The principle of mixing on an open two-roll mill revolves around the mechanical action of two counter-rotating rolls with different speeds, which generate shear and compression forces. These forces are essential for mixing rubber or plastic materials with additives. The rolls rotate towards each other, with one roll moving faster than the other, creating friction and shearing forces in the nip (gap) between the rolls. This process stretches and breaks the internal molecular chains of the material, ensuring uniform dispersion and mixing. The adjustable roll gap and speed ratio allow operators to control the intensity of the mixing process, achieving the desired material properties.
Key Points Explained:
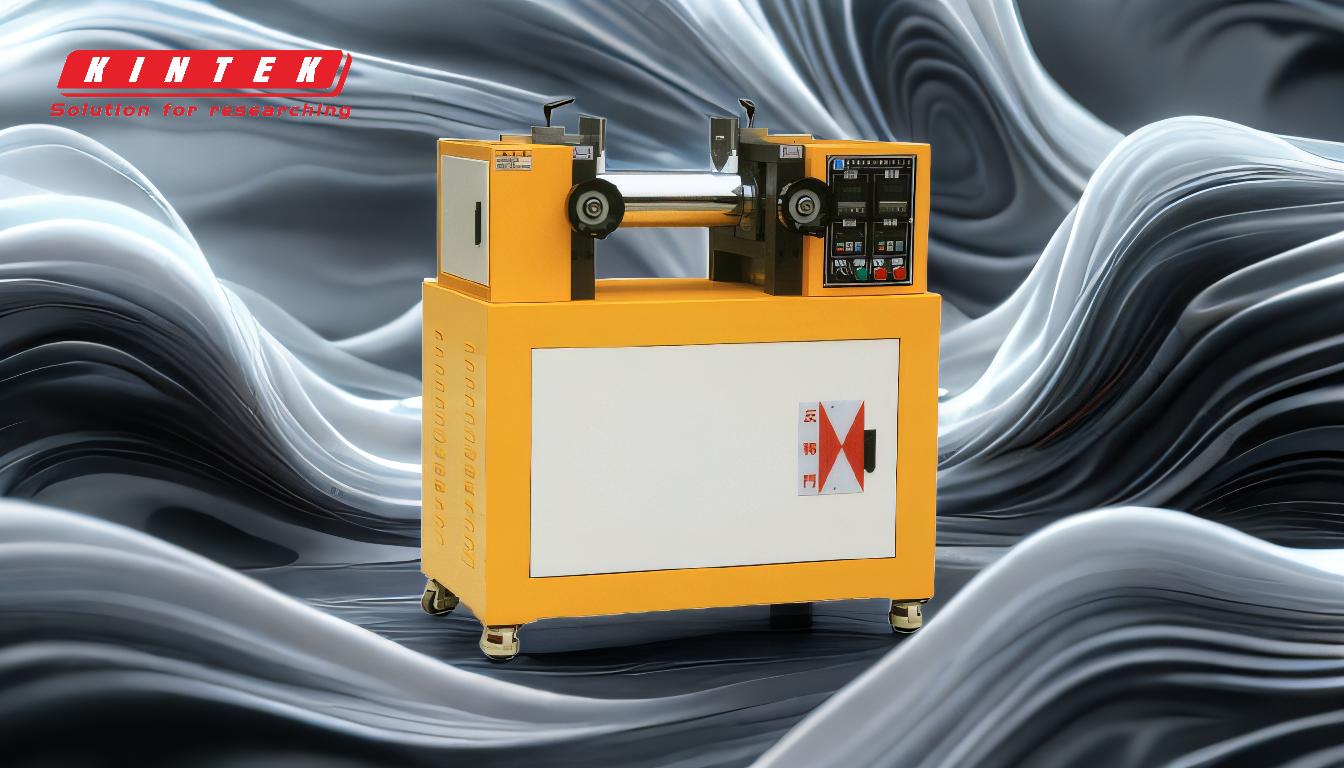
-
Counter-Rotating Rolls with Speed Differential:
- The two rolls rotate in opposite directions, with one roll running faster than the other. This speed difference (typically a ratio of 1.2:1) is critical for generating friction and shearing forces.
- The speed differential ensures that the material is subjected to both shear and compression, which are necessary for effective mixing.
-
Shear and Compression Forces:
- The opposing rotation and speed difference create a combined shear and compression force in the nip (gap) between the rolls. This force is essential for breaking down the material's internal structure and ensuring uniform mixing.
- The shear force stretches and breaks the macromolecular chains of the material, while the compression force ensures that the material is evenly distributed and compacted.
-
Adjustable Roll Gap:
- The distance between the two rolls can be adjusted by the operator. This adjustment allows control over the intensity of the shear and compression forces applied to the material.
- A smaller gap increases the shear force, which is useful for breaking down tougher materials, while a larger gap reduces the force, which is suitable for softer materials.
-
Heat Generation:
- The friction generated by the rotating rolls produces heat, which aids in the mixing process. The heat softens the material, making it easier to stretch and mix.
- The heat also helps in melting and blending additives, such as dyes or other chemicals, into the rubber or plastic.
-
Material Processing:
- The raw materials and additives are fed into the roll gap, where they are drawn in by the rotating rolls. The material is subjected to intense squeezing and shearing, which increases the contact area between the components.
- When the applied stress exceeds the material's allowable limit, the internal molecular chains are stretched and broken, leading to uniform dispersion and mixing.
-
Repetitive Mixing for Uniformity:
- The process of feeding the material through the roll gap is repeated multiple times until the desired mastication or mixing state is achieved. This ensures that the material is uniformly mixed and free of lumps or inconsistencies.
- The final product is a sheet-like compound that is ready for further processing or molding.
-
Applications in Rubber and Plastic Mixing:
- The two-roll mill is commonly used in the rubber and plastic industries for mixing raw materials with additives, such as curing agents, fillers, and dyes.
- The ability to control the speed ratio, roll gap, and heat generation makes the two-roll mill versatile for different types of materials and mixing requirements.
In summary, the principle of mixing on an open two-roll mill relies on the mechanical action of counter-rotating rolls with a speed differential, generating shear and compression forces. These forces, combined with adjustable roll gaps and heat generation, ensure effective mixing and dispersion of materials, resulting in a uniform and well-mixed final product.
Summary Table:
Key Feature | Description |
---|---|
Counter-Rotating Rolls | Rolls rotate in opposite directions with a speed differential (1.2:1 ratio). |
Shear and Compression Forces | Generates forces in the nip to stretch and break molecular chains for mixing. |
Adjustable Roll Gap | Controls shear intensity for tougher or softer materials. |
Heat Generation | Friction produces heat, softening materials and aiding additive blending. |
Material Processing | Raw materials are drawn into the roll gap, ensuring uniform dispersion. |
Repetitive Mixing | Repeated passes achieve uniform mixing and consistency. |
Applications | Used in rubber and plastic industries for mixing additives like dyes and fillers. |
Discover how an open two-roll mill can optimize your material mixing process—contact our experts today!
For more information on laboratory mill or optical material, visit our topic pages.