Hot isostatic pressing (HIP) is a manufacturing process that combines high temperature and high pressure to improve the properties of materials, such as density, strength, and uniformity. The process involves placing parts or components in a heating chamber filled with inert gas, typically argon, which is then pressurized and heated. The simultaneous application of heat and pressure eliminates internal voids and pores, resulting in a denser and more uniform material. The process is widely used in industries like aerospace, automotive, and medical devices to enhance material performance and reduce defects. A related process, warm isostatic press, operates at lower temperatures but follows similar principles of uniform pressure application.
Key Points Explained:
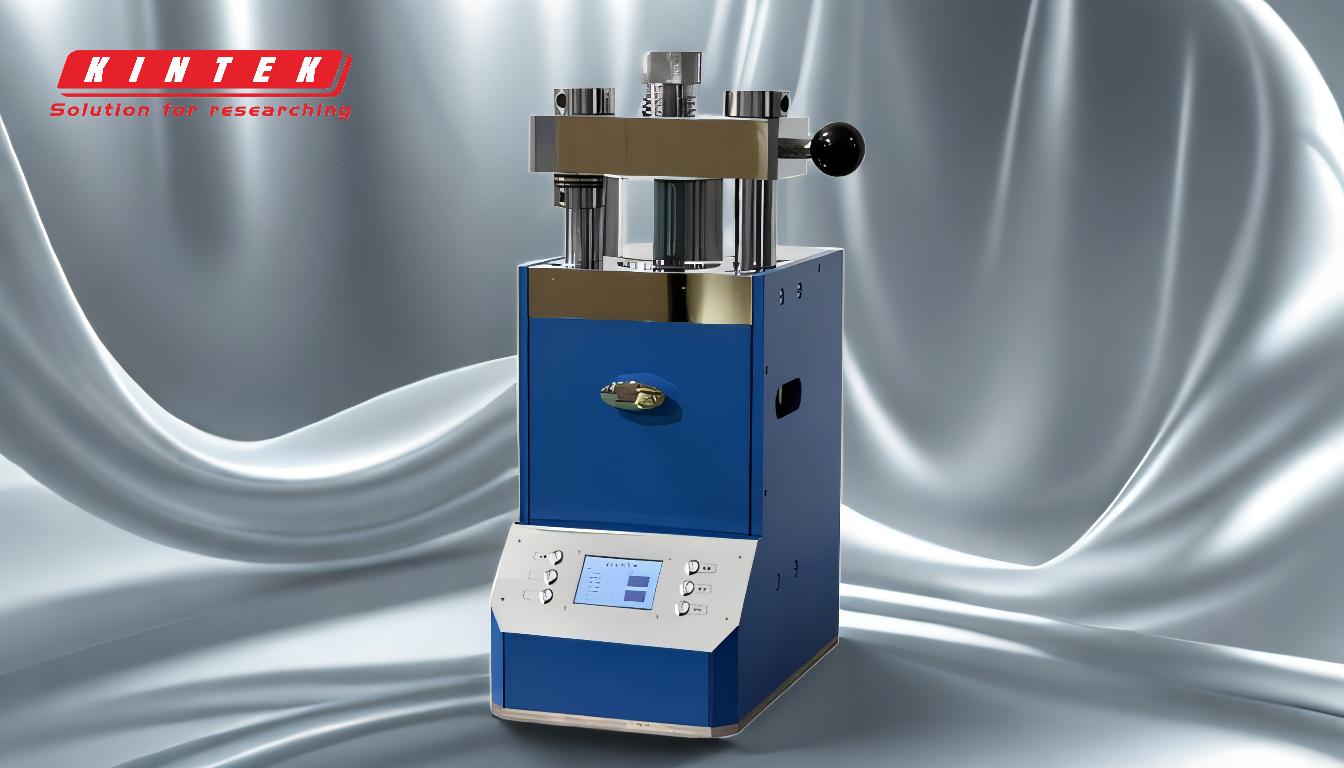
-
Principle of Hot Isostatic Pressing (HIP):
- HIP involves the simultaneous application of high temperature and high pressure to materials, typically using inert gases like argon. This process eliminates internal voids, pores, and defects, resulting in a denser and more uniform material structure. The uniform pressure ensures that the material is compressed equally from all directions, which is crucial for achieving consistent properties.
-
Process Steps:
- Loading: Parts or components are placed inside a sealed heating chamber.
- Pressurization: Inert gas, such as argon, is introduced and pressurized.
- Heating: The chamber is heated to a specific temperature, usually below the material's melting point.
- Monitoring: Temperature, pressure, and process time are closely controlled to achieve the desired material properties.
- Cooling and Depressurization: After the process, the chamber is depressurized and cooled to safely remove the parts.
-
Applications of HIP:
- HIP is used to bond or clad multiple materials, either in solid or powder form, enhancing their mechanical properties.
- It is often combined with 3D printing to reduce manufacturing time and costs while improving part quality.
- Industries such as aerospace, automotive, and medical devices rely on HIP to produce high-performance components with minimal defects.
-
Comparison with Warm Isostatic Pressing:
- A warm isostatic press operates at lower temperatures compared to HIP. It uses a heated liquid medium, which is continuously injected into a sealed pressing cylinder. The temperature is controlled using a heat generator, ensuring precise thermal conditions. This process is suitable for materials that require lower processing temperatures.
-
Advantages of HIP:
- Improved Material Properties: HIP increases density, strength, and uniformity by eliminating internal defects.
- Versatility: It can be applied to a wide range of materials, including metals, ceramics, and composites.
- Cost Efficiency: When combined with techniques like 3D printing, HIP reduces production costs and time.
-
Key Parameters:
- Temperature: Typically below the melting point of the material to avoid deformation.
- Pressure: Uniformly applied from all directions to ensure consistent compression.
- Process Time: Carefully controlled to achieve the desired material properties.
By understanding the principles and steps of hot isostatic pressing, manufacturers can leverage this process to produce high-quality components with enhanced performance characteristics. The related warm isostatic press offers an alternative for materials requiring lower processing temperatures, further expanding the applications of isostatic pressing technologies.
Summary Table:
Key Aspect | Details |
---|---|
Principle | Simultaneous high temperature and pressure to eliminate voids and defects |
Process Steps | Loading, pressurization, heating, monitoring, cooling/depressurization |
Applications | Aerospace, automotive, medical devices, 3D printing |
Advantages | Improved density, strength, uniformity, and cost efficiency |
Key Parameters | Temperature, pressure, process time |
Discover how hot isostatic pressing can transform your manufacturing process—contact us today!