A rotary kiln is a cylindrical, slightly inclined vessel that rotates slowly about its longitudinal axis. It processes materials by tumbling them in a heated drum, ensuring even exposure to heat and facilitating chemical reactions or physical changes. The kiln operates through a combination of gas flow, fuel combustion, heat transfer, and material movement. The material is fed into the upper end and moves downward due to gravity and rotation, while hot gases flow either co-currently or counter-currently to the material. The kiln's temperature and retention time are carefully controlled based on chemical and thermal analyses to achieve the desired reaction or transformation. The rotating drum is sealed at both ends to maintain the internal atmosphere and temperature, ensuring efficient and controlled processing.
Key Points Explained:
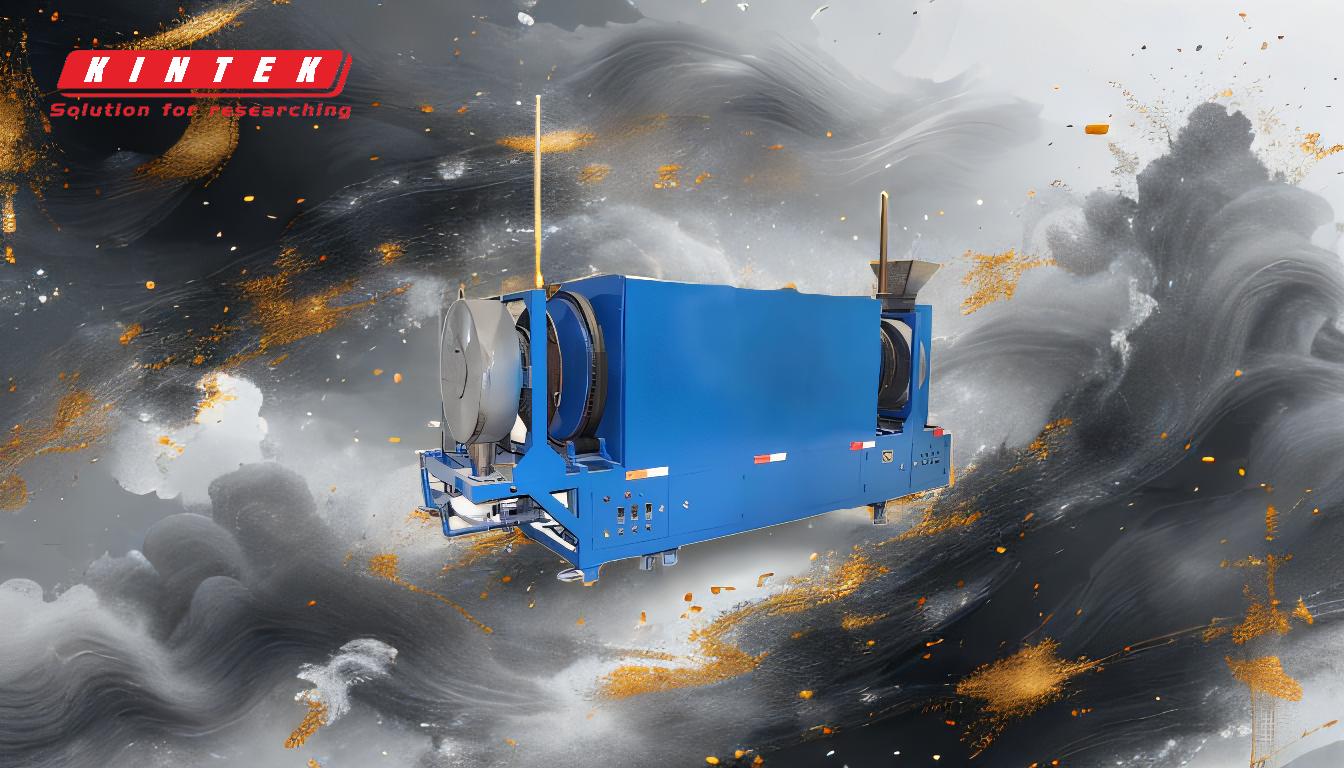
-
Cylindrical Design and Rotation:
- The rotary kiln is a large, hollow cylindrical drum that is slightly inclined from the horizontal.
- It rotates slowly about its longitudinal axis, which helps in tumbling the materials inside, ensuring even exposure to heat and facilitating mixing.
-
Material Movement:
- The material is fed into the upper end of the kiln.
- Due to the rotation and the slight incline, gravity assists in moving the material downward through the kiln toward the lower end.
-
Heating Mechanism:
- The kiln is heated either internally (direct heating) or externally (indirect heating) to achieve the desired temperature.
- Hot gases pass along the kiln, either in the same direction as the material flow (co-current) or in the opposite direction (counter-current).
-
Temperature and Retention Time:
- The temperature and the amount of time the material is held at that temperature (retention time) are predetermined based on chemical and thermal analyses.
- This ensures that the material undergoes the necessary physical and chemical changes to form the desired product.
-
Gas Flow and Combustion:
- The kiln ensures that the fuel burns fully, generating the required heat.
- The heat from the combustion is effectively transferred to the material, facilitating the intended reactions.
-
Sealing and Atmosphere Control:
- The rotating drum is sealed to stationary breeching at each end to control the atmosphere and temperature inside the kiln.
- This sealing is crucial for maintaining the internal conditions necessary for the reaction to proceed effectively.
-
Physical and Chemical Changes:
- As the material moves through the kiln, it undergoes a series of physical and chemical changes.
- These changes are driven by the high temperatures and the controlled environment within the kiln.
-
Internal Configuration Adjustments:
- The internal configuration of the kiln can be adjusted to increase tumbling or expose materials to more heat before they exit.
- This flexibility allows for optimization of the process based on the specific requirements of the material being processed.
By understanding these key points, one can appreciate the complex yet efficient operation of a rotary kiln, which is essential for various industrial processes requiring precise thermal treatment of materials.
Summary Table:
Key Aspect | Description |
---|---|
Cylindrical Design | A slightly inclined, rotating drum for even heat exposure and material mixing. |
Material Movement | Gravity and rotation move materials downward for controlled processing. |
Heating Mechanism | Direct or indirect heating with co-current or counter-current gas flow. |
Temperature Control | Precise control of temperature and retention time for desired reactions. |
Gas Flow & Combustion | Efficient fuel combustion and heat transfer for material transformation. |
Sealing & Atmosphere | Sealed ends maintain internal conditions for effective reactions. |
Physical/Chemical Changes | Materials undergo transformations due to high temperatures and controlled heat. |
Internal Adjustments | Configurable to optimize tumbling and heat exposure for specific materials. |
Interested in optimizing your industrial processes with a rotary kiln? Contact our experts today for tailored solutions!