Vacuum Arc Remelting (VAR) is a specialized metallurgical process used to refine and purify metals and alloys by melting a consumable electrode under vacuum conditions using a DC arc. The molten metal forms droplets that pass through an extremely high-temperature arc zone, undergoing physical and chemical reactions that purify the metal, improve its crystal structure, and enhance its mechanical properties. The refined metal solidifies in a water-cooled copper mold, resulting in high-grade, ultraclean alloys. VAR is particularly effective for reactive metals like titanium and zirconium, as well as for steels and superalloys, due to its ability to minimize contamination, reduce impurities, and control solidification rates.
Key Points Explained:
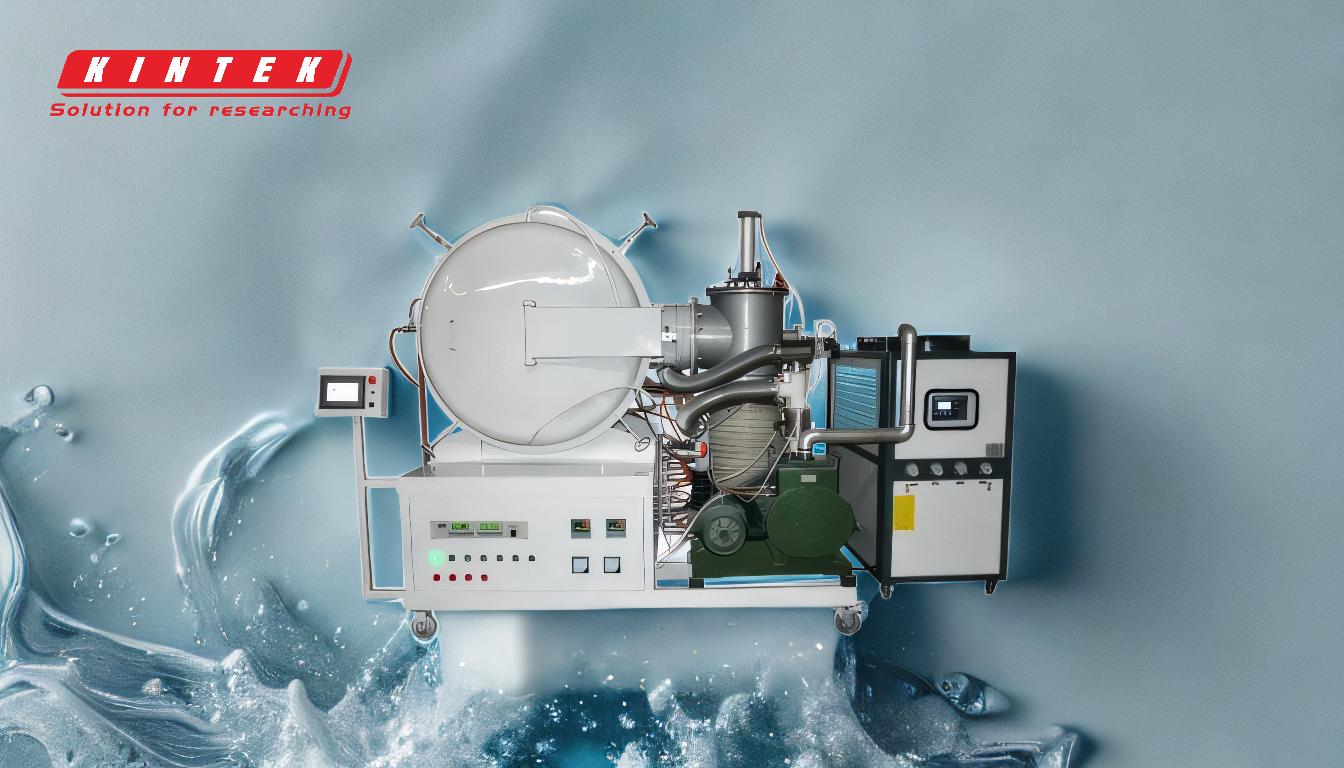
-
Process Overview:
- VAR involves melting a consumable metal electrode using a DC arc under vacuum conditions.
- The molten metal forms droplets that pass through an arc zone with temperatures reaching nearly 5000K.
- The metal re-solidifies in a water-cooled copper mold, producing a refined ingot.
-
Key Components:
- Consumable Electrode: The starting material, typically an impure alloy, which is melted during the process.
- DC Arc: Provides the intense heat required to melt the electrode.
- Vacuum Environment: Prevents contamination by outside air and facilitates the removal of impurities.
- Water-Cooled Copper Mold: Ensures controlled solidification of the molten metal.
-
Metallurgical Benefits:
- Purification: The vacuum environment reduces gas content (e.g., hydrogen) and removes low-melting-point impurities like lead, bismuth, and silver.
- Improved Crystal Structure: Controlled solidification leads to a more uniform and refined microstructure.
- Enhanced Performance: The process improves mechanical properties such as strength, ductility, and fatigue resistance.
-
Applications:
- Reactive Metals: VAR is ideal for refining reactive metals like titanium and zirconium, which are prone to contamination in conventional processes.
- Steels and Superalloys: The process is widely used to produce high-performance steels and superalloys for aerospace, energy, and medical applications.
- Refractory Metals: VAR is suitable for refractory metals and their alloys, which require high-purity and controlled solidification.
-
Advantages:
- Slag-Free Process: Unlike other refining methods, VAR does not use slag, reducing the risk of inclusion contamination.
- Minimized Active Element Loss: The process minimizes the burning of active elements like aluminum and titanium, preserving the alloy's composition.
- Denitrification Ability: VAR effectively removes nitrogen from the metal, further enhancing its purity.
-
Process Control:
- Energy Concentration: The DC arc provides highly concentrated energy, enabling precise control over the melting process.
- Solidification Rate: The water-cooled mold allows for controlled solidification, ensuring a uniform and defect-free ingot.
-
Industrial Significance:
- VAR is critical for producing high-performance materials used in demanding applications such as jet engines, gas turbines, and biomedical implants.
- The process's ability to refine and purify metals makes it indispensable in industries where material quality and reliability are paramount.
By combining vacuum conditions, high-temperature arc melting, and controlled solidification, VAR achieves unparalleled levels of metal refinement and performance enhancement, making it a cornerstone of modern metallurgy.
Summary Table:
Aspect | Details |
---|---|
Process | Melts a consumable electrode under vacuum using a DC arc. |
Key Components | Consumable electrode, DC arc, vacuum environment, water-cooled copper mold. |
Metallurgical Benefits | Purification, improved crystal structure, enhanced mechanical properties. |
Applications | Reactive metals (titanium, zirconium), steels, superalloys, refractory metals. |
Advantages | Slag-free, minimized active element loss, denitrification ability. |
Industrial Significance | Critical for aerospace, energy, and biomedical applications. |
Learn how Vacuum Arc Remelting can elevate your material quality—contact our experts today!