Vacuum tempering is a specialized heat treatment process used to enhance the mechanical properties of metals, particularly steel, while maintaining a bright, oxidation-free surface. This process is ideal for materials like mould steel, high-temperature alloys, and titanium alloys, where surface quality and precise mechanical properties are critical. The vacuum tempering process involves heating the material in a vacuum environment to a specific temperature, holding it for a predetermined time, and then cooling it rapidly using inert gases like argon. This ensures that the material achieves the desired balance of hardness and ductility without surface oxidation or contamination.
Key Points Explained:
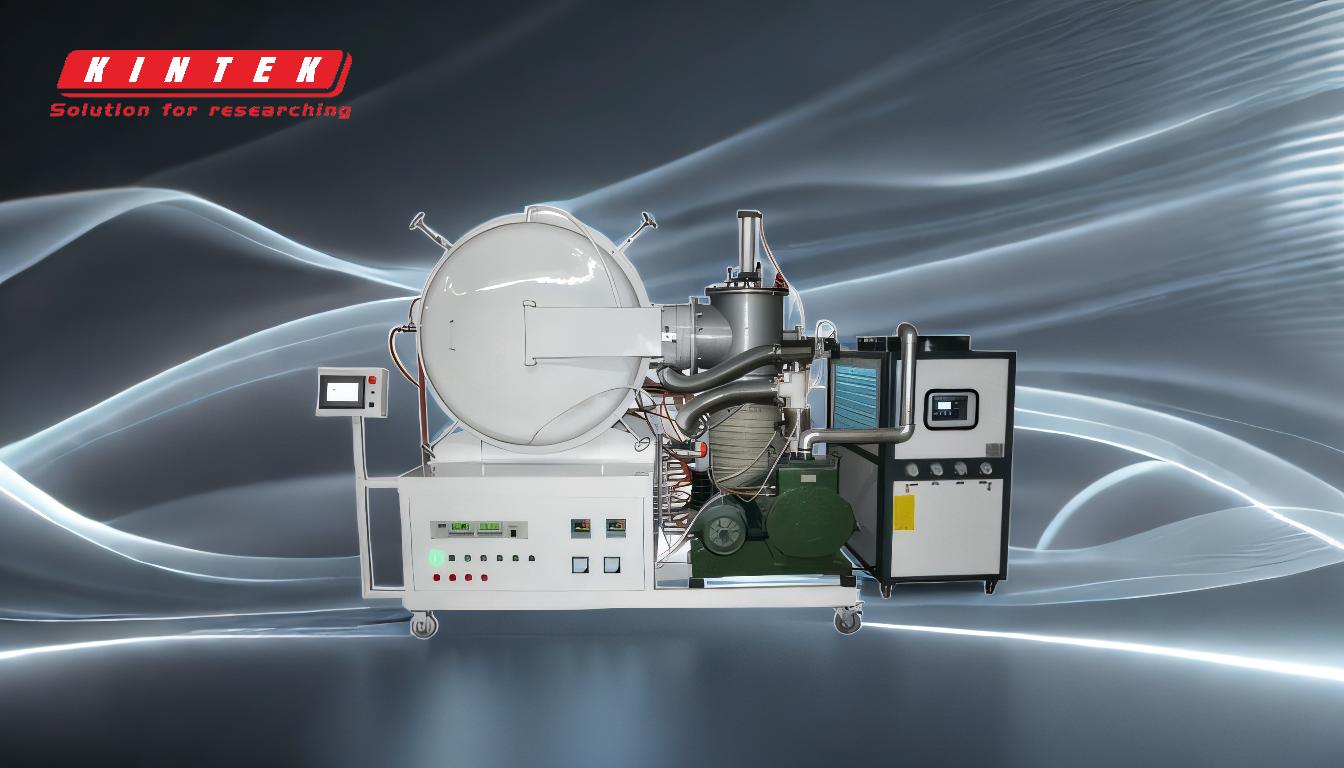
-
Purpose of Vacuum Tempering:
- Vacuum tempering is used to improve the mechanical properties of metals, such as hardness, durability, and resistance to deformation, while preventing oxidation and maintaining a bright surface finish.
- It is particularly suitable for materials like mould steel, high-temperature alloys, and titanium alloys, which require precise control over their microstructure and surface quality.
-
Equipment Used: Vacuum Furnace:
- The process is carried out in a vacuum furnace, which consists of two main systems: the vacuum system and the heating system.
- The vacuum system removes oxygen and other gases from the chamber, creating an environment free from oxidation and contamination.
- The heating system ensures precise temperature control, which is critical for achieving the desired material properties.
-
Steps in the Vacuum Tempering Process:
- Loading the Furnace: The workpiece is placed inside the vacuum chamber. This step ensures that the material is properly positioned for uniform heating and cooling.
- Creating a Vacuum: The vacuum system, including mechanical pumps and diffusion pumps, removes oxygen and other gases from the chamber. This step is crucial to prevent oxidation and contamination.
- Heating the Workpiece: The material is heated to a specific temperature, typically below the critical temperature for the material, and held at this temperature for a predetermined time. This allows the material to achieve the desired microstructure.
- Cooling the Workpiece: After heating, the workpiece is rapidly cooled using inert gases like argon. This controlled cooling process ensures that the material achieves the right balance of hardness and ductility without oxidation.
-
Cooling Mechanism:
- The cooling process in vacuum tempering is facilitated by inert gases like argon, which are pumped into the chamber to rapidly lower the temperature of the workpiece.
- This rapid cooling, or quenching, is essential for achieving the desired mechanical properties and ensuring consistency in the heat treatment process.
-
Applications of Vacuum Tempering:
- Vacuum tempering is widely used in industries that require high-performance materials, such as aerospace, automotive, and tool manufacturing.
- It is particularly beneficial for materials that need to withstand extreme conditions, such as high temperatures, stress, and wear.
-
Advantages of Vacuum Tempering:
- Oxidation-Free Surface: The vacuum environment prevents oxidation, ensuring a bright and clean surface finish.
- Precise Control: The process allows for precise control over temperature and cooling rates, resulting in consistent and high-quality results.
- Enhanced Material Properties: Vacuum tempering improves the hardness, durability, and resistance to deformation of the material, making it suitable for demanding applications.
By following these steps and utilizing the capabilities of a vacuum furnace, vacuum tempering provides a reliable and efficient method for enhancing the performance of critical metal components while maintaining their surface integrity.
Summary Table:
Key Aspect | Details |
---|---|
Purpose | Improves hardness, durability, and resistance to deformation; prevents oxidation. |
Equipment | Vacuum furnace with vacuum and heating systems. |
Process Steps | 1. Load workpiece. 2. Create vacuum. 3. Heat material. 4. Rapidly cool with argon. |
Applications | Aerospace, automotive, tool manufacturing, and high-performance materials. |
Advantages | Oxidation-free surface, precise control, enhanced material properties. |
Discover how vacuum tempering can optimize your metal components—contact our experts today!