A burnout furnace, also known as a casting furnace or wax elimination furnace, is a specialized piece of equipment primarily used in the dental and jewelry industries. Its main purpose is to remove wax patterns or organic materials from investment molds before casting metal. This process, known as dewaxing, ensures that the mold is clean and ready for the metal casting process. Burnout furnaces are designed with specific features such as high-temperature capabilities, programmable controls, and safety mechanisms to ensure efficient and safe operation. They are essential for creating precise and high-quality dental restorations and jewelry pieces.
Key Points Explained:
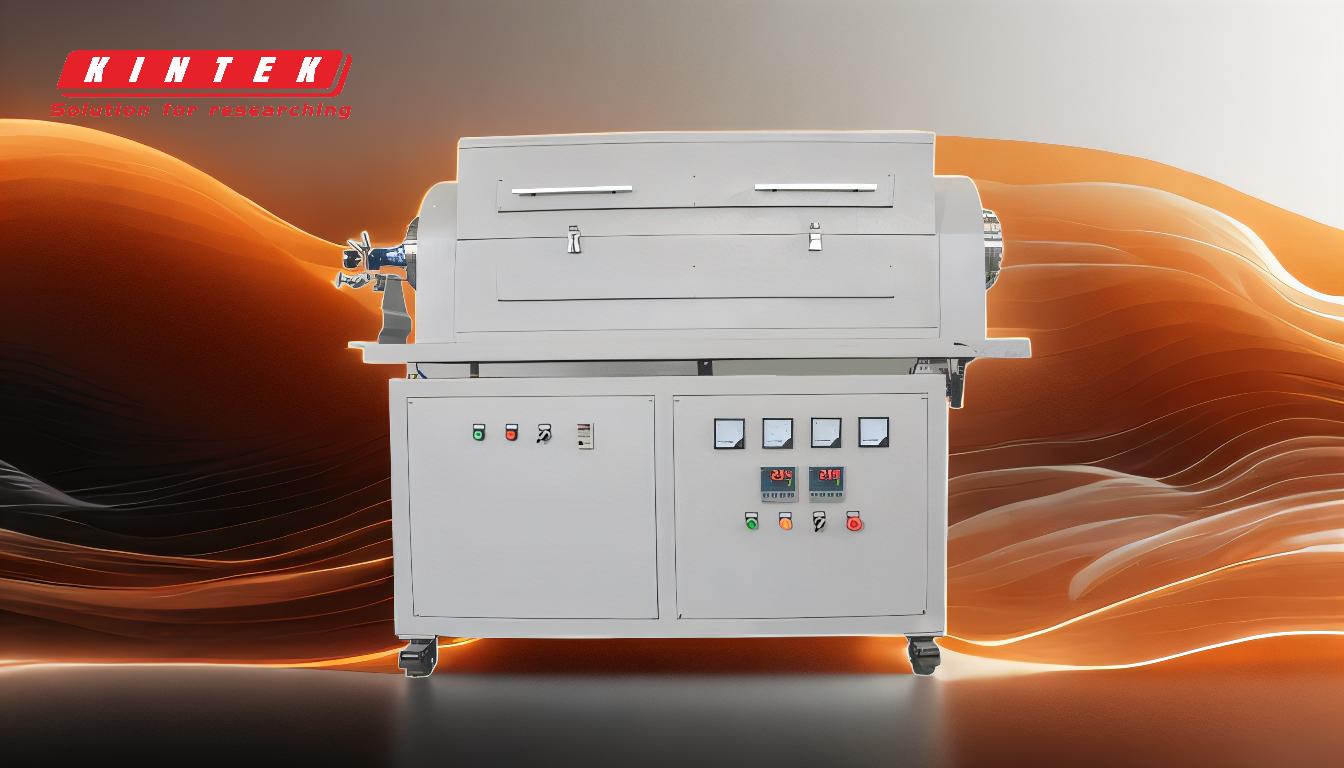
-
Primary Purpose of a Burnout Furnace:
- The burnout furnace is primarily used for the removal of wax patterns or organic materials from investment molds. This process is crucial in the dental and jewelry industries, where precision and cleanliness of the mold are essential for high-quality metal casting.
