Heat treatment of metals is a critical process used to alter the physical and sometimes chemical properties of a material, primarily to improve its mechanical properties such as hardness, strength, ductility, and resistance to wear. The process involves heating the metal to a specific temperature, holding it at that temperature for a certain period, and then cooling it in a controlled manner. This treatment is essential in various industries, including automotive, aerospace, and manufacturing, where the performance and durability of metal components are paramount. The controlled atmosphere during heat treatment prevents contamination and ensures the metal retains its desired properties. Additionally, heat treatment is vital in metal additive manufacturing to relieve residual stresses and prevent warping of 3D printed models. Vacuum heat treatment further enhances these benefits by preventing oxidation and minimizing distortion, leading to superior mechanical properties and dimensional stability.
Key Points Explained:
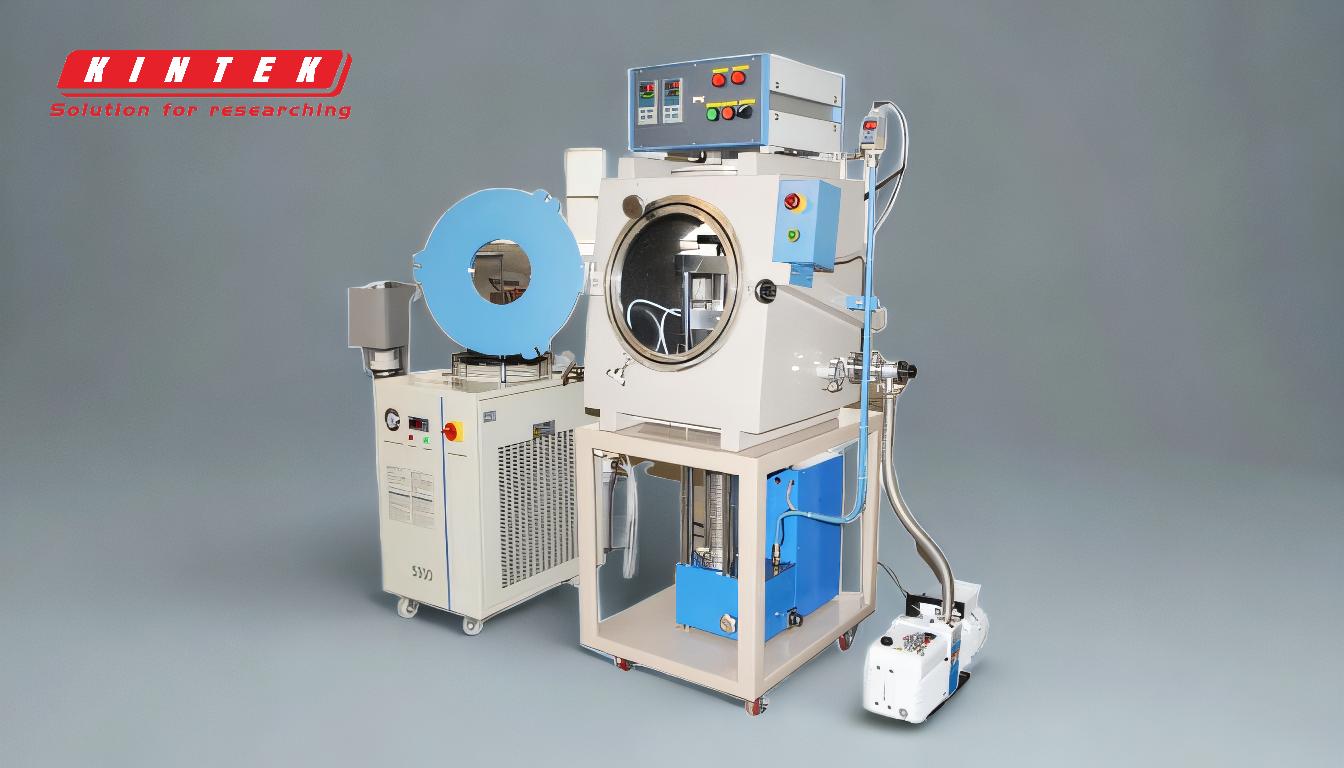
-
Enhancement of Mechanical Properties:
- Heat treatment significantly improves the mechanical properties of metals, such as hardness, strength, and ductility. By heating the metal to a specific temperature and then cooling it in a controlled manner, the internal structure of the metal is altered, leading to enhanced performance characteristics. This is crucial for applications where metals are subjected to high stress or wear.
-
Stress Relief in Additive Manufacturing:
- In metal additive manufacturing, such as SLM/DMLS/L-PBF processes, heat treatment is essential to relieve residual stresses that accumulate during the printing process. The intense laser radiation causes thermal expansion in the top layer, while the lower layers cool and contract, creating a stress gradient. Without heat treatment, these stresses can lead to build failure or plastic deformation. Heat treatment ensures the final product is dimensionally stable and free from warping.
-
Controlled Atmosphere for Quality Assurance:
- A controlled atmosphere during heat treatment is vital to prevent contamination of the metal. Contamination can lead to increased brittleness, corrosion, and other forms of damage, compromising the metal's quality and performance. By maintaining a controlled environment, the metal retains its desired properties, ensuring consistent and reliable results.
-
Vacuum Heat Treatment for Superior Results:
- Vacuum heat treatment offers additional benefits by preventing oxidation and minimizing the risk of distortion. This process enhances the hardness, strength, and wear resistance of metals while preserving their dimensional stability. The absence of oxygen in the vacuum environment ensures that the metal surfaces remain clean and free from oxidation, leading to superior performance and durability.
-
Consistency and Repeatability:
- Consistency in heat treatment processes, especially in vacuum heat treatment, ensures repeatable results. The controlled environment and precise parameters guarantee that each treatment cycle meets stringent quality assurance standards. This predictability is critical for industries where components must meet specific performance criteria consistently.
-
Application in Various Industries:
- Heat treatment is widely used in industries such as automotive, aerospace, and manufacturing. In the automotive industry, heat-treated components are essential for engines, transmissions, and suspension systems, where high strength and wear resistance are required. In aerospace, heat-treated metals are used in critical components that must withstand extreme conditions. The manufacturing sector relies on heat treatment to produce durable tools and machinery parts.
-
Prevention of Warping and Distortion:
- Heat treatment is particularly important in preventing warping and distortion in metal parts. This is especially true for complex geometries produced through additive manufacturing. By relieving residual stresses and ensuring uniform cooling, heat treatment helps maintain the dimensional accuracy and integrity of the final product.
In summary, heat treatment is a fundamental process that enhances the mechanical properties of metals, ensures dimensional stability, and prevents warping and distortion. The controlled atmosphere and precise parameters of heat treatment processes, including vacuum heat treatment, are essential for achieving consistent and reliable results across various industries.
Summary Table:
Key Benefits of Heat Treating Metals | Details |
---|---|
Enhancement of Mechanical Properties | Improves hardness, strength, ductility, and wear resistance. |
Stress Relief in Additive Manufacturing | Prevents warping and ensures dimensional stability in 3D printed parts. |
Controlled Atmosphere | Prevents contamination, ensuring consistent quality. |
Vacuum Heat Treatment | Prevents oxidation, minimizes distortion, and enhances durability. |
Consistency and Repeatability | Ensures reliable results for critical applications. |
Industry Applications | Used in automotive, aerospace, and manufacturing sectors. |
Prevention of Warping and Distortion | Maintains dimensional accuracy in complex geometries. |
Learn how heat treatment can optimize your metal components—contact our experts today!