Debinding is a critical step in the manufacturing of technical ceramics and 3D-printed parts, involving the removal of organic binders or carrier materials from the green body. This process ensures that the final product is free from contaminants that could affect its structural integrity during sintering. Debinding can be achieved through thermal or chemical methods, often requiring precise control of temperature, gas atmosphere, and time. The process typically starts with a nitrogen purge to reduce oxygen levels, followed by heating cycles that gradually decompose the binders. Multiple passes through the furnace may be necessary to ensure complete binder removal, as even trace amounts can compromise the sintering phase. The duration of debinding depends on factors like part geometry and binder composition, often taking up to 24-36 hours.
Key Points Explained:
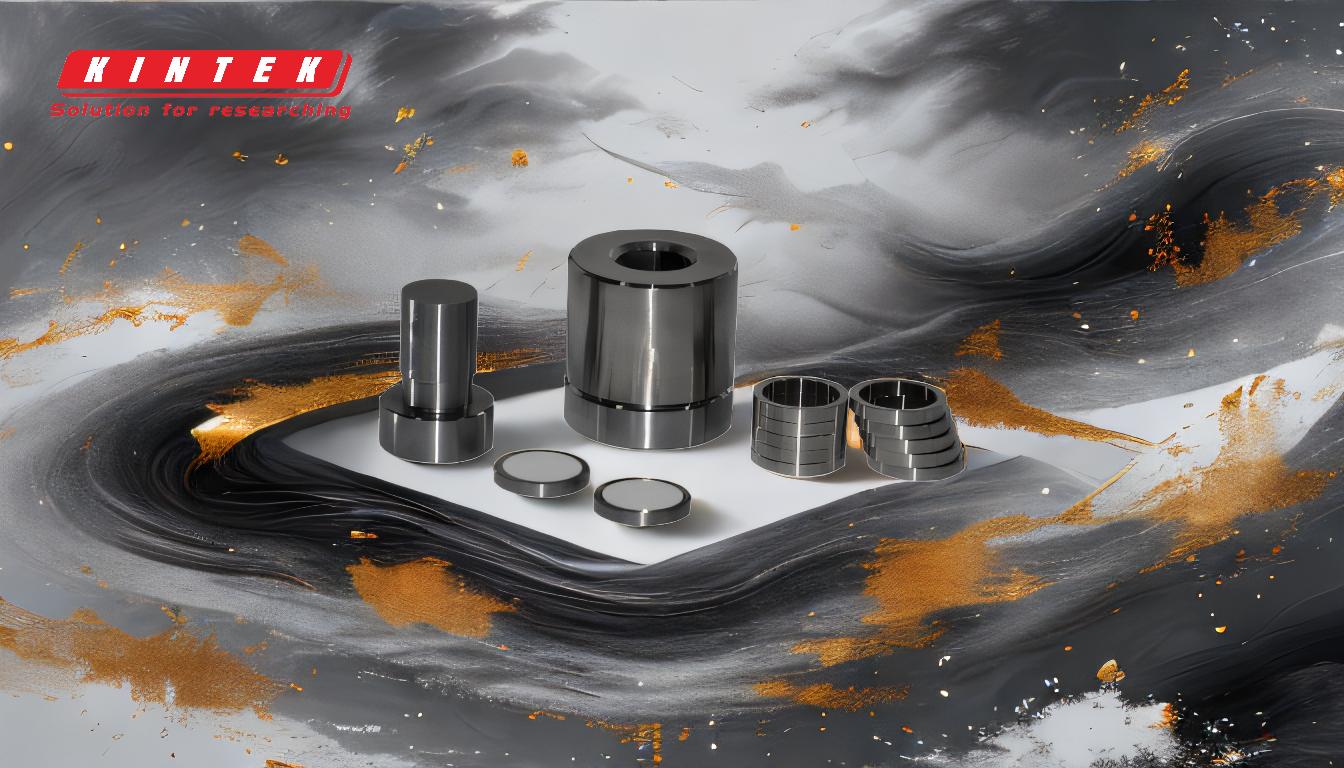
-
Purpose of Debinding:
- Debinding removes organic binders or carrier materials from 3D-printed parts or green bodies in technical ceramics.
- Ensures the final product is free from contaminants that could interfere with sintering, a process that densifies the material.
-
Methods of Debinding:
- Thermal Debinding: Involves heating the part in a furnace to decompose the binders. Temperatures typically range from 150°C to 600°C (300°F to 1110°F).
- Chemical Debinding: Uses solvents to dissolve the binders, often in combination with thermal methods for more complex parts.
-
Process Steps:
- Nitrogen Purge: Begins with reducing oxygen content in the furnace to prevent oxidation and ensure a controlled environment.
-
Heating Cycles: Parts are heated gradually, often in multiple stages, to decompose the binders. For example:
- Heat to 225°C at 2°C/min.
- Increase to 550°C at 1°C/min and hold for 2 hours.
- Further heating to 1,300°C at 6°C/min, with holding times ranging from 40 to 180 minutes.
- Cooling: Parts are cooled to 600°C at 6°C/min and then allowed to cool further in the furnace.
-
Factors Influencing Debinding:
- Part Geometry: Complex shapes may require longer debinding times to ensure complete binder removal.
- Binder Composition: Different binders decompose at varying temperatures, necessitating tailored heating profiles.
- Furnace Atmosphere: Controlled gas environments (e.g., nitrogen) are crucial to prevent defects like warping or cracking.
-
Challenges and Considerations:
- Trace Binder Residue: Even small amounts of remaining binder can contaminate the sintering phase, making multiple furnace passes necessary.
- Defect Prevention: Careful control of temperature, pressure, and gas atmosphere is essential to avoid warping, cracking, or other defects.
- Time Intensity: Debinding can take up to 24-36 hours, depending on the part and binder type.
-
Integration with Sintering:
- Debinding is often part of a larger process that includes sintering, where the part is heated to high temperatures to achieve densification.
- The debinding and sintering processes are closely linked, requiring seamless transitions between temperature cycles to ensure part integrity.
By understanding these key points, equipment and consumable purchasers can better evaluate the requirements for debinding processes, ensuring they select the appropriate materials and equipment for their specific applications.
Summary Table:
Aspect | Details |
---|---|
Purpose | Removes organic binders to prevent sintering contamination. |
Methods | Thermal (150°C–600°C) or chemical debinding. |
Process Steps | Nitrogen purge, heating cycles, cooling. |
Key Factors | Part geometry, binder composition, furnace atmosphere. |
Challenges | Trace residue, defect prevention, time-intensive (24-36 hours). |
Integration | Closely linked with sintering for densification. |
Optimize your debinding process for flawless sintering—contact our experts today!