Magnetron sputtering is a physical vapor deposition (PVD) technique widely used for thin film deposition in various industries, including semiconductors, optics, and microelectronics. It involves the use of magnetic fields to control the movement of charged particles, enabling efficient and high-quality film deposition. The process relies on the interaction between a magnetic field, a plasma, and a target material, which is bombarded by ions to eject atoms that then deposit onto a substrate. Key advantages include compatibility with a wide range of materials, the ability to deposit alloys and compounds without altering their composition, and the capability to coat large surfaces with strong adhesion. The process is highly controllable, with parameters such as target power density, gas pressure, and substrate temperature playing critical roles in determining the quality and properties of the deposited films.
Key Points Explained:
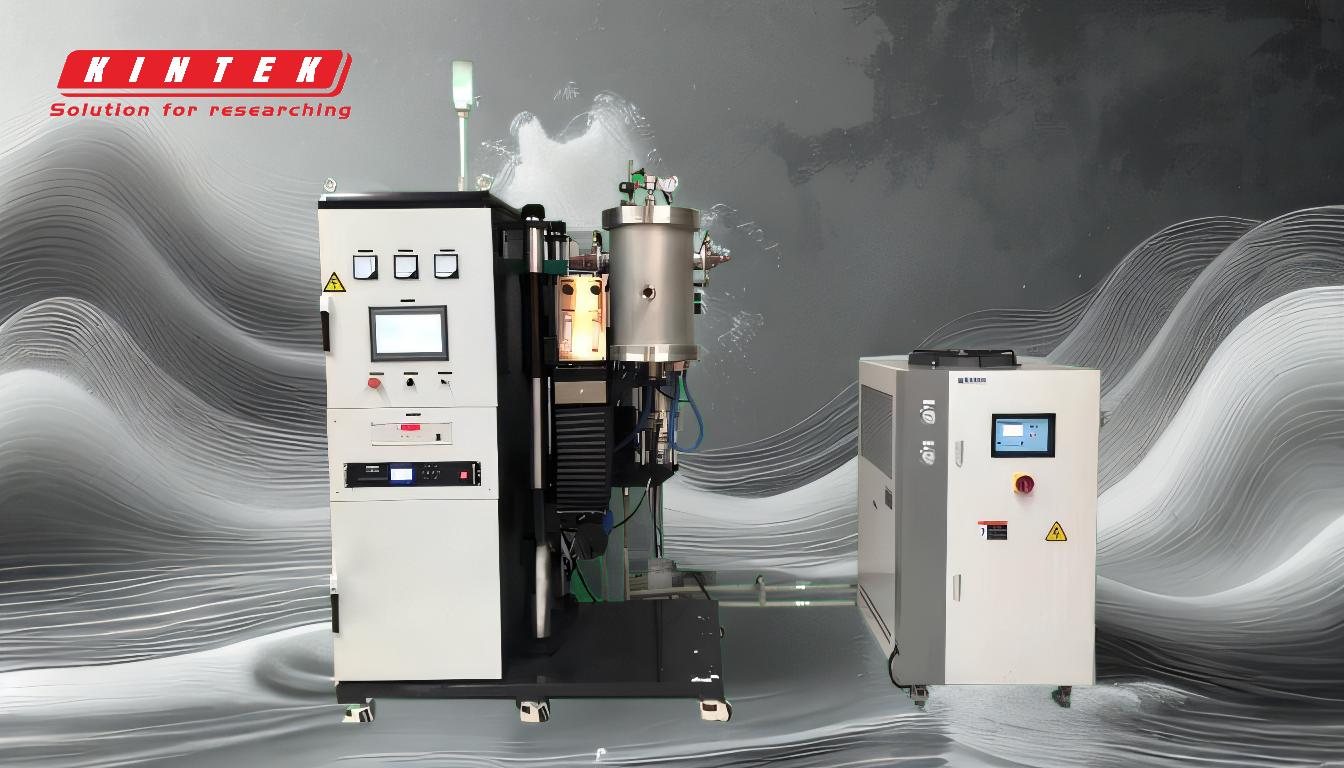
-
Basic Principles of Magnetron Sputtering:
- Magnetron sputtering is a PVD process where a target material is bombarded by ions in a plasma, causing atoms to be ejected and deposited onto a substrate.
