Continuous sintering is a process used in manufacturing to produce high-strength, thermally resistant components from powdered materials. It involves heating compacted powders to temperatures just below their melting point in a controlled environment, allowing the particles to bond without liquefying. This process is typically carried out in a sintering furnace, where materials are continuously fed through the furnace, ensuring uniform heating and cooling. The process is widely used in industries such as metallurgy, ceramics, and dentistry, where precise control over material properties is essential.
Key Points Explained:
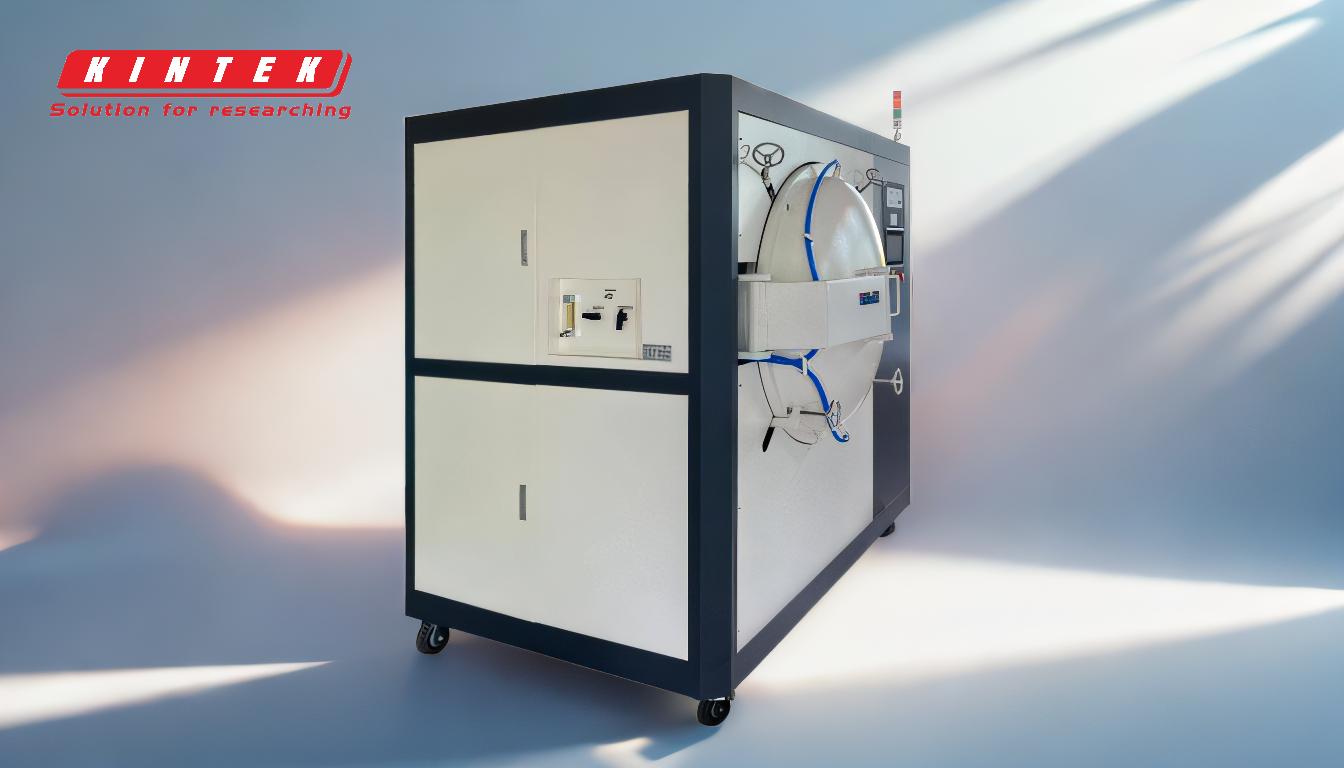
-
Definition and Purpose of Continuous Sintering:
- Continuous sintering is a method used to transform powdered materials into solid, durable components by heating them below their melting point. This process is crucial for creating materials with high thermal resistance and mechanical strength, such as dental zirconia crowns or metal parts in industrial applications.
-
Role of the Sintering Furnace:
- The sintering furnace is the core equipment in this process. It maintains precise temperatures and controlled atmospheres to ensure the powdered materials bond effectively. In continuous sintering, the furnace is designed to allow materials to move through it in a continuous flow, ensuring consistent heating and cooling.
-
Stages of the Continuous Sintering Process:
- Blending and Compaction: The powdered materials are mixed with additives and compacted into the desired shape. This step ensures uniformity in the final product.
- Heating and Bonding: The compacted material is heated in the sintering furnace to a temperature just below its melting point. This allows the particles to bond without melting, creating a solid structure.
- Cooling and Solidification: After heating, the material is cooled gradually to solidify into a unified mass. This step is critical for achieving the desired mechanical properties.
-
Applications of Continuous Sintering:
- Dental Industry: Used to sinter dental zirconia into crowns, bridges, and other restorations.
- Metallurgy: Produces high-strength metal components for industrial use.
- Ceramics: Creates durable ceramic parts for various applications.
-
Advantages of Continuous Sintering:
- Efficiency: The continuous flow of materials through the furnace allows for high-volume production.
- Consistency: Uniform heating and cooling ensure consistent material properties.
- Versatility: Suitable for a wide range of materials, including metals, ceramics, and composites.
-
Challenges and Considerations:
- Temperature Control: Maintaining precise temperatures is critical to avoid defects in the final product.
- Material Shrinkage: The sintering process often results in slight shrinkage, which must be accounted for in the design phase.
- Atmosphere Control: The furnace must maintain a controlled atmosphere to prevent oxidation or contamination.
By understanding these key points, purchasers of equipment and consumables can make informed decisions about the sintering process and the necessary tools, such as a sintering furnace, to achieve optimal results.
Summary Table:
Aspect | Details |
---|---|
Definition | Heating compacted powders below melting point to bond particles. |
Key Equipment | Sintering furnace for precise temperature and atmosphere control. |
Stages | Blending & Compaction → Heating & Bonding → Cooling & Solidification. |
Applications | Dental zirconia, industrial metal parts, ceramic components. |
Advantages | High efficiency, consistent properties, versatile material compatibility. |
Challenges | Temperature control, material shrinkage, atmosphere management. |
Ready to optimize your sintering process? Contact our experts today for tailored solutions!