Twin screw granulation is a continuous process widely used in the pharmaceutical industry to produce granules with consistent quality. It involves feeding raw materials into a twin screw extruder, where they are mixed, heated, and compressed under controlled conditions. The process ensures uniform thermal and mixing histories, resulting in granules with improved physical and chemical properties compared to traditional batch methods. This method is particularly advantageous for its scalability, efficiency, and ability to handle heat-sensitive materials.
Key Points Explained:
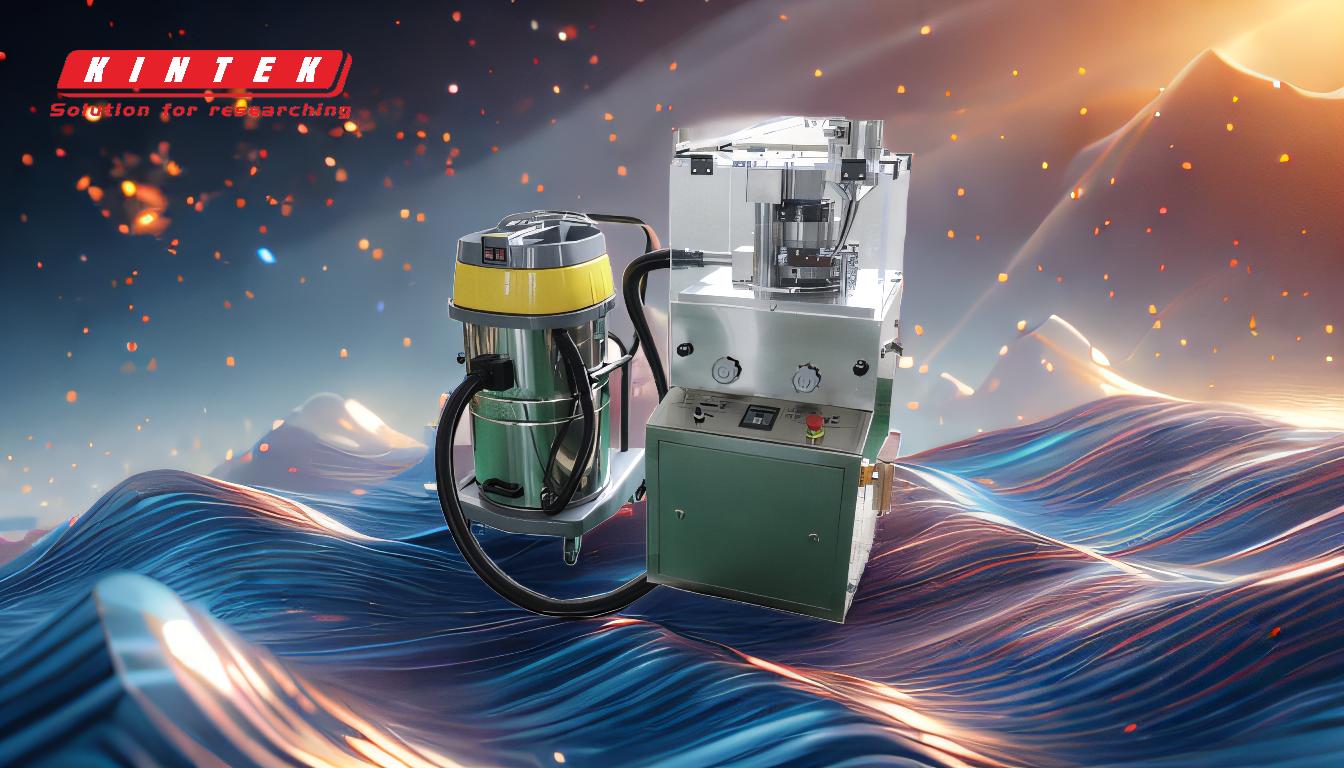
-
Overview of Twin Screw Granulation:
- Twin screw granulation is a continuous process that uses a twin screw extruder to mix, heat, and compress raw materials into granules.
- It is widely adopted in the pharmaceutical industry due to its ability to produce granules with consistent quality and uniform properties.
-
Key Components of the Process:
- Feeding System: Raw materials are fed into the extruder in a controlled manner, ensuring a steady flow.
- Twin Screw Extruder: The extruder consists of two intermeshing screws that rotate within a barrel. The screws are designed to mix, heat, and compress the materials as they move through the barrel.
- Heating and Mixing Zones: The extruder barrel is divided into zones with controlled temperatures. These zones facilitate melting, mixing, and granule formation.
- Die and Cutting System: At the end of the extruder, the material passes through a die to form strands, which are then cut into granules of the desired size using a precision cutting machine .
-
Advantages of Twin Screw Granulation:
- Consistent Quality: The continuous operation ensures uniform thermal and mixing histories, leading to granules with consistent physical and chemical properties.
- Scalability: The process is easily scalable from lab-scale to industrial production.
- Efficiency: Twin screw granulation is more efficient than batch processes, reducing production time and energy consumption.
- Versatility: It can handle a wide range of materials, including heat-sensitive compounds, and can be adapted for various formulations.
-
Process Parameters and Control:
- Screw Configuration: The design of the screws (e.g., conveying, kneading, and mixing elements) influences the mixing efficiency and granule properties.
- Temperature Control: Precise control of barrel temperatures is crucial to prevent degradation of heat-sensitive materials and ensure proper melting and mixing. A heating circulator is often used to maintain consistent temperatures.
- Screw Speed: The rotation speed of the screws affects the residence time and shear forces, which in turn influence granule size and density.
- Feed Rate: The rate at which raw materials are fed into the extruder must be optimized to maintain steady-state operation and achieve the desired granule properties.
-
Applications in the Pharmaceutical Industry:
- Twin screw granulation is used to produce granules for tablet compression, capsule filling, and other dosage forms.
- It is particularly beneficial for formulating drugs with poor solubility, as the process can enhance drug dissolution and bioavailability.
- The method is also suitable for continuous manufacturing, aligning with the industry's shift towards more efficient and flexible production systems.
-
Comparison with Batch Processes:
- Twin screw granulation offers several advantages over traditional batch granulation methods, such as high-shear granulation or fluid bed granulation.
- The continuous nature of twin screw granulation reduces variability between batches, leading to more consistent product quality.
- It also allows for better control over process parameters, resulting in granules with improved uniformity and performance.
In summary, twin screw granulation is a highly efficient and versatile process that has become a preferred method in the pharmaceutical industry for producing high-quality granules. Its ability to operate continuously with precise control over process parameters makes it ideal for modern manufacturing needs.
Summary Table:
Aspect | Details |
---|---|
Process Type | Continuous granulation using a twin screw extruder |
Key Components | Feeding system, twin screw extruder, heating/mixing zones, die/cutting system |
Advantages | Consistent quality, scalability, efficiency, versatility for heat-sensitive materials |
Process Parameters | Screw configuration, temperature control, screw speed, feed rate |
Applications | Tablet compression, capsule filling, enhancing drug solubility |
Comparison to Batch | Reduces variability, better control, improved uniformity and performance |
Learn how twin screw granulation can optimize your pharmaceutical production— contact our experts today !