The pressure range for magnetron sputtering is typically between 8 x 10^-2 to 2 x 10^-2 mbar. This range is critical for maintaining the ionization level, plasma density, and energy of sputtered atoms, which directly influence the quality and performance of the deposited thin films. The gas pressure affects the motion of sputtered ions, with higher pressures causing diffusive motion due to collisions with gas atoms, and lower pressures enabling high-energy ballistic impacts. Optimizing pressure ensures efficient sputtering and desired film properties.
Key Points Explained:
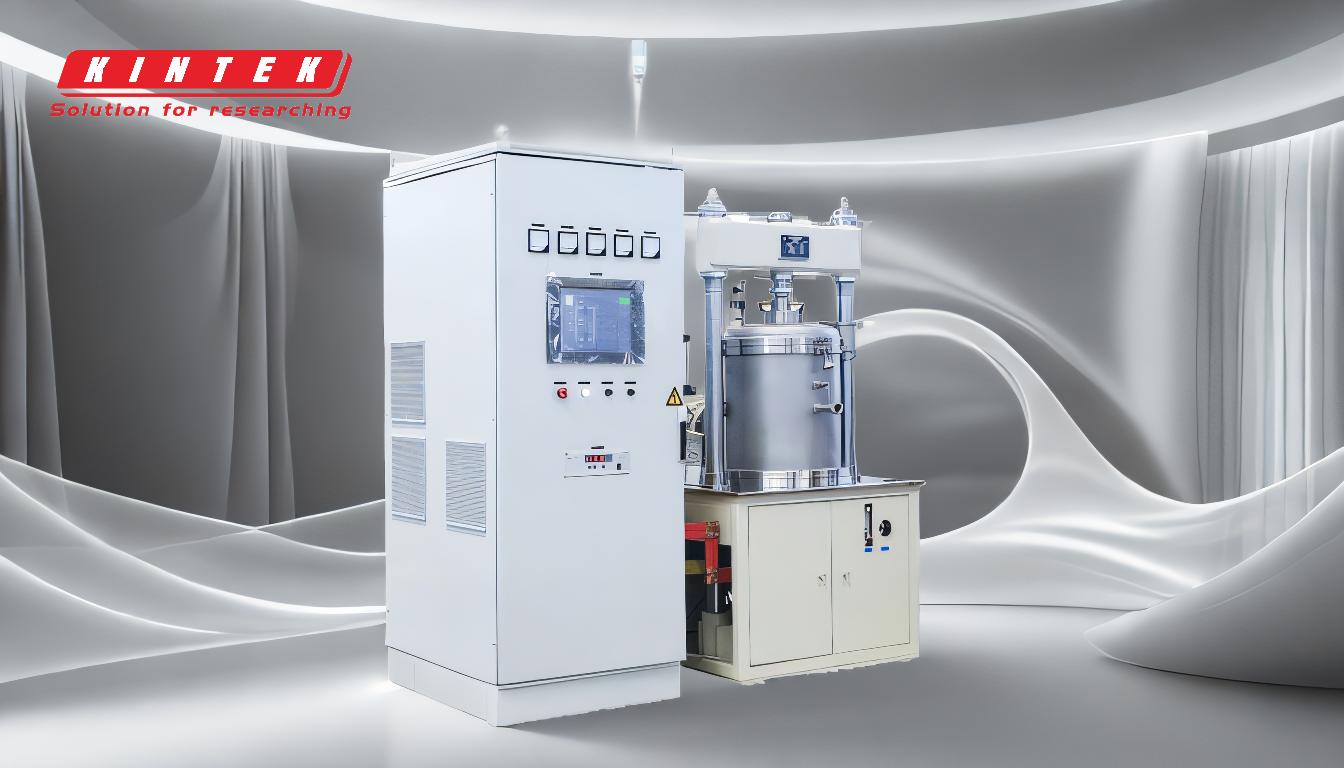
-
Typical Pressure Range for Magnetron Sputtering:
- The pressure range for magnetron sputtering is typically 8 x 10^-2 to 2 x 10^-2 mbar. This range is derived from the operational parameters of modern magnetron sputter coaters, which are designed to balance ionization, plasma density, and energy transfer for optimal film deposition.
