Vacuum Induction Melting (VIM) is a sophisticated process used primarily for producing high-purity metals and alloys. The process involves several critical steps, each contributing to the overall quality and properties of the final product. These steps include the selection and preparation of the crucible, charge preparation, melting and refining, and pouring. Each of these stages requires precise control and attention to detail to ensure the desired outcomes.
Key Points Explained:
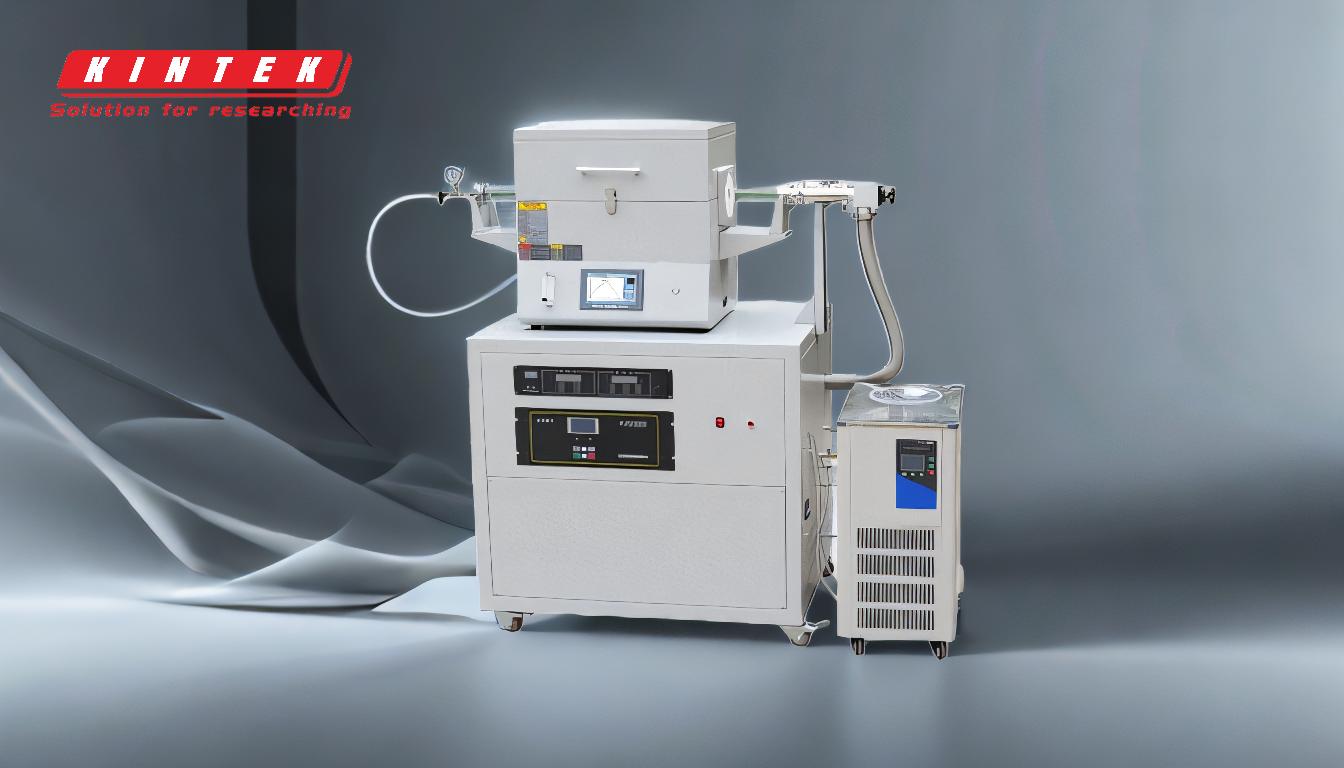
-
Selection and Preparation of the Crucible:
- Material Selection: The crucible, which holds the metal during melting, is typically made from materials that can withstand high temperatures and are chemically inert to the metal being melted. Common materials include graphite, ceramics, and certain refractory metals.
- Pre-treatment: Before use, the crucible may undergo treatments such as coating or pre-heating to enhance its durability and to prevent contamination of the melt. This step is crucial for maintaining the purity of the metal.
-
Charge Preparation:
- Selection of Raw Materials: The charge, or the raw materials to be melted, must be carefully selected based on the desired composition of the final product. This can include pure metals, alloys, and sometimes additives to achieve specific properties.
- Cleaning and Drying: The charge materials are often cleaned and dried to remove any surface contaminants or moisture that could affect the melting process or the quality of the final product.
-
Melting and Refining:
- Vacuum Environment: The melting process takes place in a vacuum to prevent oxidation and to remove dissolved gases from the melt. This environment is crucial for producing high-purity metals.
- Induction Heating: An induction coil generates a magnetic field that induces eddy currents in the metal, causing it to heat up and melt. This method allows for precise control over the temperature and heating rate.
- Refining: During melting, various refining processes may occur, such as degassing, deoxidation, and the removal of volatile impurities. These processes are essential for achieving the desired chemical composition and mechanical properties of the metal.
-
Pouring:
- Temperature Control: The molten metal must be poured at the correct temperature to ensure proper flow and solidification. Temperature control is critical to avoid defects in the final product.
- Mold Preparation: The molds used for casting the molten metal must be prepared and preheated to the appropriate temperature to prevent thermal shock and to ensure a smooth surface finish.
- Pouring Technique: The technique used to pour the molten metal into the mold can affect the quality of the final product. Techniques such as tilt pouring or bottom pouring are often used to minimize turbulence and the introduction of impurities.
Each of these steps in the VIM process is interdependent and requires meticulous execution to produce high-quality metals and alloys. The ability to control the environment and the parameters of each step is what makes VIM a preferred method for producing materials with stringent purity and performance requirements.
Summary Table:
Step | Key Details |
---|---|
Crucible Preparation | - Material: Graphite, ceramics, refractory metals. |
- Pre-treatment: Coating, pre-heating to prevent contamination. | |
Charge Preparation | - Raw materials: Pure metals, alloys, additives. |
- Cleaning & drying: Removes contaminants and moisture. | |
Melting & Refining | - Vacuum environment: Prevents oxidation, removes dissolved gases. |
- Induction heating: Precise temperature control. | |
- Refining: Degassing, deoxidation, impurity removal. | |
Pouring | - Temperature control: Ensures proper flow and solidification. |
- Mold preparation: Preheated to prevent thermal shock. | |
- Pouring technique: Minimizes turbulence and impurities. |
Discover how VIM can elevate your metal production—contact our experts today for tailored solutions!