The pressure in a hydrogenation reactor is a critical parameter that influences the reaction rate, efficiency, and safety of the process. Hydrogenation reactors typically operate under elevated pressures to enhance the reaction kinetics by increasing reactant concentration and collision frequency. The specific pressure range depends on the type of reactor (batch or continuous flow) and the application (e.g., edible fats, pharmaceuticals, or petroleum purification). High-pressure conditions are essential for achieving faster reactions, maintaining clean reaction profiles, and minimizing competing side reactions. Safety and accuracy are ensured through the integration of pressure reactors with gas dosing systems.
Key Points Explained:
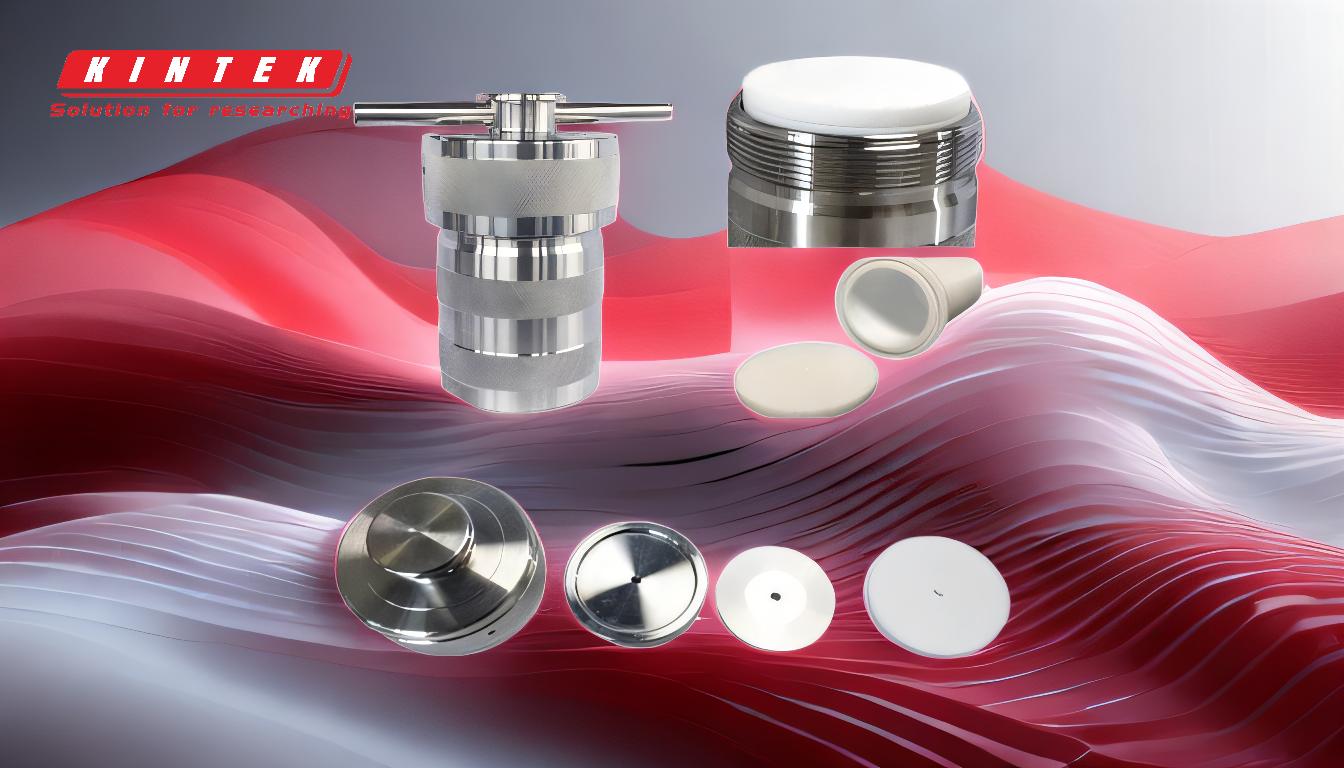
-
Importance of Pressure in Hydrogenation Reactors
- Pressure plays a crucial role in hydrogenation reactions by reducing the reaction volume and increasing the concentration of reactants, particularly hydrogen gas.
- Elevated pressure enhances the collision frequency between hydrogen molecules and the substrate, accelerating the reaction rate.
- High-pressure conditions are also beneficial for maintaining clean reaction profiles and reducing unwanted side reactions.
-
Types of Hydrogenation Reactors and Their Pressure Ranges
- Batch Hydrogenation Reactors: These are large pressurized vessels equipped with heating elements and agitators. They are commonly used in applications such as edible fat hydrogenation and pharmaceutical manufacturing. The pressure in batch reactors can vary widely depending on the specific process requirements.
- Continuous Flow/Tubular/Fixed Bed Reactors: These reactors are tube-shaped and contain fixed catalyst beds. They are often used in petroleum purification and pharmaceutical production. Continuous flow reactors typically operate under consistent pressure conditions optimized for the specific reaction.
-
Impact of Pressure on Reaction Kinetics
- Higher pressure increases the solubility of hydrogen gas in the reaction medium, which is essential for efficient hydrogenation.
- Pressure also influences the stability of intermediates and can affect the decomposition of reactants, particularly in reactions involving gas release.
- By optimizing pressure, reaction times can be significantly reduced while maintaining high yields and selectivity.
-
Safety and Control in High-Pressure Reactors
- The integration of pressure reactors with gas dosing systems ensures precise control over hydrogen gas introduction, enhancing safety and reproducibility.
- Advanced monitoring and control systems are employed to maintain stable pressure conditions and prevent over-pressurization, which could lead to safety hazards.
-
Applications and Pressure Requirements
- Edible Fats: Hydrogenation of vegetable oils typically requires moderate to high pressures to achieve the desired degree of saturation.
- Pharmaceuticals: Hydrogenation in pharmaceutical manufacturing often demands precise pressure control to ensure the purity and efficacy of the final product.
- Petroleum Purification: Continuous flow reactors used in petroleum refining operate under high pressures to facilitate efficient hydrogenation of hydrocarbons.
-
Considerations for Equipment Selection
- When selecting a hydrogenation reactor, it is essential to consider the pressure requirements of the specific application.
- Batch reactors offer flexibility for varying pressure conditions, while continuous flow reactors provide consistent pressure control for large-scale production.
- Safety features, such as pressure relief valves and automated control systems, are critical for operating high-pressure reactors.
By understanding the role of pressure in hydrogenation reactors and selecting the appropriate equipment, manufacturers can optimize reaction efficiency, ensure product quality, and maintain safe operating conditions.
Summary Table:
Key Aspect | Details |
---|---|
Importance of Pressure | Increases reactant concentration, accelerates reaction rates, reduces side reactions. |
Reactor Types | Batch reactors (flexible pressure) vs. continuous flow reactors (consistent pressure). |
Pressure Impact on Kinetics | Higher pressure improves hydrogen solubility, stabilizes intermediates, and reduces reaction time. |
Safety & Control | Gas dosing systems and automated controls ensure safe, reproducible operations. |
Applications | Edible fats (moderate-high pressure), pharmaceuticals (precise control), petroleum (high pressure). |
Equipment Selection | Choose based on pressure needs, safety features, and application requirements. |
Optimize your hydrogenation process with the right reactor—contact our experts today for tailored solutions!