Physical Vapor Deposition (PVD) is a sophisticated process used to create thin films and coatings on substrates by converting solid materials into a vapor phase and then depositing them onto a target surface. This process is widely used in industries to produce durable, corrosion-resistant, and high-performance coatings. The PVD process involves several key steps: evaporation of the target material, transportation of the vaporized atoms, potential chemical reactions, and deposition onto the substrate. The method is versatile, allowing for the coating of various materials, including those with high melting points, and is carried out in a vacuum or low-pressure environment to ensure precision and quality.
Key Points Explained:
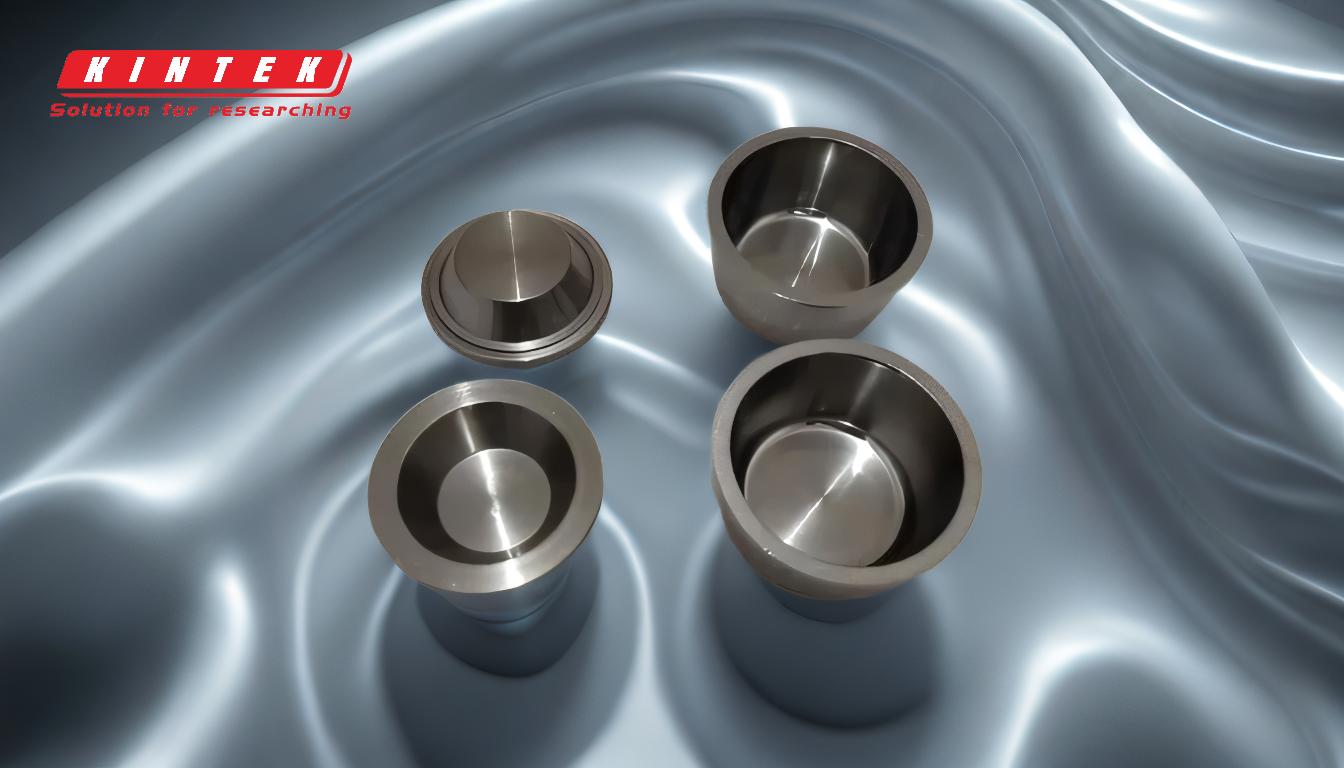
-
Evaporation of the Target Material:
- The PVD process begins with the evaporation of a solid target material. This is achieved using high-energy sources such as electrical energy, lasers, or thermal methods.
- The target material is bombarded, causing its atoms to dislodge and transition from a solid to a vapor phase. This step is crucial as it determines the quality and uniformity of the final coating.
-
Transportation of Vaporized Atoms:
- Once the target material is vaporized, the atoms are transported through a reaction chamber. This chamber is typically maintained at low pressure to minimize interference from background gases.
- The transportation phase ensures that the vaporized atoms move efficiently towards the substrate, maintaining the integrity of the coating process.
-
Chemical Reactions (Optional):
- During the transportation phase, the vaporized atoms may react with gases introduced into the chamber (such as oxygen or nitrogen) to form compounds like oxides or nitrides.
- These reactions can enhance the properties of the coating, such as increasing hardness or improving resistance to corrosion.
-
Deposition onto the Substrate:
- The final step involves the deposition of the vaporized atoms onto the substrate. This occurs as the atoms condense and form a thin film on the surface.
- The deposition process is controlled to ensure uniformity and desired thickness, often using monitoring tools like quartz crystal rate monitors.
-
Environmental Conditions:
- The PVD process is conducted in a vacuum or low-pressure environment to prevent contamination and ensure the purity of the coating.
- Temperatures within the chamber typically range from 50 to 600 degrees Celsius, depending on the materials and desired coating properties.
-
Types of PVD Methods:
- Sputtering: This method involves ejecting atoms from the target material by bombarding it with high-energy ions. The ejected atoms then deposit onto the substrate.
- Thermal Evaporation: In this method, the target material is heated until it evaporates, and the vaporized atoms are then deposited onto the substrate.
- Spraying: This technique removes surface atoms from the target and deposits them onto the substrate, often used for creating uniform coatings.
-
Advantages of PVD:
- Durability: PVD coatings are known for their hardness and resistance to wear and corrosion.
- Versatility: The process can be applied to a wide range of materials, including metals, ceramics, and polymers.
- Precision: PVD allows for the creation of thin films with precise thickness and composition, making it ideal for applications requiring high performance.
-
Applications:
- PVD is widely used in industries such as aerospace, automotive, electronics, and medical devices. It is particularly valued for creating coatings that enhance the performance and longevity of components.
By understanding these key points, one can appreciate the complexity and precision involved in the PVD process, making it a critical technology in modern manufacturing and material science.
Summary Table:
Key Aspect | Details |
---|---|
Process Steps | Evaporation, Transportation, Chemical Reactions (optional), Deposition |
Environmental Conditions | Vacuum or low-pressure, 50-600°C temperature range |
PVD Methods | Sputtering, Thermal Evaporation, Spraying |
Advantages | Durability, Versatility, Precision |
Applications | Aerospace, Automotive, Electronics, Medical Devices |
Learn how PVD can enhance your manufacturing process—contact our experts today!