Spark Plasma Sintering (SPS), also known as plasma activation sintering or discharge plasma sintering, is an advanced powder metallurgy technique that combines pulsed direct electric current, uniaxial pressure, and plasma activation to sinter materials rapidly and efficiently. This method is particularly effective for producing dense materials with fine grain structures at lower temperatures and shorter sintering times compared to conventional methods. It is widely used for sintering ceramics, metals, intermetallic compounds, and composites, making it ideal for research and development of new materials. The process involves the generation of plasma between powder particles, which removes surface impurities and activates particle surfaces, leading to enhanced sintering quality and efficiency.
Key Points Explained:
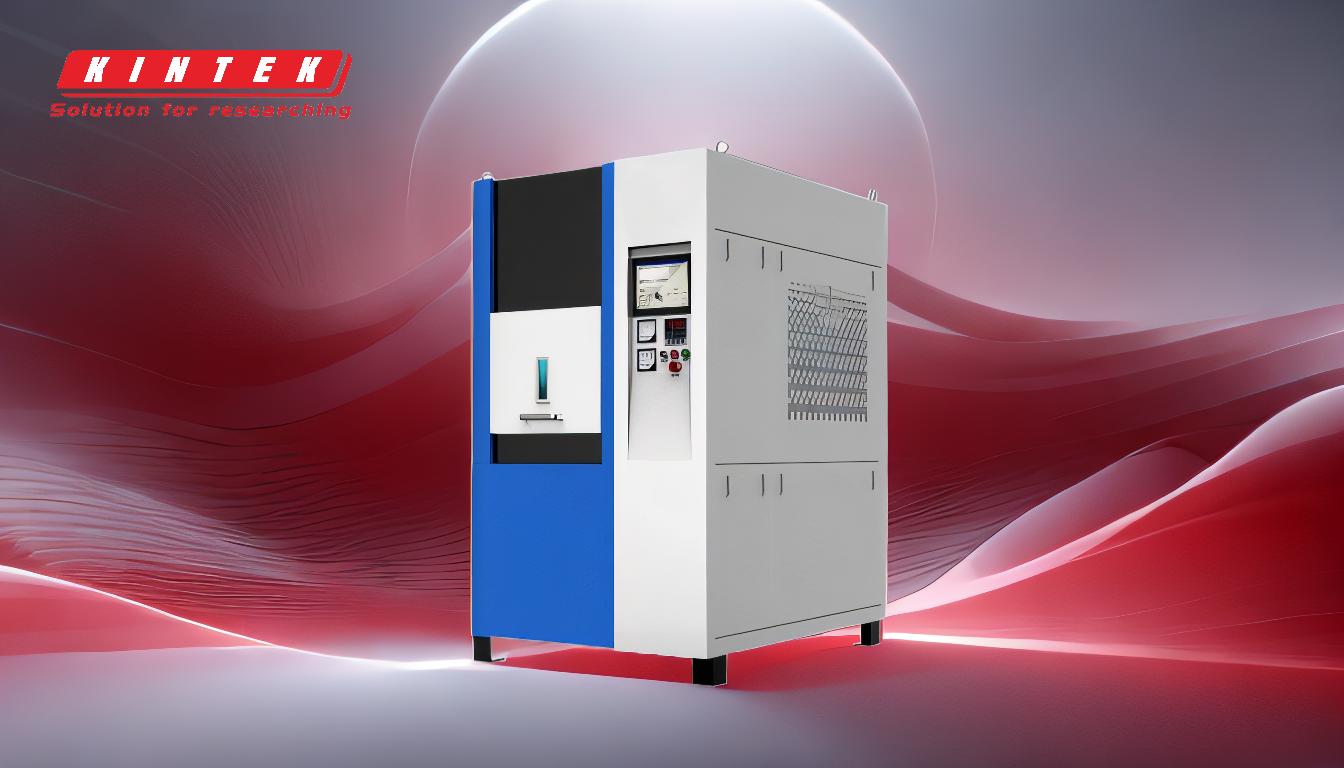
-
Definition and Mechanism of Spark Plasma Sintering (SPS):
- SPS is a sintering technique that uses pulsed direct electric current applied through electrodes in a conductive graphite die, along with uniaxial pressure.
