Vacuum carburizing, also known as low-pressure carburizing (LPC), is a heat treatment process that enhances the surface hardness of steel or alloy components by infusing carbon into their surface layers. This process is conducted in a vacuum furnace, where the metal is heated to high temperatures (typically between 1,600 and 1,950 °F or 870 and 1,070 °C). A carbon-rich gas, such as propane or acetylene, is introduced into the furnace, where it breaks down into carbon and hydrogen due to the heat. The carbon then diffuses into the metal's surface, increasing its hardness. The process involves alternating cycles of gas introduction and diffusion, followed by quenching in oil or high-pressure gas (HPGQ) to achieve the desired hardness and case depth. This method is highly controlled, ensuring uniform carbon penetration without surface contamination.
Key Points Explained:
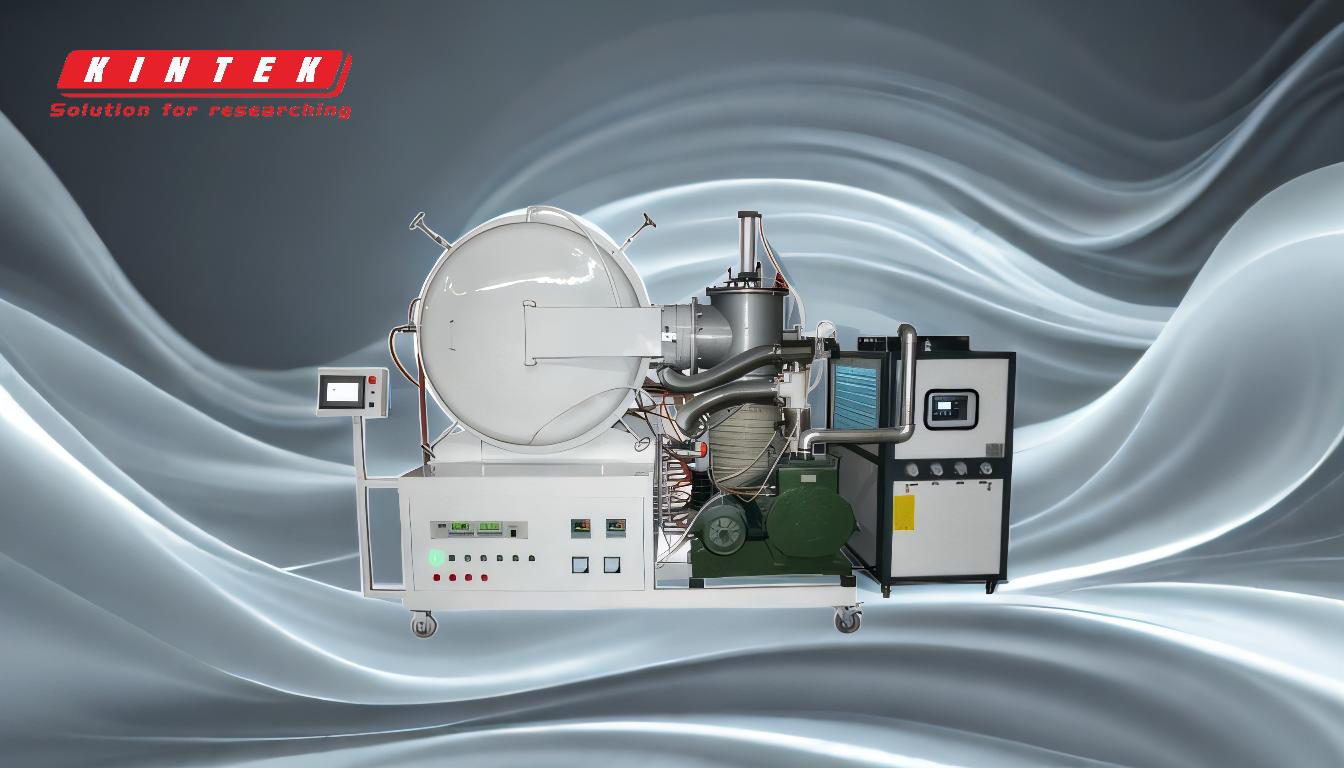
-
Introduction to Vacuum Carburizing
- Vacuum carburizing is a heat treatment process used to increase the surface hardness of steel or alloy components by introducing carbon into their surface layers.
- It is also referred to as low-pressure carburizing (LPC) and is conducted in a vacuum furnace to eliminate external contaminants and ensure a pure carburizing environment.
-
Process Overview
- The process involves placing the metal in a vacuum furnace, heating it to a specific temperature, introducing a carbon-rich gas, and allowing the carbon to diffuse into the metal surface.
- The steps include:
- Loading the metal into the vacuum furnace.
- Heating the metal to the required temperature (typically 1,600–1,950 °F or 870–1,070 °C).
- Introducing a carbon-rich gas (e.g., propane or acetylene) into the furnace.
- Allowing the gas to break down into carbon and hydrogen due to the high temperature.
- Enabling the carbon to diffuse into the metal surface.
- Quenching the metal to achieve the desired hardness.
-
Carbon Source and Gas Breakdown
- The carbon-rich gas (e.g., propane or acetylene) is introduced into the furnace as a partial pressure.
- At high temperatures, the gas disassociates into its constituent elements: carbon and hydrogen.
- The carbon atoms diffuse into the metal surface, while the hydrogen is evacuated from the furnace.
-
Diffusion and Case Hardening
- The carbon diffusion process is repeated in cycles, with varying durations of gas input and diffusion time, to achieve the desired case depth and hardness.
- The process ensures uniform carbon penetration, resulting in a hardened surface layer (case) while maintaining the core properties of the metal.
-
Quenching
- After the carburizing process, the metal is quenched to lock in the hardness.
- Quenching can be done using oil or high-pressure gas (HPGQ), with nitrogen or helium commonly used for faster cooling rates.
- The quenching method depends on the material and the desired mechanical properties.
-
Advantages of Vacuum Carburizing
- Purity: The vacuum environment eliminates surface contamination and ensures a clean, controlled process.
- Uniformity: The process provides consistent carbon penetration and case depth.
- Efficiency: The use of high-pressure gas quenching reduces cycle times and improves productivity.
- Environmental Benefits: The process produces fewer emissions compared to traditional gas carburizing methods.
-
Applications
- Vacuum carburizing is widely used in industries requiring high-performance components, such as automotive, aerospace, and tool manufacturing.
- Common applications include gears, shafts, bearings, and other parts requiring high surface hardness and wear resistance.
By following this structured process, vacuum carburizing ensures precise control over the hardening of metal components, making it a preferred method for achieving high-quality, durable parts.
Summary Table:
Aspect | Details |
---|---|
Process Name | Vacuum Carburizing (Low-Pressure Carburizing) |
Temperature Range | 1,600–1,950 °F (870–1,070 °C) |
Carbon Source | Propane or Acetylene |
Key Steps | Heating, Gas Introduction, Carbon Diffusion, Quenching |
Quenching Methods | Oil or High-Pressure Gas (HPGQ) |
Advantages | Purity, Uniformity, Efficiency, Environmental Benefits |
Applications | Automotive, Aerospace, Tool Manufacturing (gears, shafts, bearings, etc.) |
Discover how vacuum carburizing can improve your metal components—contact us today for expert advice!