The process of thin film optical coating involves depositing thin layers of material onto a substrate to alter its optical properties, such as reflectivity, transmittance, or absorption. The two primary techniques used are Physical Vapor Deposition (PVD) and Chemical Vapor Deposition (CVD). PVD includes methods like thermal evaporation, electron-beam deposition, and sputtering, where the material is vaporized in a vacuum and then condenses on the substrate. CVD involves chemical reactions where precursor gases decompose on a heated substrate to form a solid film. These techniques are chosen based on the desired film properties, substrate material, and application requirements. Additionally, other methods like Atomic Layer Deposition (ALD) and Spray Pyrolysis are used for specific applications requiring precise control over film thickness and composition.
Key Points Explained:
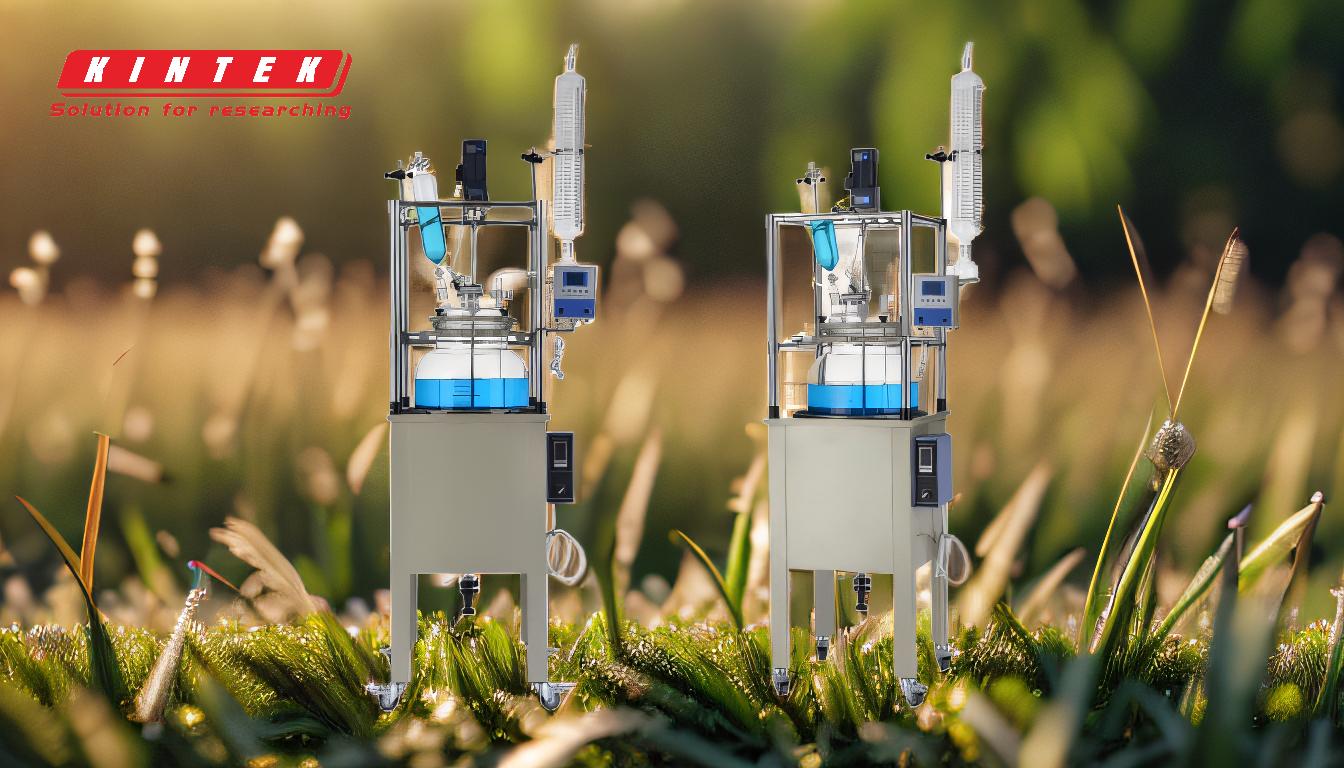
-
Overview of Thin Film Optical Coating:
- Thin film optical coating involves depositing ultra-thin layers of materials onto a substrate to modify its optical properties.
- These coatings are used in applications like anti-reflective coatings, mirrors, filters, and optical lenses.
-
Primary Deposition Techniques:
-
Physical Vapor Deposition (PVD):
- Involves vaporizing the coating material in a vacuum, which then condenses on the substrate.
- Common PVD methods include:
- Thermal Evaporation: Material is heated until it vaporizes and deposits onto the substrate.
- Electron-Beam Deposition: An electron beam heats the material, causing it to vaporize and deposit.
- Sputtering: High-energy ions bombard the target material, ejecting atoms that deposit onto the substrate.
-
Chemical Vapor Deposition (CVD):
- Involves a chemical reaction where precursor gases decompose on a heated substrate to form a solid film.
- CVD enables uniform coating over large areas and is suitable for complex geometries.
- Variants include Plasma-Enhanced CVD (PECVD) and Atomic Layer Deposition (ALD).
-
Physical Vapor Deposition (PVD):
-
Other Deposition Methods:
-
Atomic Layer Deposition (ALD):
- Deposits films one atomic layer at a time, providing exceptional control over film thickness and uniformity.
- Ideal for applications requiring precise nanoscale coatings.
-
Spray Pyrolysis:
- Involves spraying a material solution onto the substrate, followed by thermal decomposition to form a thin film.
- Suitable for large-area coatings and cost-effective production.
-
Electroplating and Sol-Gel:
- Electroplating uses an electric current to deposit metal ions onto a substrate.
- Sol-Gel involves converting a liquid solution into a solid film through chemical reactions.
-
Atomic Layer Deposition (ALD):
-
Factors Influencing Deposition Method Selection:
- Substrate Material: The compatibility of the substrate with the deposition process.
- Film Properties: Desired optical, mechanical, and thermal properties of the coating.
- Application Requirements: Specific needs like thickness control, uniformity, and scalability.
- Cost and Complexity: Economic and technical feasibility of the method.
-
Applications of Thin Film Optical Coatings:
- Anti-Reflective Coatings: Reduce reflection and enhance light transmission in lenses and displays.
- Mirrors and Filters: Improve reflectivity or selectively transmit specific wavelengths.
- Optical Lenses: Enhance performance by controlling light behavior.
- Solar Panels: Increase efficiency by optimizing light absorption.
-
Advantages and Challenges:
-
Advantages:
- High precision and control over film properties.
- Ability to deposit a wide range of materials.
- Suitable for complex and large-area substrates.
-
Challenges:
- High equipment and operational costs for some methods.
- Requires specialized knowledge and expertise.
- Potential for defects or non-uniformities in the film.
-
Advantages:
By understanding these key points, one can better appreciate the complexity and versatility of thin film optical coating processes, as well as the factors to consider when selecting a deposition method for specific applications.
Summary Table:
Aspect | Details |
---|---|
Primary Techniques | - PVD: Thermal Evaporation, Electron-Beam Deposition, Sputtering |
- CVD: Chemical reactions, Plasma-Enhanced CVD (PECVD), ALD | |
Other Methods | - ALD: Precise nanoscale coatings |
- Spray Pyrolysis: Cost-effective, large-area coatings | |
Applications | - Anti-reflective coatings, mirrors, filters, optical lenses, solar panels |
Advantages | - High precision, wide material range, suitable for complex substrates |
Challenges | - High costs, specialized expertise, potential defects |
Discover the best thin film optical coating solution for your needs—contact our experts today!