Vacuum sintering is a critical process in material science, particularly for enhancing the purity and performance of metal powders by sintering them in a vacuum environment. This process prevents oxidation and contamination, ensuring high-quality sintered parts. The vacuum pressure plays a pivotal role in this process, as it determines the effectiveness of the sintering. Typically, the vacuum system in a vacuum sintering furnace achieves a pressure of around 7 × 10^-3 Pa, which is essential for optimal sintering conditions. This pressure is maintained using a combination of vacuum valves, mechanical pumps, diffusion pumps, and Roots pumps.
Key Points Explained:
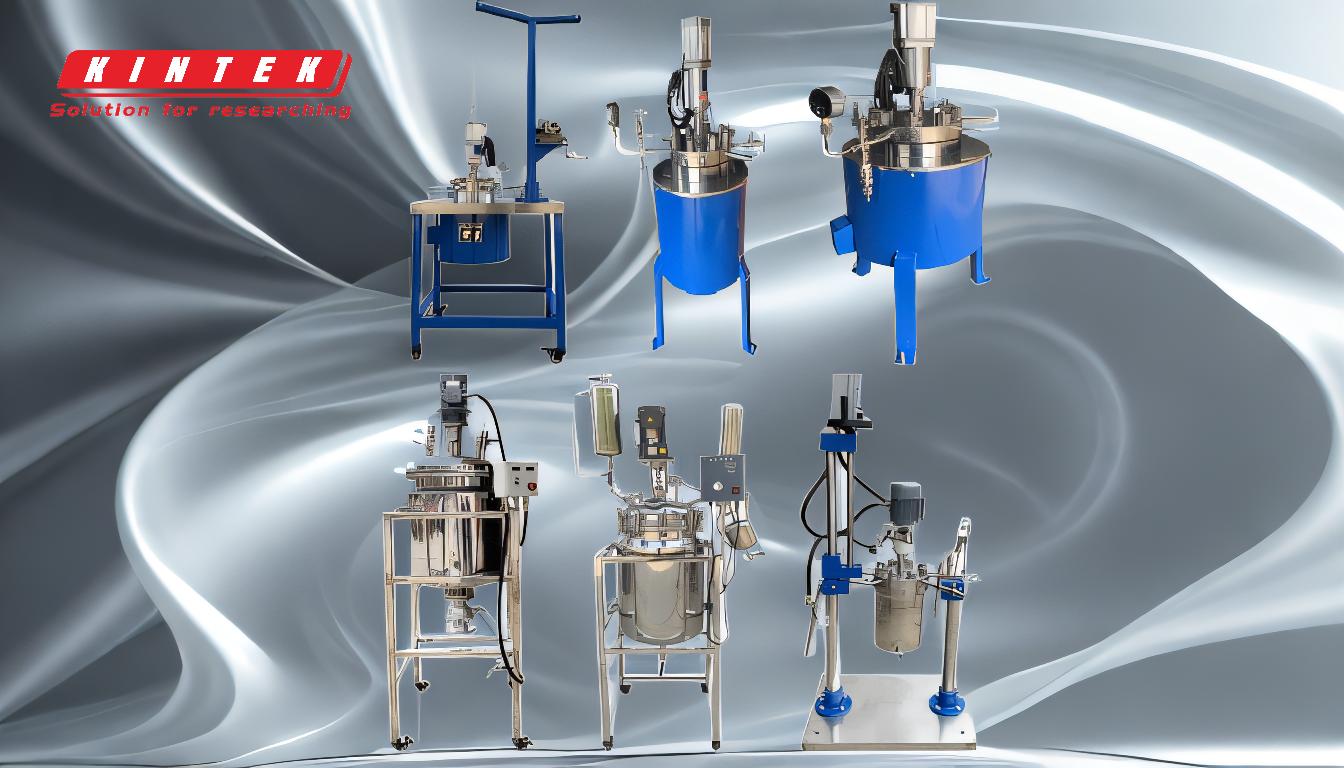
-
Purpose of Vacuum Sintering:
- Vacuum sintering is used to sinter metal powder products by heating them in a vacuum environment. This prevents oxidation and contamination, leading to higher purity and better performance of the final product. The absence of air and other reactive gases ensures that the material properties are not compromised during the sintering process.
