The process of annealing tubes involves heating the metal to a specific temperature where its crystalline structure becomes more fluid, allowing defects to repair themselves. This is followed by holding the metal at that temperature for a set period and then cooling it at a controlled rate to achieve a more ductile and workable structure. The annealing process is divided into three stages: Recovery, Recrystallization, and Grain growth, which occur as the temperature increases. This process is commonly carried out using a chamber furnace, where precise temperature control and cooling rates are essential for achieving the desired material properties.
Key Points Explained:
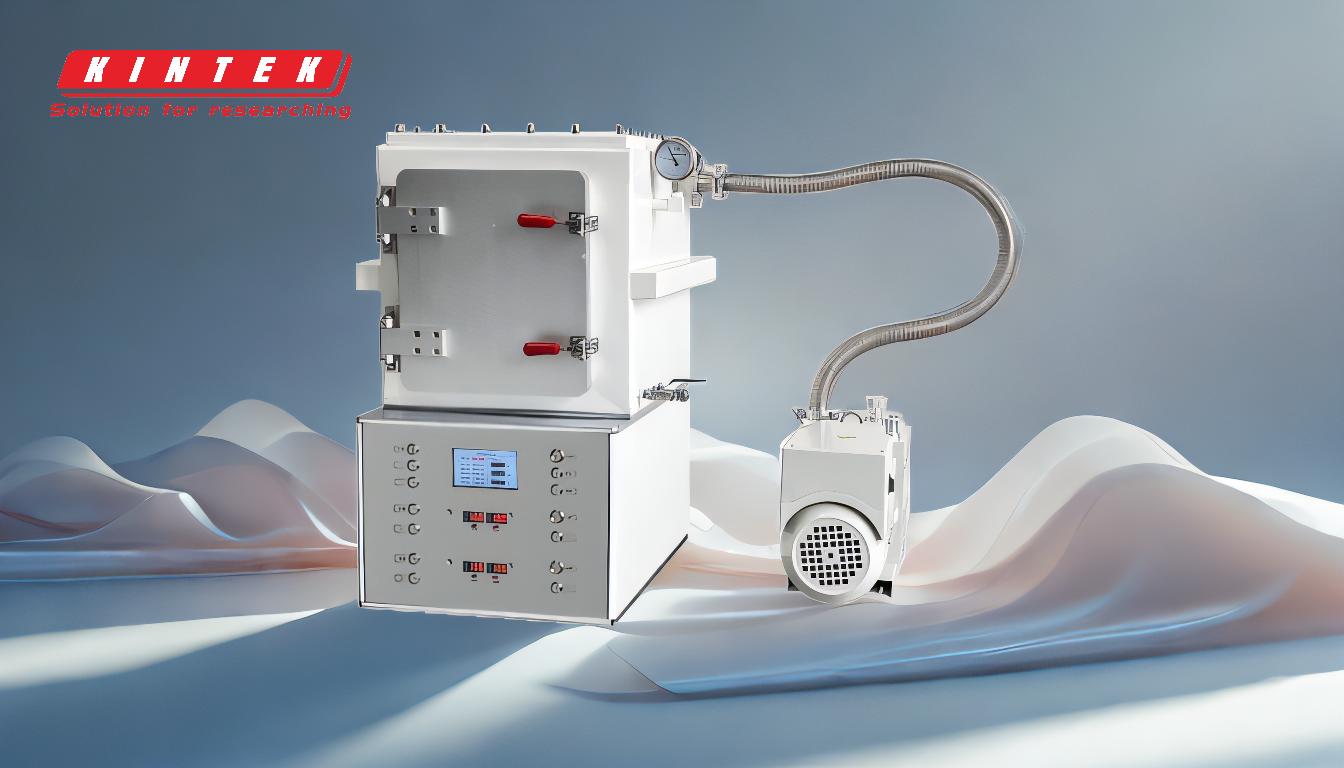
-
Three Stages of Annealing:
- Recovery: This is the initial stage where the metal is heated to a temperature that relieves internal stresses without altering the grain structure. The metal begins to soften, and dislocations in the crystal structure start to move and rearrange.
- Recrystallization: At this stage, the metal is heated to a higher temperature where new, strain-free grains begin to form, replacing the deformed grains. This results in a reduction of hardness and an increase in ductility.
- Grain Growth: If the metal is held at the recrystallization temperature for too long, the grains will continue to grow, which can lead to a decrease in strength. Controlling the time and temperature is crucial to prevent excessive grain growth.
-
Heating the Metal:
- The metal is heated to a specific temperature where the crystalline structure becomes fluid but remains in a solid state. This temperature is typically below the melting point of the metal but high enough to allow for the movement of atoms within the crystal lattice.
- The exact temperature depends on the type of metal being annealed. For example, steel is typically annealed at temperatures between 700°C and 900°C, while copper is annealed at lower temperatures, around 400°C to 700°C.
-
Holding Time:
- After reaching the desired temperature, the metal is held at that temperature for a specific period, known as the holding time. This allows for the complete recrystallization of the metal and the repair of any defects in the crystal structure.
- The holding time varies depending on the type of metal, its thickness, and the desired properties. For instance, thicker materials may require longer holding times to ensure uniform heating throughout the material.
-
Controlled Cooling:
- After the holding period, the metal is cooled at a controlled rate. Slow cooling is essential to prevent the formation of new stresses and to allow the metal to achieve a more ductile and uniform structure.
- The cooling rate can vary depending on the material and the desired outcome. For some materials, cooling in the furnace (furnace cooling) is preferred, while for others, cooling in air or a controlled environment may be necessary.
-
Use of Chamber Furnace:
- A chamber furnace is commonly used for the annealing process due to its ability to provide precise temperature control and uniform heating. The furnace allows for the metal to be heated evenly, ensuring consistent results throughout the material.
- The furnace also provides a controlled environment for cooling, which is crucial for achieving the desired material properties.
By following these steps, the annealing process can effectively improve the ductility, reduce hardness, and relieve internal stresses in metal tubes, making them more suitable for further processing or use in various applications.
Summary Table:
Stage | Description |
---|---|
Recovery | Relieves internal stresses; dislocations in the crystal structure rearrange. |
Recrystallization | New, strain-free grains form, reducing hardness and increasing ductility. |
Grain Growth | Excessive grain growth can occur if temperature and time are not controlled. |
Heating | Metal heated to a specific temperature below melting point for fluidity. |
Holding Time | Metal held at temperature to allow recrystallization and defect repair. |
Cooling | Controlled cooling prevents new stresses and ensures a ductile structure. |
Chamber Furnace | Provides precise temperature control and uniform heating for consistent results. |
Optimize your metal processing with precise annealing techniques—contact us today for expert guidance!