- In dentistry, it is used for dental dewaxing casting and the heat treatment of 3D metal printer restorations. This ensures that the final dental restorations, such as crowns and bridges, are free from any residual wax or organic material.
-
Process of Dewaxing:
- The burnout furnace heats the investment mold to a high temperature, typically up to 1200°C, to burn out the wax or organic material. This process leaves a clean cavity in the mold, which is then filled with molten metal to create the final product.
- The furnace's programmable controls allow for precise temperature management, ensuring that the wax is completely removed without damaging the mold.
-
Key Features of a Burnout Furnace:
- High-Temperature Capability: Burnout furnaces can reach temperatures up to 1200°C, which is necessary for effectively burning out wax and organic materials.
- Programmable Controls: These furnaces often feature 30-segment programmable controls, allowing for precise temperature regulation and automated operation.
- Safety Features: The furnace is designed with a double-layer steel casing and fan cooling to ensure that the surface temperature remains below 50°C, protecting the operator from burns.
- Efficient Heating: The ceramic fiber furnace chamber ensures fast heating and energy efficiency, making the process both quick and cost-effective.
-
Applications in Different Industries:
- Dental Industry: In dentistry, burnout furnaces are used for dental dewaxing casting and the heat treatment of 3D metal printer restorations. This is essential for creating accurate and high-quality dental prosthetics.
- Jewelry Industry: In jewelry making, burnout furnaces are used to remove wax from investment molds before casting precious metals like gold and silver. This ensures that the final jewelry pieces are free from defects and have a high level of detail.
-
Comparison with Other Types of Furnaces:
- High-Temperature Furnace: While a high-temperature furnace is used for elemental analysis, heat treatment (such as hardening and annealing), and sintering, a burnout furnace is specifically designed for dewaxing and organic material removal.
- Melting Furnace: A melting furnace is used to liquefy solid materials, whereas a burnout furnace is used to remove wax or organic materials from molds.
- Muffle Furnace: A muffle furnace is used to heat materials without contamination from combustion gases, making it suitable for scientific research. In contrast, a burnout furnace is designed for dewaxing and heat treatment in industrial applications.
-
Importance in Dental and Jewelry Manufacturing:
- In both the dental and jewelry industries, the burnout furnace plays a critical role in ensuring the precision and quality of the final products. By completely removing wax or organic materials, the furnace ensures that the molds are clean and ready for metal casting, resulting in high-quality dental restorations and jewelry pieces.
-
Safety and Efficiency Considerations:
- The design of the burnout furnace prioritizes operator safety and energy efficiency. Features like the double-layer steel casing and fan cooling ensure that the furnace can operate at high temperatures without posing a risk to the operator. Additionally, the ceramic fiber furnace chamber allows for rapid heating, reducing the time and energy required for the dewaxing process.
In summary, the burnout furnace is an essential piece of equipment in the dental and jewelry industries, designed to remove wax and organic materials from investment molds before metal casting. Its high-temperature capabilities, programmable controls, and safety features make it a reliable and efficient tool for producing high-quality dental restorations and jewelry pieces.
Summary Table:
Feature | Details |
---|---|
Primary Purpose | Removes wax or organic materials from investment molds (dewaxing). |
Temperature Range | Up to 1200°C for effective wax burnout. |
Programmable Controls | 30-segment controls for precise temperature management. |
Safety Features | Double-layer steel casing, fan cooling, surface temperature below 50°C. |
Applications | Dental dewaxing casting, heat treatment of 3D metal printer restorations, jewelry casting. |
Efficiency | Ceramic fiber chamber for fast heating and energy efficiency. |
Upgrade your dental or jewelry production with a burnout furnace—contact us today to learn more!