Pressureless sintering is a manufacturing process that involves fusing particles together through heating without the application of external pressure. This method is particularly suitable for materials like metal-ceramic composites and ceramic powders. The process begins with the creation of ceramic powder compacts using techniques such as cold isostatic pressing, injection molding, or slip casting. These compacts are pre-sintered and machined to their final shape before being subjected to controlled heating. The heating process can be carried out using techniques like constant-rate heating (CRH), rate-controlled sintering (RCS), or two-step sintering (TSS), each influencing the microstructure and grain size of the final product. The absence of external pressure helps avoid density variations, making it ideal for producing uniform and high-quality ceramic components.
Key Points Explained:
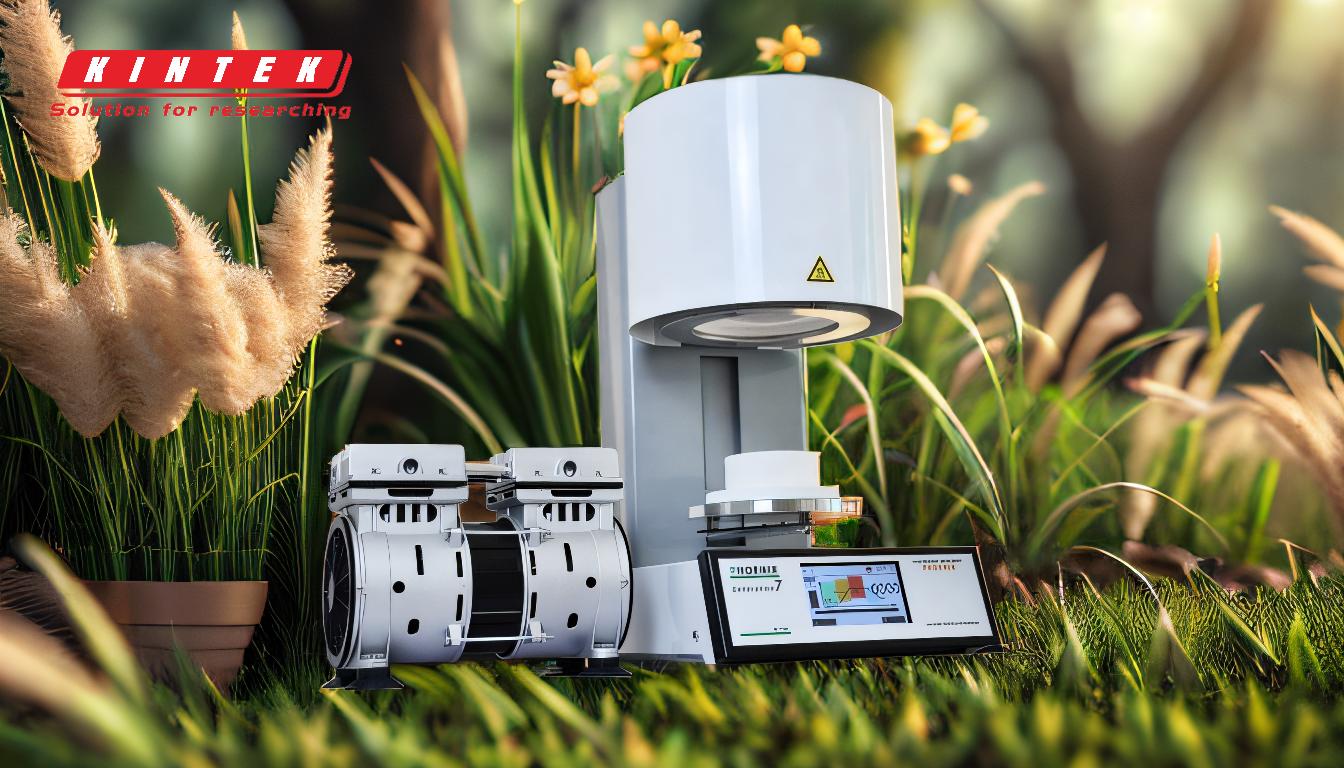
-
Definition of Pressureless Sintering:
- Pressureless sintering is a process where particles are fused together solely through heating, without the need for external pressure.
- This method is particularly effective for materials like metal-ceramic composites and ceramic powders.
-
Preparation of Ceramic Powder Compacts:
- The process begins with the creation of ceramic powder compacts using methods such as cold isostatic pressing, injection molding, or slip casting.
- These compacts are pre-sintered and machined to their final shape before the actual sintering process begins.
-
Heating Techniques:
- Constant-Rate Heating (CRH): The temperature is increased at a constant rate until the desired sintering temperature is reached.
- Rate-Controlled Sintering (RCS): The heating rate is adjusted based on the material's response to temperature changes, allowing for better control over the sintering process.
- Two-Step Sintering (TSS): The material is heated to a high temperature initially, followed by a lower temperature hold, which helps in achieving a fine-grained microstructure.
-
Microstructure and Grain Size:
- The final microstructure and grain size of the sintered product depend on the material used and the specific heating technique applied.
- Pressureless sintering helps in avoiding density variations, resulting in a more uniform and high-quality final product.
-
Advantages of Pressureless Sintering:
- Uniformity: The absence of external pressure helps in achieving a more uniform density throughout the material.
- Complex Shapes: It allows for the production of complex shapes and intricate designs that might be difficult to achieve with pressure-assisted sintering.
- Material Compatibility: Suitable for a wide range of materials, including metal-ceramic composites and various ceramic powders.
-
Applications:
- Pressureless sintering is widely used in the production of ceramic components for industries such as electronics, aerospace, and biomedical engineering.
- It is also used in the manufacturing of advanced materials like graded metal-ceramic composites and monolithic ceramic structures.
-
Comparison with Hot Press Sintering:
- Unlike hot press sintering, which involves the application of external pressure during the heating process, pressureless sintering relies solely on heat to fuse particles together.
- This difference makes pressureless sintering more suitable for applications where maintaining material integrity and avoiding density variations are critical.
By understanding these key points, one can appreciate the nuances of pressureless sintering and its advantages in producing high-quality, uniform ceramic components without the need for external pressure.
Summary Table:
Aspect | Details |
---|---|
Definition | Fusing particles through heating without external pressure. |
Materials | Metal-ceramic composites, ceramic powders. |
Preparation Techniques | Cold isostatic pressing, injection molding, slip casting. |
Heating Techniques | Constant-rate heating (CRH), rate-controlled sintering (RCS), two-step sintering (TSS). |
Advantages | Uniform density, complex shapes, material compatibility. |
Applications | Electronics, aerospace, biomedical engineering, advanced materials. |
Discover how pressureless sintering can enhance your ceramic production—contact our experts today!