Mold manufacturing is a complex and precise process that involves several stages, from design to final production. The process typically begins with the creation of a detailed design, followed by material selection, machining, and finishing. The mold is then tested and refined to ensure it meets the required specifications. The final step involves the actual production of parts using the mold, where a liquid material is injected into the mold cavity, cooled, and hardened to form the desired shape. This process is critical in industries such as automotive, consumer goods, and electronics, where high precision and repeatability are essential.
Key Points Explained:
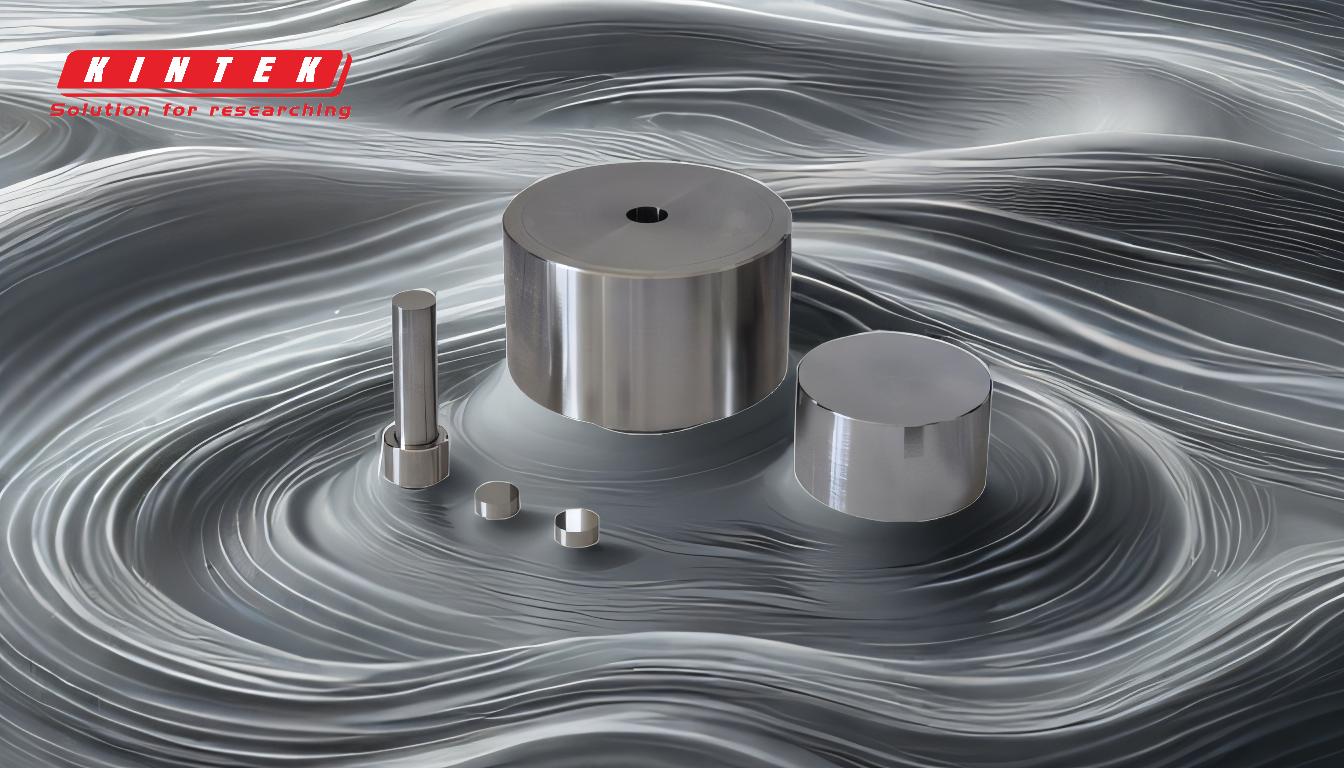
-
Design and Planning:
- Conceptualization: The process starts with the conceptualization of the mold design, often using CAD (Computer-Aided Design) software. This stage involves defining the shape, size, and features of the mold.
- Material Selection: Based on the design requirements, the appropriate material (usually steel or aluminum) is selected. Steel is preferred for its durability and ability to withstand high pressures, while aluminum is chosen for its lighter weight and faster machining times.
- Simulation and Analysis: Before manufacturing, simulations are often run to predict how the mold will perform. This includes flow analysis to ensure the material will fill the mold cavity correctly and cooling analysis to optimize the cooling process.
-
Machining:
- CNC Machining: The selected material is then machined using CNC (Computer Numerical Control) machines. This involves cutting, drilling, and milling the material to form the mold's specific features. CNC machining ensures high precision and repeatability.
- EDM (Electrical Discharge Machining): For more complex shapes or hard-to-reach areas, EDM is used. This process involves using electrical discharges to erode material, allowing for the creation of intricate details.
- Surface Finishing: After machining, the mold undergoes surface finishing processes such as polishing or coating to improve its surface quality and durability. This step is crucial for ensuring the final product has a smooth finish.
-
Assembly and Testing:
- Assembly: Once all the components of the mold are machined and finished, they are assembled. This includes fitting together the core and cavity, as well as any inserts or ejector pins.
- Testing: The assembled mold is then tested to ensure it functions correctly. This involves injecting a material (often a plastic) into the mold cavity and checking the quality of the resulting part. Adjustments may be made to the mold based on the test results.
-
Production:
- Injection Molding: In the production phase, the mold is used in an injection molding machine. A liquid material (usually plastic) is fed into a heated barrel, mixed, and then injected into the mold's cavity under high pressure.
- Cooling and Ejection: The material cools and hardens to the mold's configuration. Once solidified, the part is ejected from the mold, and the process repeats for the next part.
- Quality Control: Throughout the production process, quality control measures are in place to ensure each part meets the required specifications. This may include visual inspections, dimensional checks, and functional testing.
-
Maintenance and Refinement:
- Regular Maintenance: To ensure the mold remains in good condition and continues to produce high-quality parts, regular maintenance is required. This includes cleaning, lubrication, and inspection for wear and tear.
- Refinement: Over time, the mold may need to be refined or modified to accommodate design changes or to improve performance. This could involve re-machining certain areas or updating the mold's components.
In summary, mold manufacturing is a multi-step process that requires careful planning, precision machining, and thorough testing. Each stage, from design to production, plays a critical role in ensuring the final mold meets the required specifications and can produce high-quality parts consistently.
Summary Table:
Stage | Key Activities |
---|---|
Design and Planning | Conceptualization, Material Selection, Simulation and Analysis |
Machining | CNC Machining, EDM, Surface Finishing |
Assembly and Testing | Assembly, Testing, Adjustments |
Production | Injection Molding, Cooling and Ejection, Quality Control |
Maintenance | Regular Maintenance, Refinement |
Need expert guidance on mold manufacturing? Contact us today for tailored solutions!