- The process relies on a combination of electric and magnetic fields to confine electrons near the target, enhancing the ionization of the sputtering gas (typically argon) and increasing the efficiency of the deposition process.
-
Role of Magnetic Fields:
- Magnets placed behind the cathode create a magnetic field that traps electrons, preventing them from bombarding the substrate and increasing the density of the plasma near the target.
- This confinement of electrons enhances the ionization of the sputtering gas, leading to a higher rate of ion bombardment on the target and more efficient sputtering.
-
Plasma Formation and Ion Bombardment:
- A high voltage is applied to the target, creating a plasma near its surface. The plasma consists of argon gas atoms, argon ions, and free electrons.
- Electrons in the plasma collide with argon atoms, ionizing them and creating positively charged ions. These ions are then accelerated toward the negatively charged target, where they collide with the target material, ejecting atoms.
-
Sputtering Process and Film Deposition:
- When ions collide with the target, they transfer energy to the target atoms. If the energy transferred exceeds the binding energy of the target atoms, they are ejected from the surface.
- The ejected atoms travel through the vacuum chamber and deposit onto the substrate, forming a thin film. The properties of the film, such as thickness, uniformity, and adhesion, depend on the sputtering conditions.
-
Key Parameters Influencing the Process:
- Target Power Density: Determines the rate of ion bombardment and the energy of the ejected atoms.
- Gas Pressure: Affects the mean free path of the ejected atoms and the density of the plasma.
- Substrate Temperature: Influences the mobility of the deposited atoms on the substrate, affecting film quality and adhesion.
- Deposition Rate: Controlled by the power applied to the target and the gas pressure, it determines how quickly the film is deposited.
-
Advantages of Magnetron Sputtering:
- Versatility: Can deposit a wide range of materials, including metals, alloys, and compounds, without altering their composition.
- High Melting Point Materials: Suitable for materials that are difficult to melt or evaporate using other methods.
- Strong Adhesion: Produces films with excellent adhesion to the substrate, making it ideal for applications requiring durable coatings.
-
Applications of Magnetron Sputtering:
- Semiconductors: Used to deposit thin films for integrated circuits and other electronic components.
- Optical Devices: Creates films with specific optical properties, such as anti-reflective coatings and filters.
- Decorative Coatings: Used in the production of decorative films for consumer products.
- Machining Industry: Provides wear-resistant and corrosion-resistant coatings for tools and components.
-
Physics of Sputtering:
- The process involves the transfer of kinetic energy from ions to target atoms. If the energy transferred exceeds the binding energy of the target atoms, they are ejected from the surface.
- Collision cascades occur when primary recoil atoms collide with neighboring atoms, leading to further ejections. Sputtering occurs when the energy transferred normal to the surface exceeds about three times the surface binding energy.
By understanding these key points, one can appreciate the complexity and versatility of magnetron sputtering, making it a valuable technique for thin film deposition in various industrial applications.
Summary Table:
Key Aspect | Description |
---|---|
Basic Principles | A PVD process where ions bombard a target, ejecting atoms for deposition. |
Role of Magnetic Fields | Confines electrons, enhancing plasma density and ion bombardment efficiency. |
Plasma Formation | Argon gas ionizes, creating a plasma that accelerates ions toward the target. |
Sputtering Process | Ejected atoms deposit onto a substrate, forming a thin film. |
Key Parameters | Target power density, gas pressure, substrate temperature, and deposition rate. |
Advantages | Versatility, strong adhesion, and compatibility with high-melting-point materials. |
Applications | Semiconductors, optical devices, decorative coatings, and machining industry. |
Discover how magnetron sputtering can elevate your thin film applications—contact our experts today!