Magnetron sputtering is a widely used thin film deposition technique that leverages a gaseous plasma and kinetic energy to coat surfaces under vacuum conditions. High-energy ions bombard a target material, causing atoms to be ejected and form a vapor cloud, which then deposits onto a substrate to create a thin film. This method is highly versatile, allowing for the deposition of a wide range of materials, including metals, alloys, and ceramics. Key parameters such as target power density, gas pressure, substrate temperature, and deposition rate play a critical role in determining the quality and properties of the deposited films. Magnetron sputtering is particularly valued for its ability to produce uniform, dense, and adherent films, making it suitable for both laboratory research and high-volume industrial production.
Key Points Explained:
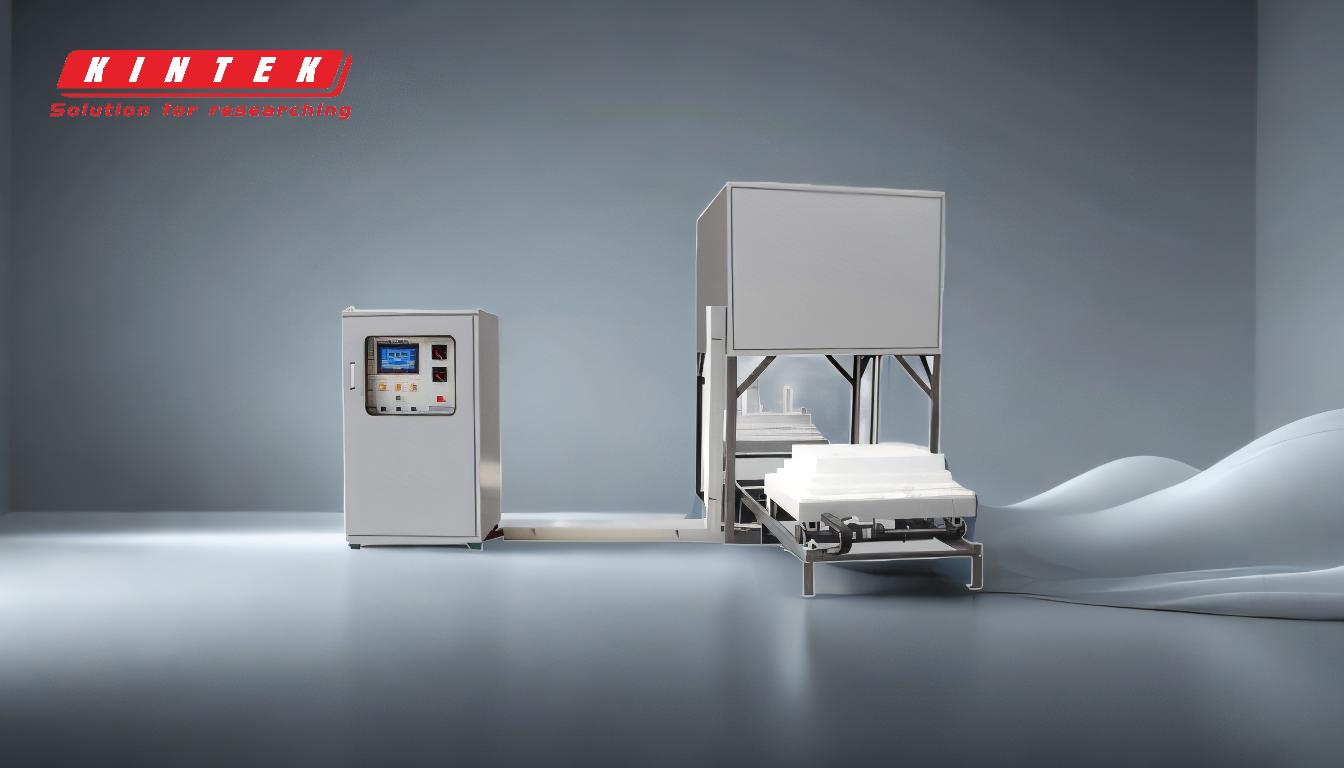
-
Basic Principle of Magnetron Sputtering:
- Magnetron sputtering involves the use of a gaseous plasma to generate high-energy ions that bombard a target material.
- These ions liberate atoms from the target, which then form a vapor cloud.
- The vapor cloud deposits onto a substrate, creating a thin film.
-
Key Parameters Influencing Film Quality:
- Target Power Density: Higher power densities can increase the rate of sputtering, but must be balanced to avoid damaging the target or substrate.
- Gas Pressure: Optimal gas pressure is crucial for maintaining a stable plasma and controlling the energy of the sputtered atoms.
- Substrate Temperature: Temperature affects the mobility of atoms on the substrate surface, influencing film morphology and adhesion.
- Deposition Rate: Controlling the deposition rate is essential for achieving the desired film thickness and uniformity.
-
Advantages of Magnetron Sputtering:
- Material Versatility: A wide range of materials, including metals, alloys, and ceramics, can be used as targets.
- Co-Sputtering: Multiple targets can be used simultaneously to deposit precise alloy compositions.
- Reactive Sputtering: The addition of reactive gases allows for the deposition of compound films, such as oxides or nitrides.
- Uniformity and Precision: The technique is capable of producing films with highly uniform thickness and precise control over film properties.
- High Efficiency: Magnetron sputtering is suitable for high-volume production due to its fast coating rates and the ability to produce dense, adherent films.
-
Applications of Magnetron Sputtering:
- Optical Coatings: Used to create reflective, anti-reflective, or transparent coatings for optical components.
- Electrical Coatings: Applied in the production of conductive layers, insulating films, and semiconductor devices.
- Decorative Coatings: Utilized for aesthetic purposes, such as in the automotive and jewelry industries.
- Protective Coatings: Provides wear resistance, corrosion protection, and improved durability for various surfaces.
-
Modern Developments in Magnetron Sputtering:
- Advanced Power Supplies: Modern power supplies offer high stability and precise control over the plasma, leading to improved film quality and process reproducibility.
- Scalability: The technique can be scaled to coat very large surfaces, making it suitable for industrial applications.
- Material Independence: Magnetron sputtering can be used to coat most common surfaces with a variety of materials, making it a flexible and powerful deposition method.
In summary, magnetron sputtering is a highly versatile and efficient thin film deposition technique that offers precise control over film properties and is suitable for a wide range of applications. Its ability to produce uniform, dense, and adherent films makes it a preferred choice in both research and industrial settings.
Summary Table:
Aspect | Details |
---|---|
Basic Principle | High-energy ions bombard a target, ejecting atoms to form a vapor cloud. |
Key Parameters | Target power density, gas pressure, substrate temperature, deposition rate. |
Advantages | Material versatility, co-sputtering, reactive sputtering, uniformity. |
Applications | Optical coatings, electrical coatings, decorative & protective coatings. |
Modern Developments | Advanced power supplies, scalability, material independence. |
Unlock the potential of pulse magnetron sputtering for your applications—contact us today for expert guidance!