Vacuum heat treatment is a specialized process used to harden metals in a controlled environment where air is removed from a sealed chamber using a vacuum pump. This method ensures that the metal is not exposed to oxidation, decarburization, or contamination, leading to superior mechanical properties and high-quality components. The process involves precise control over heating and cooling parameters, uniform temperature distribution, and minimal distortion of complex geometries. Vacuum heat treatment includes various techniques such as vacuum sintering, vacuum brazing, vacuum quenching, and vacuum annealing, each tailored to specific applications and material requirements. The advantages of this method include improved surface hardness, wear resistance, and consistent, repeatable results, making it a preferred choice for industries requiring high precision and quality.
Key Points Explained:
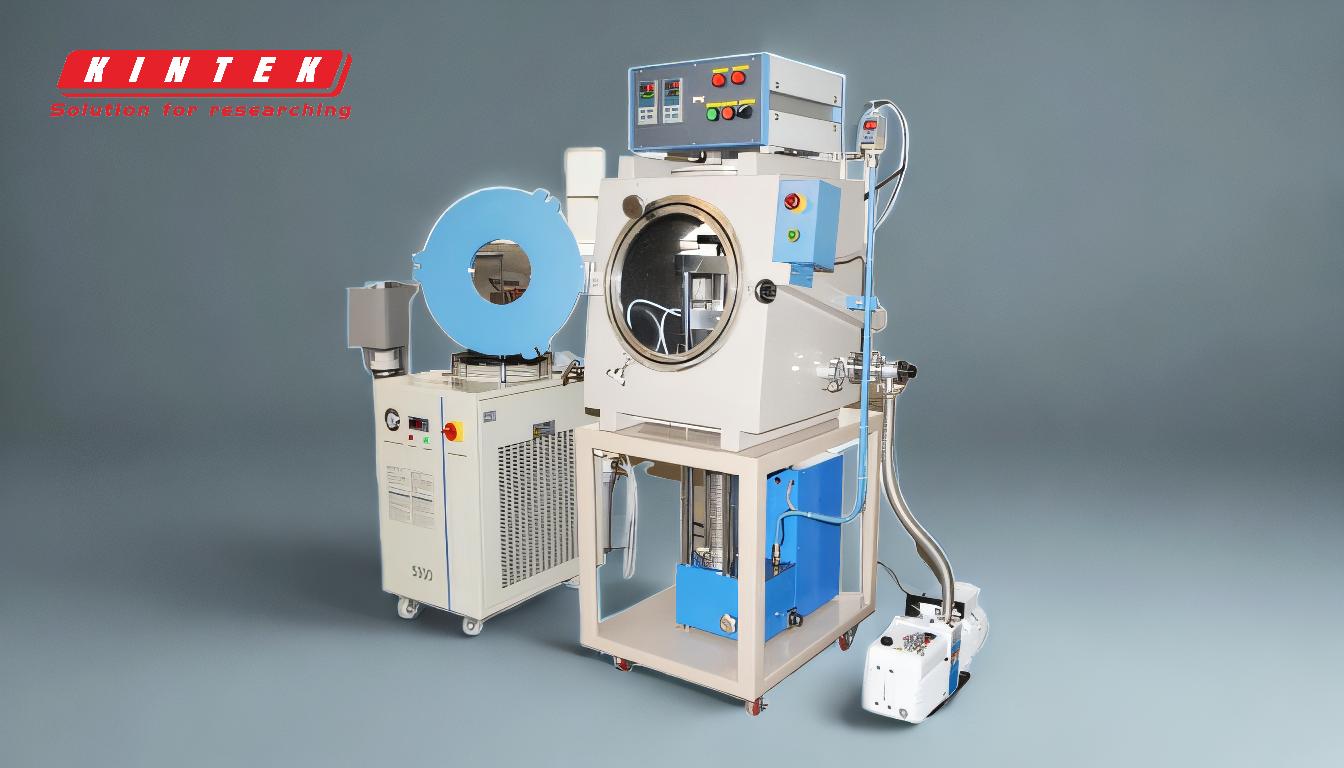
-
Principle of Vacuum Heat Treatment:
- Vacuum heat treatment involves heating metals in a sealed chamber where air is removed using a vacuum pump. This creates an environment free from oxygen and other reactive gases, preventing oxidation, decarburization, and contamination.
