The order of sieves in sieving is a critical aspect of the sieving process, ensuring efficient separation of particles based on size. Sieves are arranged in a stack, with the sieve having the largest mesh holes placed at the top and progressively tighter mesh sizes as you move downward. This arrangement allows larger particles to be retained on the top sieve, while smaller particles pass through to the lower sieves. The process involves careful selection of sieves, precise sample preparation, and systematic analysis to achieve accurate results. Below, the key points of sieve order and its importance are explained in detail.
Key Points Explained:
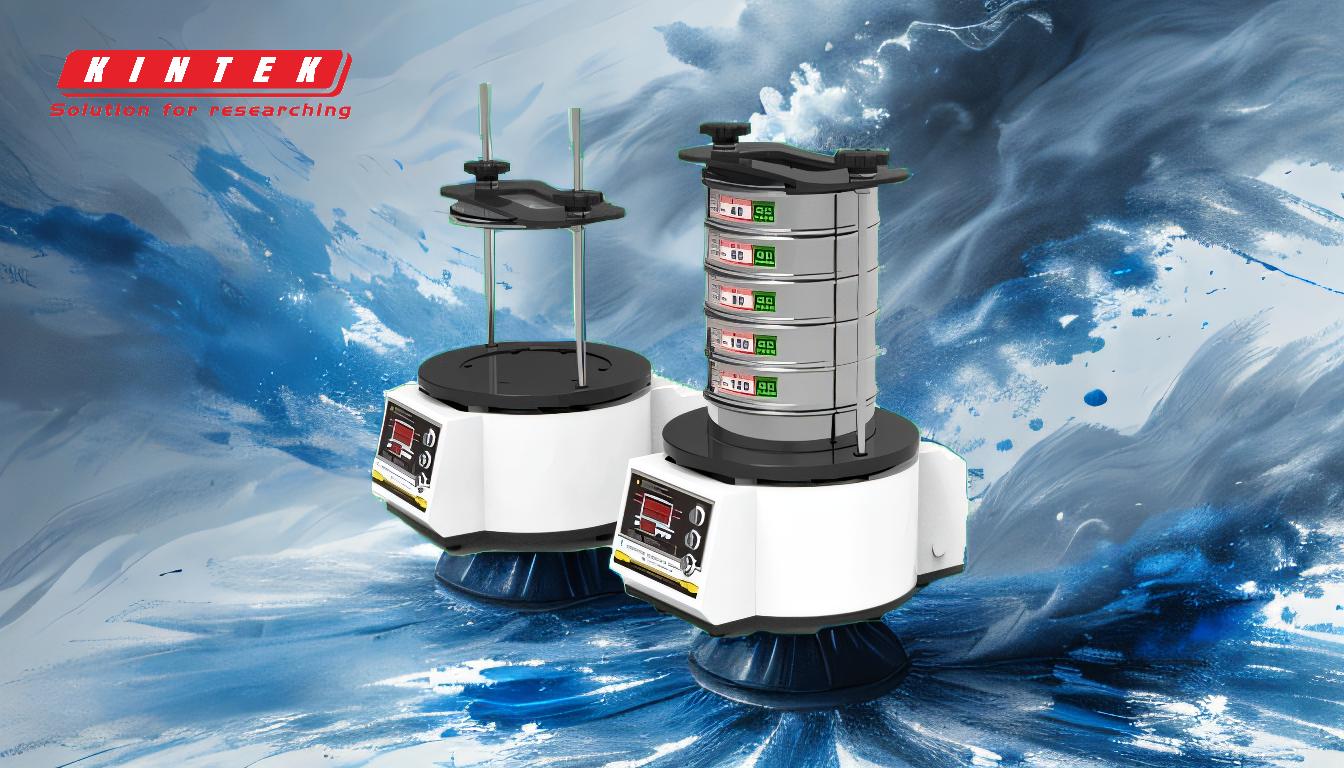
-
Sieve Stack Arrangement:
- Sieves are organized in a stack, with the largest mesh size at the top and progressively smaller mesh sizes downward.
- This ensures that larger particles are retained on the top sieve, while smaller particles pass through to the lower sieves.
- Example: A stack might start with a 4.75 mm mesh at the top, followed by 2.36 mm, 1.18 mm, and so on, down to the finest sieve.
-
Purpose of Sieve Order:
- The order facilitates the separation of particles into distinct size fractions.
- It ensures that each sieve captures particles within a specific size range, allowing for accurate particle size distribution analysis.
- This is essential for quality control in industries like construction, pharmaceuticals, and food processing.
-
Number of Sieves in a Stack:
- The number of sieves used can range from 1 to 18, depending on the material being analyzed and the required precision.
- More sieves allow for a more detailed particle size distribution analysis.
- For example, a simple analysis might use 3-5 sieves, while a detailed analysis could require 10 or more.
-
Selection of Suitable Test Sieves:
- The choice of sieves depends on the material properties and the desired particle size ranges.
- Sieves must comply with standardized mesh sizes (e.g., ISO or ASTM standards) to ensure consistency and accuracy.
- Example: For soil analysis, sieves with mesh sizes of 2 mm, 1 mm, 500 µm, and 250 µm might be selected.
-
Sieving Process Steps:
- Sampling: Collect a representative sample of the material to be analyzed.
- Sample Division: If necessary, divide the sample to ensure uniformity.
- Sieve Selection: Choose sieves with appropriate mesh sizes for the material.
- Sieving Parameters: Set parameters like sieving time and motion type (e.g., horizontal or vertical shaking).
- Sieve Analysis: Perform the actual sieving, allowing particles to separate based on size.
- Recovery of Sample Material: Collect the material retained on each sieve for further analysis.
- Data Evaluation: Calculate the percentage of material retained on each sieve to determine particle size distribution.
- Cleaning and Drying: Clean and dry the sieves to prepare them for future use.
-
Importance of Sieve Order in the Sieving Process:
- Correct sieve order ensures that particles are accurately separated into their respective size fractions.
- It prevents contamination of results, such as larger particles being mistakenly retained on finer sieves.
- Proper arrangement also improves the efficiency of the sieving process, reducing the time required for analysis.
-
Practical Considerations for Equipment Purchasers:
- When purchasing sieves, consider the material being analyzed and the required mesh sizes.
- Ensure that the sieves are durable and comply with relevant standards (e.g., ISO 3310-1 for test sieves).
- For automated sieving machines, verify compatibility with the sieve stack arrangement and motion type.
By understanding the order of sieves and its role in the sieving process, equipment and consumable purchasers can make informed decisions to optimize their particle size analysis workflows.
Summary Table:
Key Aspect | Details |
---|---|
Sieve Stack Arrangement | Largest mesh at the top, progressively smaller downward (e.g., 4.75 mm to 250 µm). |
Purpose of Sieve Order | Separates particles into size fractions for accurate distribution analysis. |
Number of Sieves | 1 to 18 sieves, depending on material and precision requirements. |
Sieve Selection | Based on material properties and standardized mesh sizes (ISO/ASTM). |
Sieving Process Steps | Sampling, sieve selection, sieving analysis, data evaluation, and cleaning. |
Importance of Sieve Order | Ensures accurate separation, prevents contamination, and improves efficiency. |
Practical Considerations | Choose durable sieves compliant with ISO/ASTM standards for your material. |
Ensure accurate particle size analysis with the right sieve arrangement—contact our experts today for guidance!