- The electric current generates plasma between powder particles, causing micro-discharges that remove surface impurities like oxide films and adsorbed gases.
- The process activates particle surfaces through heat and strain energy, enabling rapid sintering in tens of seconds to minutes.
-
Advantages of SPS:
- Fast Heating and Cooling Rates: SPS achieves rapid heating and cooling, reducing processing time significantly.
- Lower Sintering Temperatures: Materials can be sintered at lower temperatures compared to conventional methods, preserving material properties.
- High Material Density: The process produces materials with high density and fine, uniform grain structures.
- Controlled Parameters: External pressure and sintering atmosphere can be precisely controlled, enhancing material quality.
- Versatility: Suitable for a wide range of materials, including ceramics, metals, intermetallic compounds, and composites.
-
Applications of SPS:
- Material Research and Development: Ideal for preparing small quantities of new materials with high efficiency.
- Ceramics and Composites: Used for sintering advanced ceramics like silicon carbide (SiC) with sintering aids (e.g., Al2O3 and Y2O3).
- Refractory Materials: Effective for sintering diamond and other hard-to-sinter materials.
- Intermetallic Compounds and Cermets: Enables the production of high-performance materials with tailored properties.
-
Comparison with Other Sintering Techniques:
- Conventional Sintering: Relies on thermal energy alone, requiring higher temperatures and longer times.
- Microwave Sintering: Uses microwaves for faster heating but lacks the plasma activation and pressure application of SPS.
- Hot Isostatic Pressing (HIP): Applies high pressure and temperature but is slower and less efficient than SPS.
- SPS stands out due to its integration of plasma activation, resistance heating, and pressure, enabling rapid and high-quality sintering.
-
Process Details:
- Plasma Activation: Micro-discharges between particles generate plasma, which cleans and activates particle surfaces.
- Joule Heating: Electric current produces localized heat at particle contact points, promoting thermal and electrical diffusion.
- Uniaxial Pressure: Applied pressure enhances particle bonding and densification.
- Rapid Cooling: After sintering, the material is cooled quickly to preserve its microstructure.
-
Material Examples:
- Silicon Carbide (SiC): Sintered with Al2O3 and Y2O3 aids to produce dense ceramics.
- Metals and Alloys: Used for sintering refractory metals and intermetallic compounds.
- Cermets and Composites: SPS is effective for producing materials with tailored mechanical and thermal properties.
-
Suitability for R&D:
- SPS is particularly advantageous for research and development due to its ability to produce small quantities of high-quality materials quickly.
- Its controlled parameters and rapid processing make it ideal for exploring new material compositions and properties.
In summary, Spark Plasma Sintering is a cutting-edge technique that combines electrical, thermal, and mechanical energy to sinter materials rapidly and efficiently. Its ability to produce dense, high-quality materials at lower temperatures and shorter times makes it a valuable tool for both industrial applications and material research.
Summary Table:
Aspect | Details |
---|---|
Definition | Advanced sintering technique using pulsed electric current, pressure, and plasma activation. |
Advantages | Fast heating/cooling, lower sintering temperatures, high density, controlled parameters, versatility. |
Applications | Ceramics, metals, intermetallic compounds, composites, R&D of new materials. |
Comparison | Faster and more efficient than conventional, microwave, and HIP sintering. |
Process Details | Plasma activation, Joule heating, uniaxial pressure, rapid cooling. |
Material Examples | Silicon carbide (SiC), refractory metals, cermets, composites. |
Suitability for R&D | Ideal for producing small quantities of high-quality materials quickly. |
Learn how Spark Plasma Sintering can transform your material research—contact our experts today!