- The absence of air ensures that the metal surface remains clean and free from impurities, leading to enhanced mechanical properties and improved surface finish.
-
Types of Vacuum Heat Treatment:
- Vacuum Sintering: A process where powdered metals are heated below their melting points to form a solid mass. This is commonly used in the production of high-density components.
- Vacuum Brazing: Joins two or more metals by heating them just below their melting points and using a filler metal to create a smooth joint. This method is ideal for creating strong, leak-proof joints in complex assemblies.
- Vacuum Quenching: Involves rapid cooling of heated metal to achieve high hardness and strength. The vacuum environment prevents surface oxidation, ensuring a clean and uniform surface.
- Vacuum Annealing: A process used to soften metals, improve ductility, and relieve internal stresses. The vacuum environment prevents surface contamination, ensuring a high-quality finish.
- Vacuum Tempering: Follows quenching to reduce brittleness and improve toughness. The vacuum environment ensures consistent results and prevents surface degradation.
-
Advantages of Vacuum Heat Treatment:
- Enhanced Control: Precise control over heating and cooling parameters ensures uniform temperature distribution and minimal distortion.
- Improved Surface Properties: The absence of oxidation and contamination leads to improved surface hardness, wear resistance, and overall mechanical properties.
- Consistent Results: The controlled environment ensures consistent and repeatable results, making it ideal for high-precision applications.
- Energy Efficiency: Vacuum heat treatment is energy-efficient and environmentally friendly, as it eliminates the need for protective atmospheres or chemical treatments.
-
Applications of Vacuum Heat Treatment:
- Aerospace: Used for treating critical components such as turbine blades, engine parts, and structural components that require high strength and resistance to wear.
- Medical Devices: Ensures the production of high-quality surgical instruments, implants, and other medical components with superior mechanical properties.
- Automotive: Applied in the production of gears, shafts, and other components that require high precision and durability.
- Tool and Die Manufacturing: Enhances the performance and lifespan of cutting tools, molds, and dies by improving hardness and wear resistance.
-
Process Steps in Vacuum Heat Treatment:
- Loading: The metal components are placed inside the vacuum chamber.
- Evacuation: Air is removed from the chamber using a vacuum pump to create a controlled environment.
- Heating: The components are heated to the desired temperature, ensuring uniform heat distribution.
- Holding: The temperature is maintained for a specific period to achieve the desired metallurgical changes.
- Cooling: The components are rapidly or slowly cooled, depending on the desired properties.
- Unloading: The treated components are removed from the chamber and inspected for quality.
-
Comparison with Other Heat Treatment Methods:
- Induction Heat Treatment: Unlike vacuum heat treatment, induction heat treatment uses electromagnetic induction to heat the surface of the metal. While it is faster and more localized, it does not offer the same level of control and uniformity as vacuum heat treatment.
- Atmospheric Heat Treatment: Heat treatment in an open atmosphere can lead to oxidation and contamination, resulting in inferior surface quality and mechanical properties compared to vacuum heat treatment.
In conclusion, vacuum heat treatment is a highly effective method for enhancing the mechanical properties of metals by providing a clean, controlled environment. Its ability to prevent oxidation, decarburization, and contamination, combined with precise control over heating and cooling, makes it an essential process in industries requiring high precision and quality.
Summary Table:
Aspect | Details |
---|---|
Principle | Heating metals in a vacuum-sealed chamber to prevent oxidation and contamination. |
Key Benefits | Improved surface hardness, wear resistance, and consistent results. |
Common Techniques | Vacuum sintering, brazing, quenching, annealing, and tempering. |
Applications | Aerospace, medical devices, automotive, and tool manufacturing. |
Process Steps | Loading, evacuation, heating, holding, cooling, and unloading. |
Discover how vacuum heat treatment can elevate your metal components—contact our experts today!