaces, where it can withstand extreme conditions without losing its structural integrity. Synthetic graphite is also used in industrial processes like degassing, fluxing, and injection, as well as in recreational products like fishing rods and tent frames. Its lightweight nature and durability make it a preferred material for applications requiring both strength and thermal resistance.
Key Points Explained:
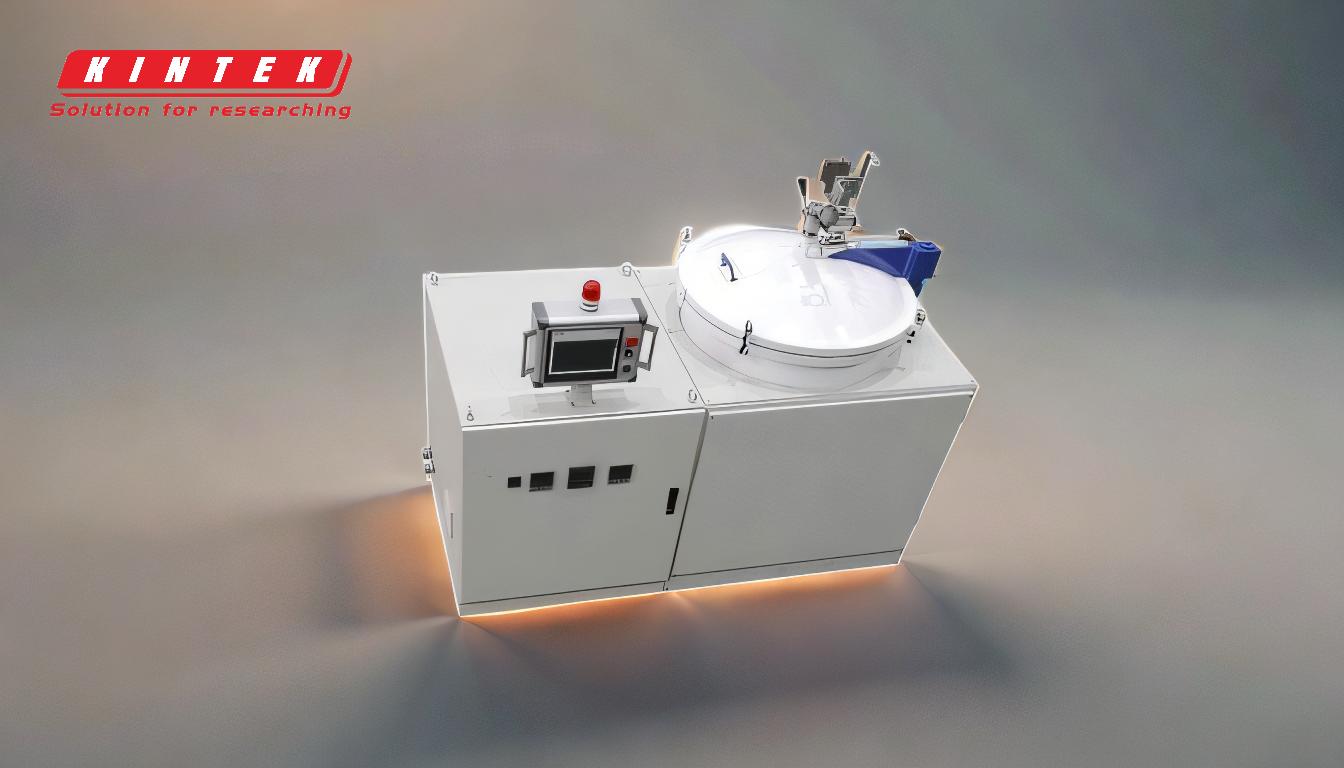
-
Synthetic Graphite as the Most Common Type
- Synthetic graphite is the most widely used form of graphite due to its consistent properties and ease of production. It is manufactured through the high-temperature treatment of carbon-rich materials like petroleum coke or coal tar pitch. This process ensures uniformity in its structure, making it ideal for industrial and commercial applications.
-
Applications in High-Temperature Environments
- Synthetic graphite is extensively used in graphite furnaces, which operate in vacuum or protective atmospheres. Its ability to maintain dimensional integrity at temperatures up to 5000°F makes it indispensable for high-temperature material processing.
-
Industrial Uses
- Graphite is commonly employed in industrial processes such as degassing shafts, impellers, fluxing, and injection tubes. Its thermal stability and resistance to chemical reactions make it suitable for these demanding applications.
-
Recreational and Lightweight Applications
- Beyond industrial uses, graphite is also found in recreational products like kite frames, tent poles, kayak riggers, and fishing rods. Its lightweight nature, combined with high strength, makes it ideal for these applications.
-
High Compressive Strength
- Graphite exhibits high compressive strength, allowing it to withstand significant loads without deformation. This property, along with its lighter weight compared to materials like steel, enhances safety and efficiency in industrial processes.
-
Advantages Over Natural Graphite
- While natural graphite exists, synthetic graphite is preferred for most applications due to its purity, consistency, and tailored properties. Natural graphite often contains impurities that can affect performance in critical applications.
-
Role in Preventing Accidents
- The lightweight nature of graphite workpieces reduces the risk of accidents during handling and processing. This is particularly important in industries where heavy materials could pose safety hazards.
In summary, synthetic graphite is the most common type of graphite due to its versatility, thermal stability, and strength. Its applications range from high-temperature industrial processes to lightweight recreational products, making it a critical material in modern manufacturing and everyday life.
Summary Table:
Property | Details |
---|---|
Type | Synthetic Graphite |
Key Features | Thermal stability, high compressive strength, lightweight, and durability |
Applications | Graphite furnaces, degassing, fluxing, injection, fishing rods, tent frames |
Temperature Resistance | Up to 5000°F |
Advantages | Purity, consistency, lightweight, and reduced accident risks |
Interested in synthetic graphite for your applications? Contact us today to learn more!