Physical Vapor Deposition (PVD) is a versatile thin film deposition technique used to create durable, high-performance coatings on various substrates. The process involves converting a solid precursor material into a vapor phase, which then condenses onto a substrate to form a thin film. This is achieved through methods such as thermal evaporation, sputtering, or other physical means, typically in a vacuum environment to minimize contamination. PVD coatings are known for their excellent adhesion, scratch resistance, and corrosion resistance, making them suitable for applications in industries like aerospace, electronics, and medical devices. The process is highly controllable, allowing precise management of film thickness and composition.
Key Points Explained:
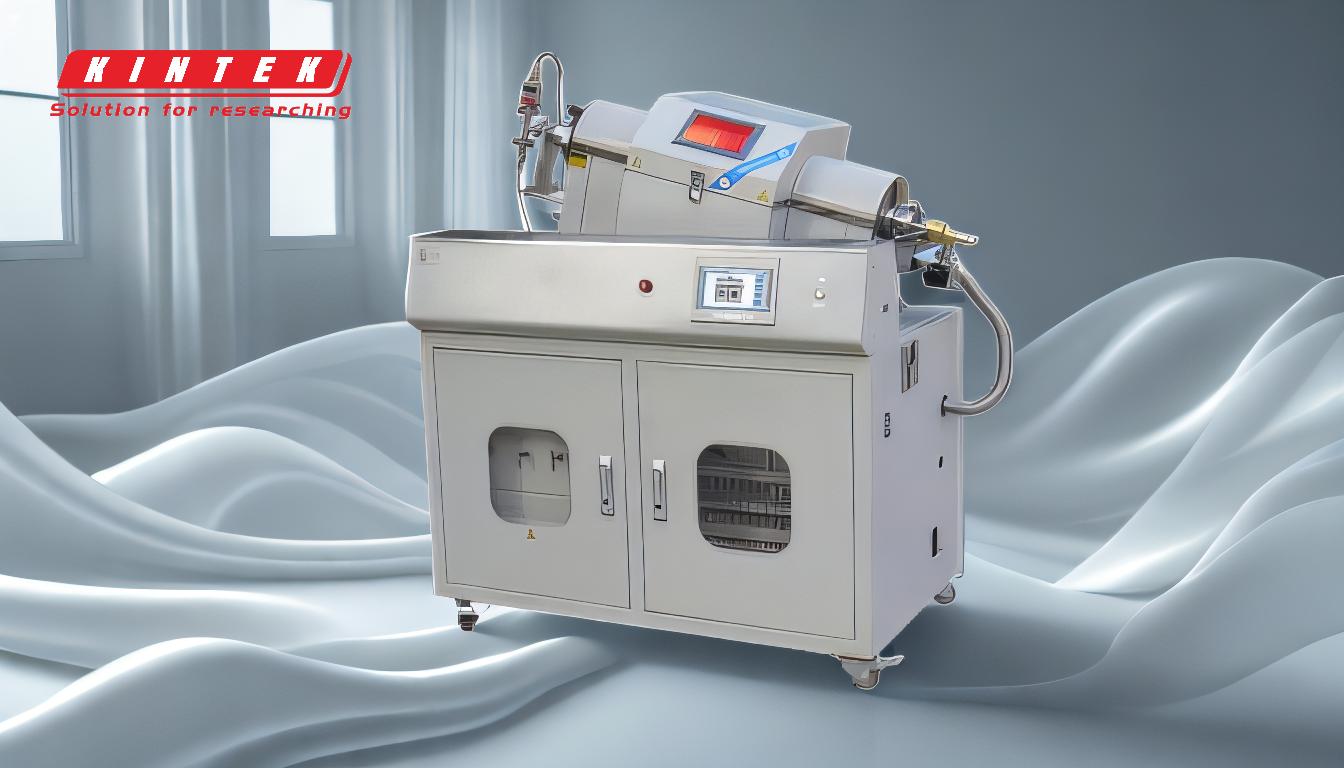
-
Basic Principle of PVD:
- PVD involves the transformation of a solid material into a vapor phase, which is then deposited onto a substrate to form a thin film.
- The process occurs in a vacuum or low-pressure environment to reduce interference from background gases and ensure high-quality coatings.
-
Steps in the PVD Process:
- Vaporization: The solid precursor material is gasified using methods such as thermal evaporation, sputtering, or laser ablation.
- Transport: The vaporized atoms or molecules travel through the reaction chamber.
- Deposition: The vapor condenses onto the substrate, forming a thin film with strong adhesion and uniform thickness.
-
Methods of PVD:
- Thermal Evaporation: The target material is heated to its evaporation point, and the vapor is deposited onto the substrate.
- Sputtering: High-energy ions bombard the target material, dislodging atoms that then deposit onto the substrate.
- Other Techniques: Includes arc vapor deposition and pulsed laser deposition, each suited for specific applications.
-
Advantages of PVD:
- Durability: PVD coatings are highly resistant to wear, scratches, and corrosion.
- Versatility: Can deposit a wide range of materials, including those with high melting points.
- Precision: Allows for precise control over film thickness and composition, often monitored using tools like quartz crystal rate monitors.
-
Applications of PVD:
- Industrial Coatings: Used for tools, molds, and machinery to enhance durability and performance.
- Electronics: Deposits thin films for semiconductors, sensors, and optical devices.
- Medical Devices: Provides biocompatible and wear-resistant coatings for implants and surgical instruments.
-
Key Considerations for PVD:
- Vacuum Environment: Essential for minimizing contamination and ensuring high-quality coatings.
- Material Compatibility: The choice of target material and substrate must align with the intended application.
- Process Control: Parameters like temperature, pressure, and deposition rate must be carefully managed to achieve desired film properties.
By understanding these key points, equipment and consumable purchasers can make informed decisions about selecting PVD systems and materials for their specific needs.
Summary Table:
Aspect | Details |
---|---|
Basic Principle | Converts solid material into vapor, condensing into a thin film on a substrate. |
Steps in PVD Process | Vaporization → Transport → Deposition |
Methods | Thermal Evaporation, Sputtering, Arc Vapor Deposition, Pulsed Laser Deposition |
Advantages | Durability, Versatility, Precision |
Applications | Industrial Coatings, Electronics, Medical Devices |
Key Considerations | Vacuum Environment, Material Compatibility, Process Control |
Discover how PVD can enhance your applications—contact our experts today!