-
Role of Gas Pressure in Sputtering:
- Gas pressure significantly influences the sputtering process:
- Higher Pressure: At higher gas pressures, sputtered ions collide more frequently with gas atoms, leading to diffusive motion. This moderates the energy of ions, causing them to reach the substrate or chamber walls after a random walk. This can result in lower-energy impacts and a more uniform deposition.
- Lower Pressure: At lower pressures, ions experience fewer collisions, allowing for high-energy ballistic impacts. This can enhance the energy of sputtered atoms, leading to denser and more adherent films.
- Gas pressure significantly influences the sputtering process:
-
Impact on Plasma Density and Ionization:
- Gas pressure directly affects plasma density and ionization levels, which are critical for the sputtering process. The formula for plasma density is:
[
n_e = \left(\frac{1}{\lambda_{De}^2}\right) \times \left(\frac{\omega^2 m_e \epsilon_0}{e^2}\right),
]
where:
- (n_e) = plasma density,
- (\lambda_{De}) = Debye length,
- (\omega) = angular frequency,
- (m_e) = electron mass,
- (\epsilon_0) = permittivity of free space,
- (e) = elementary charge.
- Higher pressures generally increase plasma density, while lower pressures may reduce it, affecting the overall sputtering efficiency.
- Gas pressure directly affects plasma density and ionization levels, which are critical for the sputtering process. The formula for plasma density is:
[
n_e = \left(\frac{1}{\lambda_{De}^2}\right) \times \left(\frac{\omega^2 m_e \epsilon_0}{e^2}\right),
]
where:
-
Optimization for Film Quality:
- The pressure range is optimized to achieve the desired film quality. For example:
- Uniformity: Higher pressures can improve film uniformity by promoting diffusive motion of sputtered atoms.
- Adhesion and Density: Lower pressures can enhance film adhesion and density by enabling high-energy impacts.
- The pressure range is optimized to achieve the desired film quality. For example:
-
Operational Considerations:
- Modern magnetron sputter coaters operate within the specified pressure range to maintain:
- Sputtering Voltage: 100V to 3kV,
- Current: 0 to 50mA,
- Deposition Rate: 0 to 25 nm/min,
- Grain Size: Less than 5nm,
- Temperature Rise: Less than 10°C.
- These parameters ensure consistent and high-quality thin film deposition.
- Modern magnetron sputter coaters operate within the specified pressure range to maintain:
-
Practical Implications for Equipment and Consumables Purchasers:
- When selecting or operating magnetron sputtering equipment, it is essential to:
- Ensure the system can maintain the required pressure range (8 x 10^-2 to 2 x 10^-2 mbar).
- Consider the impact of pressure on film properties (e.g., uniformity, adhesion, density).
- Optimize pressure settings based on the specific application and desired film characteristics.
- Monitor and control other critical parameters (e.g., voltage, current, deposition rate) to achieve consistent results.
- When selecting or operating magnetron sputtering equipment, it is essential to:
By understanding the pressure range and its effects, equipment and consumables purchasers can make informed decisions to optimize the sputtering process and achieve high-quality thin films.
Summary Table:
Aspect | Details |
---|---|
Pressure Range | 8 x 10^-2 to 2 x 10^-2 mbar |
Higher Pressure Effects | Diffusive motion, uniform deposition, lower-energy impacts |
Lower Pressure Effects | High-energy ballistic impacts, denser and more adherent films |
Plasma Density Formula | (n_e = \left(\frac{1}{\lambda_{De}^2}\right) \times \left(\frac{\omega^2 m_e \epsilon_0}{e^2}\right)) |
Operational Parameters | Voltage: 100V-3kV, Current: 0-50mA, Deposition Rate: 0-25 nm/min |
Need help optimizing your magnetron sputtering process? Contact our experts today!