The MS temperature in heat treatment refers to the specific temperature at which the transformation of austenite to martensite begins during the cooling process. This temperature is critical in determining the microstructure and mechanical properties of the steel. For low carbon, low alloy steels, the MS temperature typically starts around 350°C. Understanding and controlling the MS temperature is essential for achieving desired material properties such as hardness, strength, and toughness in heat-treated components.
Key Points Explained:
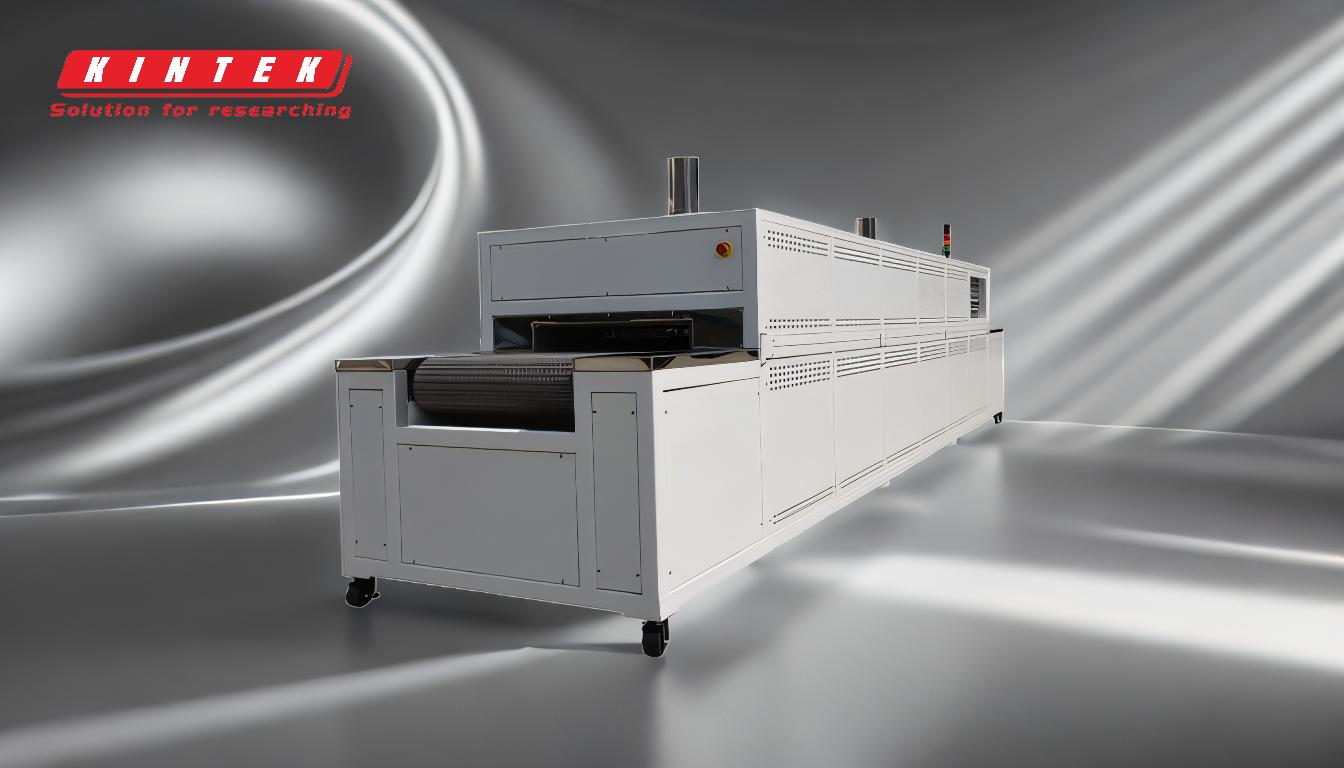
-
Definition of MS Temperature:
- The MS temperature, or martensite start temperature, is the point at which austenite begins to transform into martensite during cooling. This transformation is a diffusionless process that occurs rapidly and results in a hard, brittle microstructure.
-
Importance in Heat Treatment:
- The MS temperature is a critical parameter in heat treatment processes, particularly in quenching. It determines the cooling rate required to achieve the desired martensitic structure, which is essential for enhancing the hardness and strength of the steel.
-
Typical MS Temperature for Low Carbon, Low Alloy Steels:
- For low carbon, low alloy steels, the MS temperature is generally around 350°C. This value can vary depending on the specific composition of the steel, including the amounts of carbon and other alloying elements.
-
Factors Influencing MS Temperature:
- Carbon Content: Higher carbon content tends to lower the MS temperature, making it more challenging to achieve a fully martensitic structure.
- Alloying Elements: Elements such as manganese, chromium, and nickel can also affect the MS temperature, either lowering or raising it depending on their concentration.
- Cooling Rate: The rate at which the steel is cooled from the austenitizing temperature can influence the MS temperature and the extent of martensite formation.
-
Practical Implications for Equipment and Consumables Purchasers:
- Material Selection: Understanding the MS temperature helps in selecting the appropriate steel grade for specific applications, ensuring that the material can achieve the desired properties after heat treatment.
- Process Optimization: Knowledge of the MS temperature allows for the optimization of heat treatment processes, such as quenching, to achieve the best possible microstructure and mechanical properties.
- Quality Control: Monitoring and controlling the MS temperature during heat treatment processes is crucial for maintaining consistency and quality in the final product.
-
Considerations for Heat Treatment Equipment:
- Quenching Media: The choice of quenching medium (oil, water, or air) should be based on the MS temperature to ensure the correct cooling rate is achieved.
- Temperature Control: Precise temperature control during the cooling phase is essential to hit the MS temperature accurately and avoid issues such as incomplete transformation or excessive brittleness.
By understanding the MS temperature and its implications, equipment and consumables purchasers can make informed decisions that enhance the performance and durability of heat-treated components.
Summary Table:
Aspect | Details |
---|---|
Definition | MS temperature is the point where austenite transforms into martensite. |
Typical MS Temperature | ~350°C for low carbon, low alloy steels. |
Influencing Factors | Carbon content, alloying elements, and cooling rate. |
Practical Implications | Material selection, process optimization, and quality control. |
Equipment Considerations | Quenching media and precise temperature control are critical. |
Optimize your heat treatment processes with expert guidance—contact us today!