-
Role of Vacuum Pressure:
- The vacuum pressure is a critical parameter in the sintering process. It ensures that the environment is free from impurities and reactive gases. The typical vacuum pressure achieved in a vacuum sintering furnace is around 7 × 10^-3 Pa. This level of vacuum is necessary to facilitate the proper adhesion and diffusion of metal powder grains, resulting in dense and high-quality sintered parts.
-
Components of the Vacuum System:
- The vacuum system in a vacuum sintering furnace includes several key components:
- Vacuum Valves: Control the flow of gases and maintain the vacuum pressure.
- Mechanical Pumps: Provide the initial vacuum by removing the bulk of the air and gases from the chamber.
- Diffusion Pumps: Further reduce the pressure to achieve the high vacuum levels required for sintering.
- Roots Pumps: Enhance the pumping speed and efficiency, especially in conjunction with mechanical pumps.
- These components work together to achieve and maintain the necessary vacuum pressure for effective sintering.
- The vacuum system in a vacuum sintering furnace includes several key components:
-
Importance of High Vacuum Levels:
- Achieving a high vacuum level (7 × 10^-3 Pa) is crucial for several reasons:
- Prevention of Oxidation: At high vacuum levels, the partial pressure of oxygen is extremely low, preventing oxidation of the metal powders.
- Reduction of Contaminants: High vacuum levels minimize the presence of impurities that could affect the material properties.
- Enhanced Diffusion: The high vacuum environment promotes better diffusion of metal powder grains, leading to stronger and more uniform sintered parts.
- Achieving a high vacuum level (7 × 10^-3 Pa) is crucial for several reasons:
-
Process of Vacuum Sintering:
- The vacuum sintering process involves several steps:
- Loading: Metal powder products are loaded into the vacuum sintering furnace.
- Evacuation: The chamber is evacuated to achieve the desired vacuum pressure.
- Heating: The furnace is heated to the sintering temperature, causing the metal powder grains to adhere and diffuse.
- Cooling: After sintering, the furnace is cooled, and the vacuum is released to retrieve the sintered parts.
- Each step is carefully controlled to ensure the quality and integrity of the final product.
- The vacuum sintering process involves several steps:
-
Applications of Vacuum Sintering:
- Vacuum sintering is widely used in various industries, including:
- Aerospace: For producing high-strength, lightweight components.
- Automotive: For manufacturing durable and precise parts.
- Medical: For creating biocompatible implants and devices.
- Electronics: For producing components with high electrical conductivity and thermal stability.
- The ability to produce high-purity, high-performance materials makes vacuum sintering indispensable in these fields.
- Vacuum sintering is widely used in various industries, including:
In summary, the pressure in a vacuum sintering furnace is a critical factor that directly impacts the quality and performance of the sintered materials. By maintaining a high vacuum level of around 7 × 10^-3 Pa, the process ensures that the materials are free from oxidation and contamination, leading to superior sintered parts. The components of the vacuum system, including vacuum valves, mechanical pumps, diffusion pumps, and Roots pumps, work in unison to achieve and maintain this pressure, making vacuum sintering a reliable and effective method for producing high-quality materials.
Summary Table:
Aspect | Details |
---|---|
Vacuum Pressure | 7 × 10^-3 Pa |
Purpose | Prevents oxidation and contamination, enhances material purity and performance |
Key Components | Vacuum valves, mechanical pumps, diffusion pumps, Roots pumps |
Applications | Aerospace, automotive, medical, electronics |
Benefits | High-strength, lightweight, durable, and biocompatible materials |
Discover how vacuum sintering can improve your material quality—contact our experts today!