Furnace soldering is a specialized process used to join metal components by melting a filler material (solder) without melting the base metals. It is commonly used in industries requiring high precision and strong joints, such as aerospace, electronics, and automotive manufacturing. The process involves several critical steps, including joint preparation, cleaning, assembly, heating, and post-processing. Each step ensures the integrity and strength of the final joint. Below, we break down the process in detail to provide a comprehensive understanding of furnace soldering.
Key Points Explained:
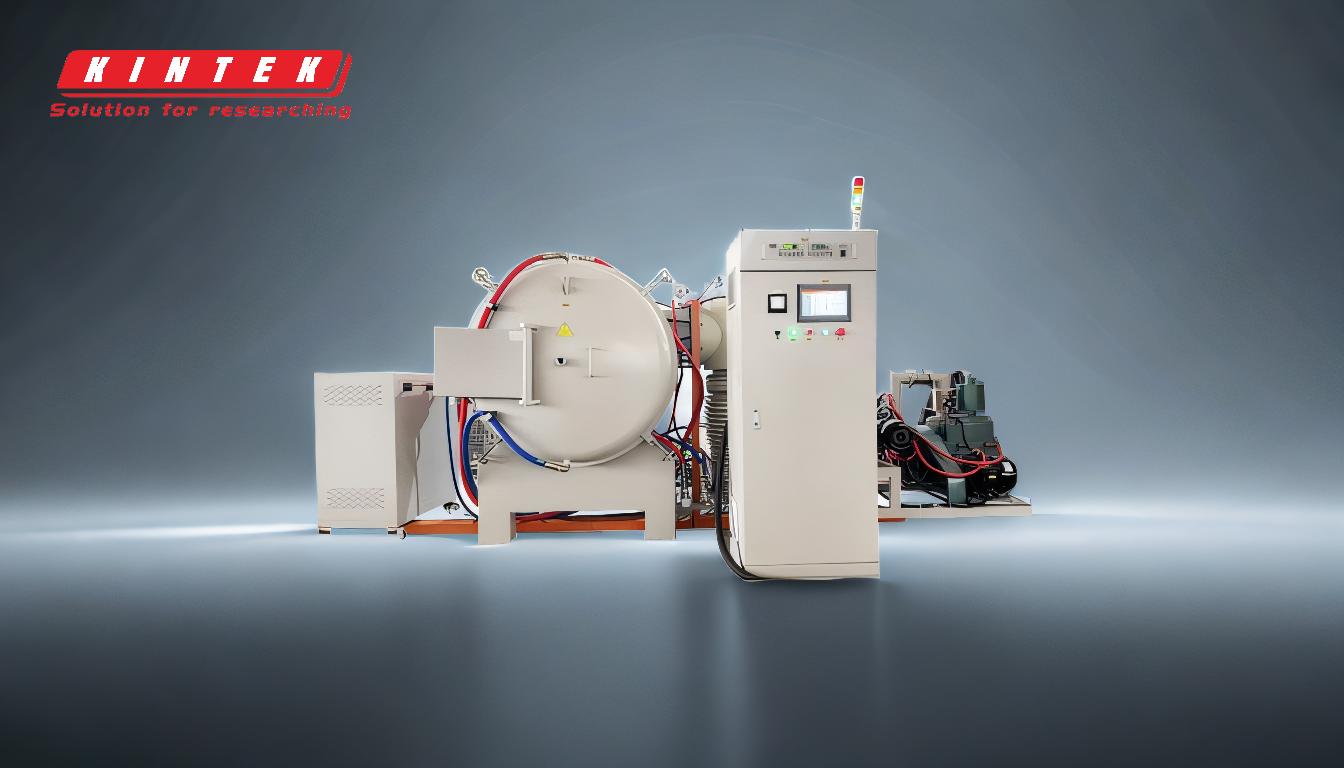
-
Joint Fit and Preparation
- The first step in furnace soldering is ensuring the joint fit is correct. This involves checking the gap width between the metal components to ensure it is neither too wide nor too narrow.
- A proper gap allows the solder to flow evenly and form a strong bond. Too wide a gap may result in weak joints, while too narrow a gap can prevent proper solder flow.
- This step is critical for achieving uniform heating and solder distribution during the process.
-
Cleaning the Metal Surfaces
- Contaminants such as oils, oxides, or dirt can interfere with the soldering process, leading to weak or incomplete joints.
- Cleaning is typically done using chemical solvents, abrasives, or ultrasonic cleaning methods to ensure the surfaces are free of impurities.
- Clean surfaces allow the solder to adhere properly and form a strong metallurgical bond.
-
Assembly and Alignment
- After cleaning, the parts are assembled with precise alignment. This is often achieved using clamps, fixtures, or support structures to hold the components in place.
- Proper alignment ensures that the solder flows evenly and fills the joint completely, preventing gaps or voids.
- Misalignment can lead to uneven heating and weak joints, compromising the integrity of the final product.
-
Heating in the Furnace
- The assembled parts are placed in a furnace, where they are heated to a temperature that melts the solder but not the base metals.
- The furnace provides a controlled environment, ensuring uniform heating and preventing oxidation or contamination.
- The solder flows into the joint by capillary action, forming a strong bond as it cools and solidifies.
- Temperature control is critical, as overheating can damage the components, while insufficient heat may result in incomplete soldering.
-
Post-Processing and Cleaning
- Once the soldering is complete, the assembly is removed from the furnace and allowed to cool.
- Any residual flux or solder spatter is cleaned off using appropriate methods, such as chemical cleaning or mechanical abrasion.
- This step ensures the final product is free of contaminants and meets the required specifications for appearance and performance.
By following these steps meticulously, furnace soldering produces strong, reliable joints suitable for high-performance applications. The process requires careful attention to detail at every stage to ensure the quality and durability of the final product.
Summary Table:
Step | Description |
---|---|
Joint Fit & Preparation | Ensure proper gap width for even solder flow and strong bonding. |
Cleaning | Remove contaminants using solvents, abrasives, or ultrasonic methods for clean surfaces. |
Assembly & Alignment | Align parts precisely using clamps or fixtures to ensure even solder flow and prevent voids. |
Heating in the Furnace | Heat in a controlled furnace to melt solder without damaging base metals. |
Post-Processing | Clean residual flux or solder spatter to meet performance and appearance standards. |
Need expert guidance on furnace soldering? Contact us today to achieve flawless metal joints for your applications!