DC magnetron sputtering is a widely used thin-film deposition technique that leverages a combination of electric and magnetic fields to enhance the sputtering process. It operates in a high-vacuum environment where a plasma is generated using an inert gas, typically argon. A high negative voltage is applied to the target material (cathode), creating a strong electric field that accelerates positively charged argon ions toward the target. When these ions collide with the target, they dislodge atoms from its surface, which then deposit onto a substrate to form a thin film. The key innovation in magnetron sputtering is the use of magnets behind the target, which trap electrons near the target surface, increasing plasma density and sputtering efficiency. This results in higher deposition rates, better film quality, and lower operating pressures compared to traditional sputtering methods.
Key Points Explained:
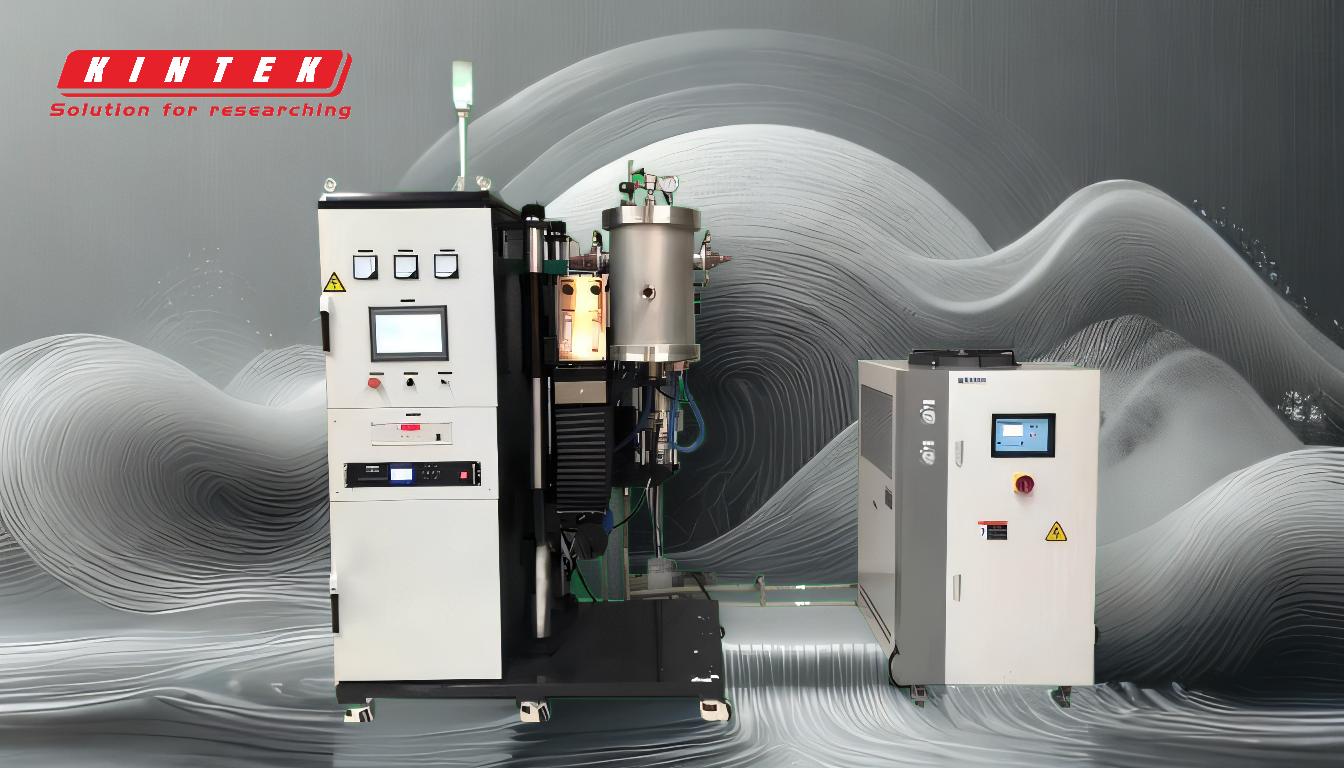
-
High Vacuum Environment:
- DC magnetron sputtering requires a high vacuum chamber to minimize contamination and ensure a controlled environment. The low-pressure environment allows for the efficient generation of plasma and reduces the likelihood of unwanted chemical reactions.
-
Plasma Generation:
- An inert gas, usually argon, is introduced into the chamber and ionized to form a plasma. The ionization process is initiated by applying a high negative voltage (typically around 300 V) between the cathode (target) and anode. This creates a strong electric field that accelerates argon ions toward the target.
-
Magnetic Field Configuration:
- Magnets are placed behind the target to create a magnetic field parallel to its surface. This magnetic field traps electrons in a circular trajectory near the target, increasing their residence time in the plasma. This enhances the ionization of gas molecules, leading to a higher density of argon ions and a more efficient sputtering process.
-
Sputtering Mechanism:
- Positively charged argon ions from the plasma collide with the negatively charged target surface. If the kinetic energy of the ions exceeds the surface binding energy of the target material (typically about three times the binding energy), atoms are ejected from the target. These ejected atoms travel through the vacuum and deposit onto the substrate, forming a thin film.
-
Advantages of Magnetron Sputtering:
- High Deposition Rates: The magnetic field increases plasma density, leading to faster sputtering and deposition rates.
- Low Operating Pressure: The process can be conducted at lower pressures, reducing energy consumption and improving film quality.
- Versatility: A wide range of materials, including metals, alloys, and ceramics, can be used as targets.
- Precision and Uniformity: The technique allows for precise control over film thickness and composition, making it suitable for high-precision applications.
- Industrial Scalability: Magnetron sputtering is well-suited for high-volume production due to its efficiency and ability to produce dense, well-adhered films.
-
Historical Context:
- Sputtering was first observed in the 1850s but became commercially viable in the 1940s with diode sputtering. However, diode sputtering had limitations, such as low deposition rates and high costs. Magnetron sputtering was introduced in 1974 as a significant improvement, offering higher deposition rates and broader applicability.
-
Applications:
- DC magnetron sputtering is used in various industries, including semiconductor manufacturing, optical coatings, and decorative coatings. Its ability to deposit high-quality, uniform films makes it ideal for applications requiring precise material properties.
By combining the principles of electric and magnetic fields, DC magnetron sputtering achieves a highly efficient and versatile thin-film deposition process. Its ability to operate at low pressures, produce high-quality films, and handle a wide range of materials makes it a cornerstone of modern materials science and industrial manufacturing.
Summary Table:
Key Aspect | Description |
---|---|
High Vacuum Environment | Ensures minimal contamination and controlled plasma generation. |
Plasma Generation | Argon gas ionized by a high negative voltage, creating a plasma for sputtering. |
Magnetic Field | Magnets trap electrons near the target, increasing plasma density and sputtering efficiency. |
Sputtering Mechanism | Argon ions collide with the target, ejecting atoms that deposit onto a substrate as a thin film. |
Advantages | High deposition rates, low operating pressure, versatility, precision, and scalability. |
Applications | Semiconductor manufacturing, optical coatings, decorative coatings, and more. |
Discover how DC magnetron sputtering can enhance your thin-film deposition process—contact our experts today!