Thin film deposition is a critical process in materials science, involving the application of a thin layer of material onto a substrate. This process is essential for creating films with specific properties tailored for various applications, such as improving tribological behavior, enhancing optics, and upgrading aesthetics. The physical deposition of thin films, particularly through methods like Physical Vapor Deposition (PVD), involves thermodynamic or mechanical processes typically conducted in low-pressure environments to ensure functional and accurate results. The process includes several phases such as adsorption, surface diffusion, and nucleation, which are influenced by the material and substrate properties, as well as the deposition method and parameters. The choice of deposition source, such as ion beam deposition sources or magnetron sputtering cathodes, depends on the materials to be deposited and the desired film properties.
Key Points Explained:
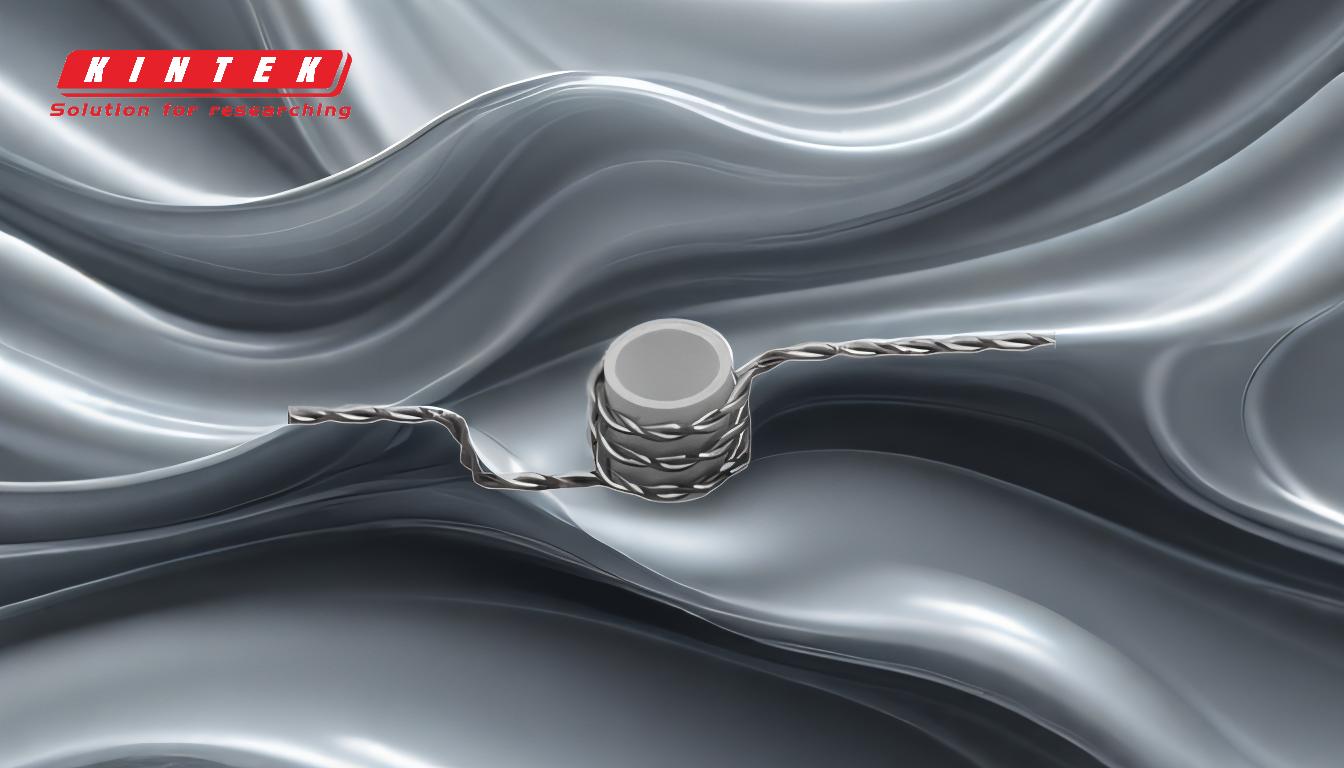
-
Overview of Thin Film Deposition:
- Thin film deposition involves applying a thin layer of material onto a substrate within a vacuum chamber.
- This process is crucial for creating films with specific properties for various applications, including tribological improvements, optical enhancements, and aesthetic upgrades.
-
Physical Deposition Methods:
- Physical Vapor Deposition (PVD) is a common method for thin film deposition, utilizing thermodynamic or mechanical processes.
- These methods typically require low-pressure environments to achieve functional and accurate results.
-
Phases of Thin Film Deposition:
- Adsorption: The initial phase where the material adheres to the substrate surface.
- Surface Diffusion: The movement of adsorbed atoms or molecules across the substrate surface.
- Nucleation: The formation of stable nuclei on the substrate, leading to the growth of the thin film.
- These phases are influenced by the material and substrate properties, as well as the deposition method and parameters.
-
Deposition Sources:
- Various sources are used for thin film deposition, including ion beam deposition sources, magnetron sputtering cathodes, thermal evaporators, and electron beam evaporators.
- The choice of source depends on the materials to be deposited and the desired film properties.
-
Materials Used in Thin Film Deposition:
- Common materials include metals, oxides, and compounds, each with specific advantages and disadvantages.
- The selection of materials is based on the intended application and desired film properties.
-
Applications of Thin Film Devices:
- Thin film devices are significant in materials science due to their precise manufacturing processes.
- They are used in a wide range of applications, from advanced batteries to luxury fabrics woven with gold and silver thin films.
-
Process Optimization:
- The deposition process may involve additional steps such as annealing or heat treatment to modify film properties.
- Analysis of film properties is conducted to refine the deposition process and achieve the desired outcomes.
By understanding these key points, one can appreciate the complexity and importance of the physical deposition of thin films in modern materials science and technology.
Summary Table:
Aspect | Details |
---|---|
Overview | Application of a thin material layer onto a substrate in a vacuum chamber. |
Methods | Physical Vapor Deposition (PVD), using thermodynamic/mechanical processes. |
Phases | Adsorption, surface diffusion, nucleation. |
Deposition Sources | Ion beam, magnetron sputtering, thermal/electron beam evaporators. |
Materials | Metals, oxides, compounds, tailored for specific applications. |
Applications | Tribology, optics, aesthetics, advanced batteries, luxury fabrics. |
Optimization | Annealing, heat treatment, and film property analysis for refinement. |
Discover how physical deposition of thin films can revolutionize your applications—contact our experts today!