A vacuum furnace is a specialized piece of equipment used for heat treatment processes in a controlled, oxygen-free environment. The process involves loading materials into the chamber, creating a vacuum to remove oxygen, heating the materials to precise temperatures, and then cooling them using inert gases. This ensures uniform temperature distribution, prevents oxidation, and minimizes contamination. The vacuum furnace is ideal for applications requiring high precision, such as metallurgy, brazing, and sintering. Proper operation requires trained personnel and adherence to strict cleanliness protocols to maintain the integrity of the process and the materials being treated.
Key Points Explained:
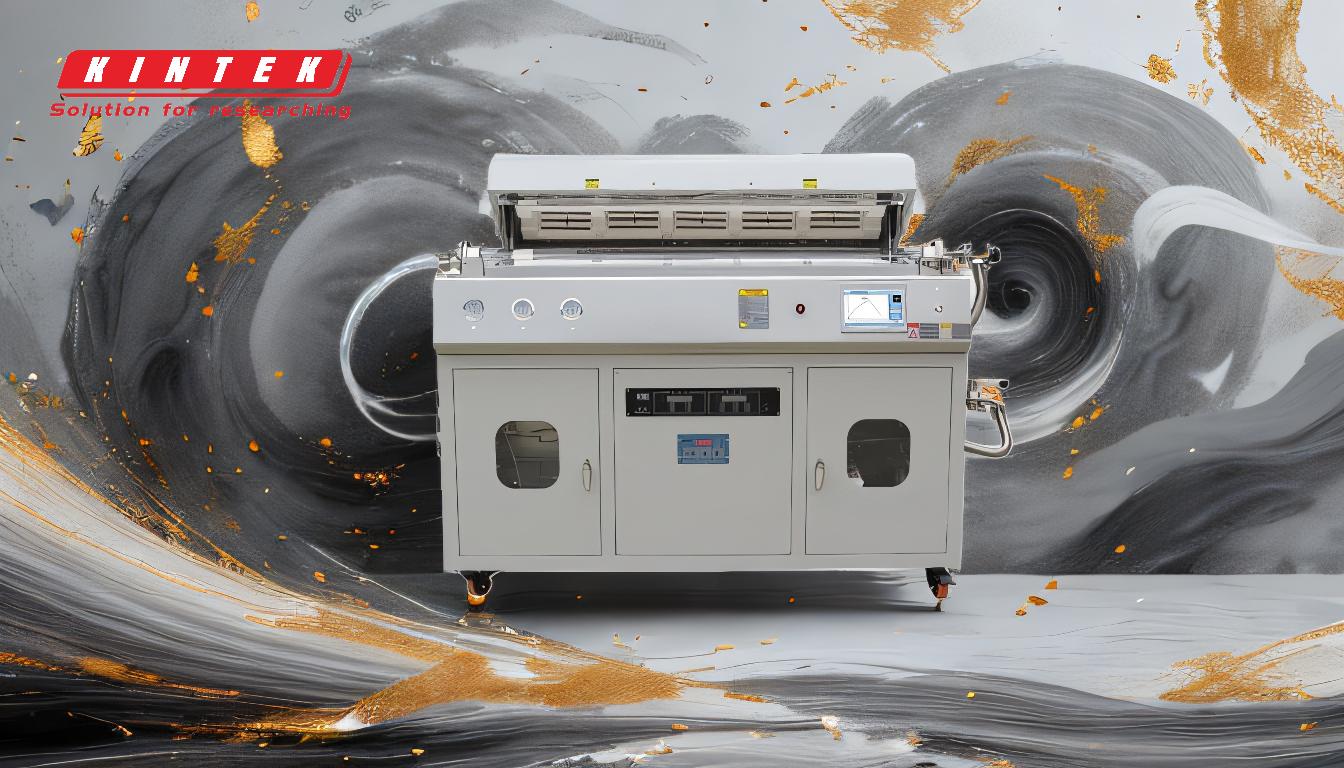
-
Introduction to a Vacuum Furnace
- A vacuum furnace is a type of equipment designed to heat materials in a vacuum environment, where the pressure is reduced to less than one standard atmospheric pressure. This prevents oxidation and contamination, making it ideal for processes like brazing, sintering, and heat treatment.
- The vacuum environment is created using a vacuum system, typically operating in the 10-2 Torr range, which includes components like a two-stage rotary vane pump, vacuum gauge controller, and electro-pneumatic vacuum valve.
-
Key Steps in the Vacuum Furnace Process
- Loading the Furnace: Materials, tools, or components are carefully placed into the furnace chamber. Operators must wear clean garments and gloves to avoid contamination, as even fingerprints can cause rust stains.
- Creating a Vacuum: The vacuum system removes oxygen and other gases from the chamber, ensuring an oxygen-free environment. This step is critical to prevent oxidation and achieve the desired metallurgical properties.
- Heating the Materials: The furnace heats the materials to a precise temperature, typically between 1100°C and 1500°C. The temperature is controlled using advanced systems to ensure uniformity and repeatability.
- Cooling and Finishing: After heating, inert gases like argon are introduced to cool the materials rapidly (quenching) without causing chemical reactions. This step ensures the materials achieve the desired hardness and structural properties.
-
Advantages of Using a Vacuum Furnace
- Controlled Environment: The vacuum prevents oxidation and contamination, ensuring high-quality results.
- Uniform Temperature Distribution: The furnace provides consistent heating across the chamber, which is essential for processes like brazing and sintering.
- Rapid Cooling: Inert gas quenching allows for fast cooling, which is critical for achieving specific material properties.
- Computer-Controlled Processes: Automation ensures repeatability and precision, making the vacuum furnace suitable for high-precision applications.
-
Operational Requirements and Safety
- Cleanliness: The furnace chamber must be kept clean, and operators must follow strict protocols to avoid contamination. Materials should be packed in plastic envelopes and sealed with nitrogen to prevent oxidation.
- Trained Personnel: Only trained and experienced operators should handle the vacuum furnace to ensure safety and proper operation.
- Prohibited Actions: Direct injection of liquids or molten metals into the chamber is strictly prohibited to avoid damage to the furnace and ensure safety.
-
Applications of Vacuum Furnaces
- Vacuum furnaces are widely used in industries such as aerospace, automotive, and medical device manufacturing. They are ideal for processes that require high precision, such as heat treatment of metals, brazing of complex components, and sintering of advanced materials.
By following these steps and adhering to operational guidelines, a vacuum furnace can deliver consistent, high-quality results for a wide range of industrial applications.
Summary Table:
Step | Description |
---|---|
Loading | Materials are carefully placed into the chamber to avoid contamination. |
Creating a Vacuum | Oxygen and gases are removed to prevent oxidation and ensure a clean environment. |
Heating | Materials are heated to precise temperatures (1100°C–1500°C) for uniformity. |
Cooling | Inert gases like argon quench materials rapidly to achieve desired properties. |
Finishing | Materials are cooled and ready for high-precision applications. |
Ready to optimize your heat treatment process? Contact our experts today for tailored vacuum furnace solutions!