Hot press forging is a manufacturing process that involves shaping metal using heat and pressure. The process typically uses a hot press machine to apply controlled heat and force to a workpiece, ensuring uniform deformation and high-quality results. The process begins by heating the metal to a temperature where it becomes malleable, followed by applying pressure to shape it into the desired form. The key steps include heating, pressing, and cooling, each of which is critical to achieving the desired mechanical properties and dimensional accuracy. Below, we will explore the process in detail, focusing on the role of the hot press machine and its operational advantages.
Key Points Explained:
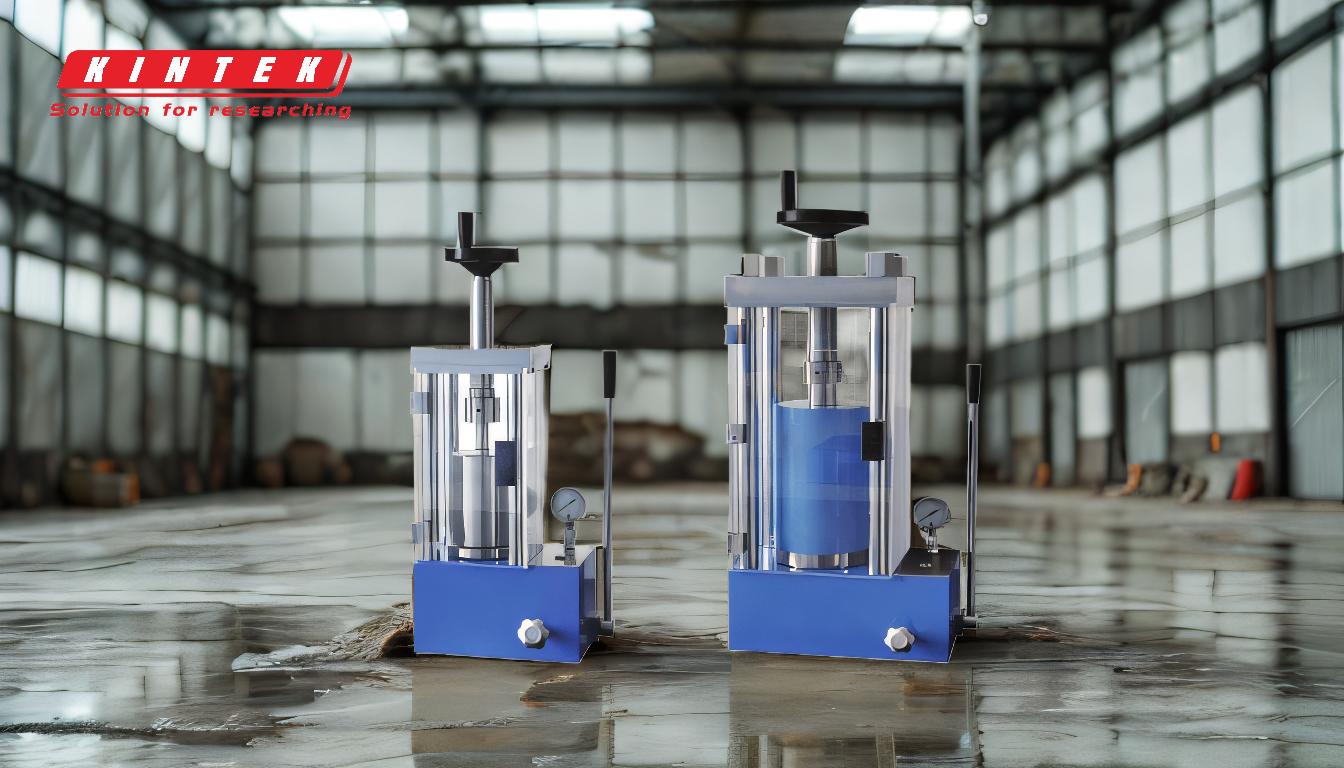
-
Heating the Workpiece
- The first step in hot press forging is heating the metal to its recrystallization temperature, typically between 700°C and 1,200°C, depending on the material.
- The hot press machine plays a crucial role here, as it ensures fast and uniform heating. For thin workpieces (under twenty millimeters thick), the heat conduction time is minimal, allowing for rapid processing.
- Uniform heating is essential to prevent internal stresses and ensure consistent material properties throughout the workpiece.
-
Applying Pressure with the Hot Press Machine
- Once the metal reaches the desired temperature, it is placed in the hot press machine, where pressure is applied to shape it.
- The machine uses a ram or plunger to deliver controlled force, ensuring precise deformation. In some designs, such as friction drive forging presses, vertically mounted drive wheels and flywheels are used to accelerate the ram during the downstroke.
- The ability to control the pressure and speed of the ram is critical for achieving the desired shape and avoiding defects like cracks or uneven surfaces.
-
Uniform Heating and Adhesive Curing
- One of the standout features of a hot press machine is its ability to minimize the influence of workpiece thickness on heating. This ensures that both the interior and exterior of the product are heated uniformly.
- Uniform heating is particularly important for processes like adhesive curing, where consistent temperatures are required to achieve strong bonds.
- The machine's design also helps maintain temperature stability during the pressing phase, further enhancing the quality of the final product.
-
Cooling and Finishing
- After the pressing phase, the workpiece is allowed to cool gradually. Controlled cooling is essential to prevent warping or cracking due to thermal stresses.
- Depending on the application, additional finishing processes, such as machining or surface treatment, may be required to achieve the final specifications.
-
Advantages of Hot Press Forging
- Enhanced Material Properties: The combination of heat and pressure improves the grain structure of the metal, resulting in higher strength and durability.
- Precision and Consistency: The hot press machine ensures precise control over temperature and pressure, leading to consistent results.
- Efficiency: Fast heating and uniform temperature distribution reduce processing time, making the process suitable for high-volume production.
-
Applications of Hot Press Forging
- Hot press forging is widely used in industries such as automotive, aerospace, and tool manufacturing, where high-strength components are required.
- Common products include engine components, gears, and structural parts.
In summary, hot press forging is a highly effective process for shaping metal components with superior mechanical properties. The hot press machine plays a central role in ensuring efficient heating, precise pressure application, and uniform temperature distribution, all of which contribute to the quality and consistency of the final product. By understanding the key steps and advantages of this process, manufacturers can optimize their operations and produce high-performance components for a wide range of applications.
Summary Table:
Step | Description |
---|---|
Heating | Heat metal to 700°C–1,200°C for uniform malleability and stress prevention. |
Pressing | Apply controlled pressure using a hot press machine for precise deformation. |
Cooling | Gradually cool the workpiece to prevent warping or cracking. |
Advantages | Enhanced strength, precision, and efficiency for high-volume production. |
Applications | Used in automotive, aerospace, and tool manufacturing for durable components. |
Optimize your metal shaping process with hot press forging—contact our experts today!