Plasma arc technology is a cutting-edge method used in various industrial applications, particularly in melting and processing materials. At its core, this technology utilizes a plasma arc furnace, which generates a low-temperature plasma flow through an electric arc heater, known as a plasmatron. This plasma flow delivers intense heat, enabling the melting of a wide range of substances. The technology is highly efficient and versatile, making it suitable for industries such as metallurgy, waste treatment, and advanced material synthesis.
Key Points Explained:
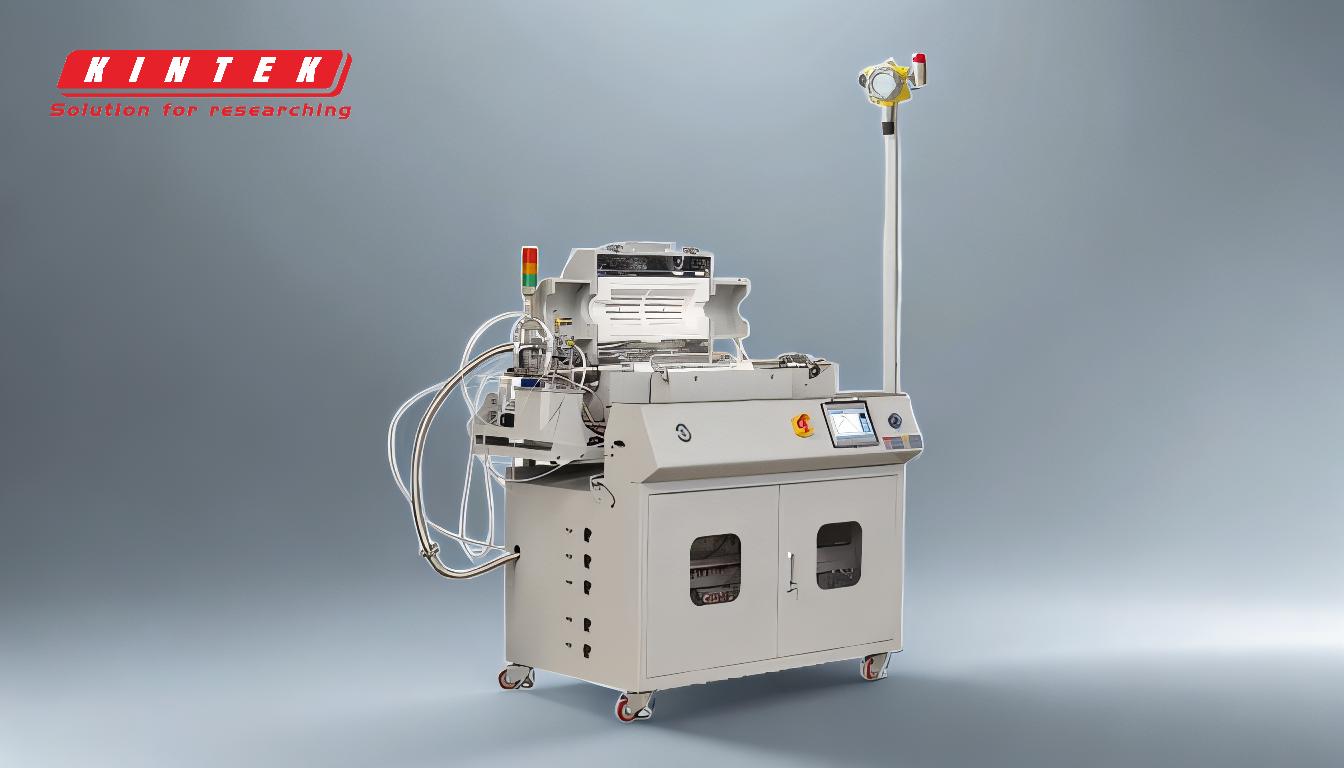
-
What is Plasma Arc Technology?
- Plasma arc technology involves the use of ionized gas (plasma) to generate extremely high temperatures. This is achieved by passing an electric current through a gas, creating a plasma arc. The plasma arc furnace is a key component of this technology, designed to harness and direct this energy for melting materials.
-
Components of a Plasma Arc Furnace
- Plasmatron (Electric Arc Heater): The heart of the system, the plasmatron generates the plasma by ionizing gas. It typically consists of electrodes and a gas supply system.
- Plasma Flow: The ionized gas, or plasma, flows out of the plasmatron at high temperatures, providing the heat required for melting.
- Furnace Chamber: This is where the material to be melted is placed. The chamber is designed to withstand high temperatures and contain the plasma flow.
-
How Plasma Arc Furnaces Work
- The process begins with the generation of plasma in the plasmatron. The gas (often argon, nitrogen, or a mixture) is ionized by an electric arc, creating a plasma flow.
- This plasma is then directed into the furnace chamber, where it transfers its heat to the material, causing it to melt.
- The temperature of the plasma can be precisely controlled, allowing for the melting of a wide range of materials, from metals to ceramics.
-
Applications of Plasma Arc Technology
- Metallurgy: Used for melting and refining metals, including steel, titanium, and other alloys.
- Waste Treatment: Plasma arc furnaces can be used to safely dispose of hazardous waste by converting it into inert slag and syngas.
- Material Synthesis: Advanced materials, such as nanoparticles and high-purity metals, can be synthesized using plasma arc technology.
-
Advantages of Plasma Arc Furnaces
- High Efficiency: Plasma arc furnaces can achieve very high temperatures, making them highly efficient for melting and processing materials.
- Versatility: They can handle a wide range of materials, including those that are difficult to melt using conventional methods.
- Environmental Benefits: Plasma arc technology can reduce emissions and waste, making it a more environmentally friendly option compared to traditional furnaces.
-
Challenges and Considerations
- Cost: The initial investment for a plasma arc furnace can be high, though this is often offset by the long-term savings in energy and material efficiency.
- Maintenance: Regular maintenance of the plasmatron and furnace chamber is required to ensure optimal performance.
- Safety: Handling high-temperature plasma requires strict safety protocols to protect operators and equipment.
In summary, plasma arc technology, particularly through the use of a plasma arc furnace, represents a significant advancement in material processing. Its ability to generate and control high-temperature plasma makes it an invaluable tool in modern industry, offering both efficiency and versatility.
Summary Table:
Aspect | Details |
---|---|
What is it? | Uses ionized gas (plasma) to generate high temperatures for melting materials. |
Key Components | Plasmatron, plasma flow, furnace chamber. |
How it Works | Gas is ionized to create plasma, which transfers heat to melt materials. |
Applications | Metallurgy, waste treatment, advanced material synthesis. |
Advantages | High efficiency, versatility, environmental benefits. |
Challenges | High initial cost, maintenance, and safety considerations. |
Ready to explore how plasma arc technology can transform your industrial processes? Contact us today for expert guidance!