The process of a crucible furnace involves heating materials, typically metals with low melting points like brass, bronze, or aluminum, inside a crucible until they reach their melting point. The furnace uses a heating element powered by fuel sources such as natural gas, propane, or electricity to generate heat. This heat is transferred to the crucible, which is made of refractory material, causing the material inside to melt. Once molten, the material is poured into molds or containers to achieve the desired shape. The process can be controlled through temperature adjustments, and factors like furnace size and design influence melting efficiency and time.
Key Points Explained:
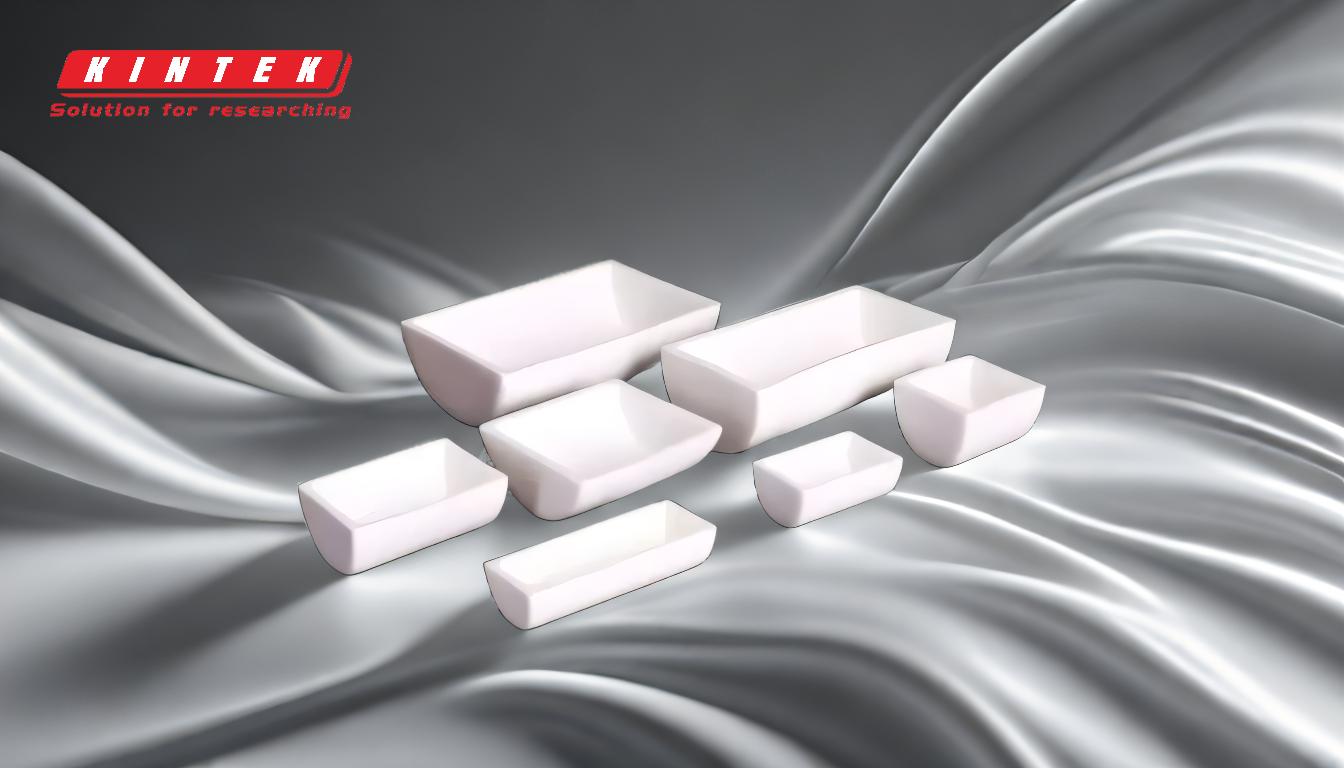
-
Purpose of a Crucible Furnace
- A crucible furnace is primarily used for melting and casting metals with low melting points, such as brass, bronze, and aluminum.
- It is one of the oldest types of melting ovens and remains widely used in industries for its simplicity and effectiveness.
-
Components of a Crucible Furnace
- Crucible: A container made of refractory material (e.g., graphite, clay, or ceramic) that holds the material to be melted.
- Furnace Chamber: Encloses the crucible and is also made of refractory material to withstand high temperatures.
- Heating Element: Generates heat using fuel sources like natural gas, propane, or electricity.
- Temperature Control System: Allows precise regulation of heat to ensure optimal melting conditions.
-
Heating Process
- The heating element generates heat, which is transferred to the crucible.
- The crucible, in turn, heats the material inside until it reaches its melting point.
- The furnace chamber insulates the heat, ensuring efficient energy use and uniform heating.
-
Melting and Pouring
- Once the material reaches its melting point, it becomes molten.
- The molten material is then poured into molds or containers to take the desired shape.
- This step requires careful handling to avoid spills or contamination.
-
Control and Optimization
- The melting process can be controlled by adjusting the heat input or using a temperature control system.
- Factors like furnace size, design, and crucible material impact the melting time and efficiency.
- Proper control ensures consistent results and minimizes energy waste.
-
Applications and Advantages
- Crucible furnaces are ideal for small-scale melting and casting operations.
- They are versatile, cost-effective, and suitable for a variety of metals.
- Their simplicity makes them easy to operate and maintain.
By understanding these key points, a purchaser can evaluate whether a crucible furnace meets their specific needs, considering factors like material type, production scale, and operational efficiency.
Summary Table:
Key Aspect | Details |
---|---|
Purpose | Melting and casting metals with low melting points (e.g., brass, aluminum). |
Components | Crucible, furnace chamber, heating element, temperature control system. |
Heating Process | Heat is transferred to the crucible, melting the material uniformly. |
Melting and Pouring | Molten material is poured into molds for shaping. |
Control and Optimization | Adjustable heat input and temperature control for consistent results. |
Applications | Small-scale operations, cost-effective, versatile, and easy to maintain. |
Discover how a crucible furnace can streamline your metal melting process—contact us today to learn more!