An induction furnace is a highly efficient and environmentally friendly tool used primarily in foundries for melting metals such as iron, steel, copper, aluminum, and precious metals. Its purpose is to melt metals at regulated temperatures, preserving their alloying elements while minimizing contamination and pollution. Unlike traditional furnaces, induction furnaces use electromagnetic induction to generate heat directly within the metal, ensuring precise temperature control, energy efficiency, and a cleaner melting process. This makes them ideal for producing high-quality castings with minimal waste and environmental impact. Induction furnaces are also praised for their fast heating speed, reduced oxidation, and improved working conditions, making them a preferred choice in modern industrial settings.
Key Points Explained:
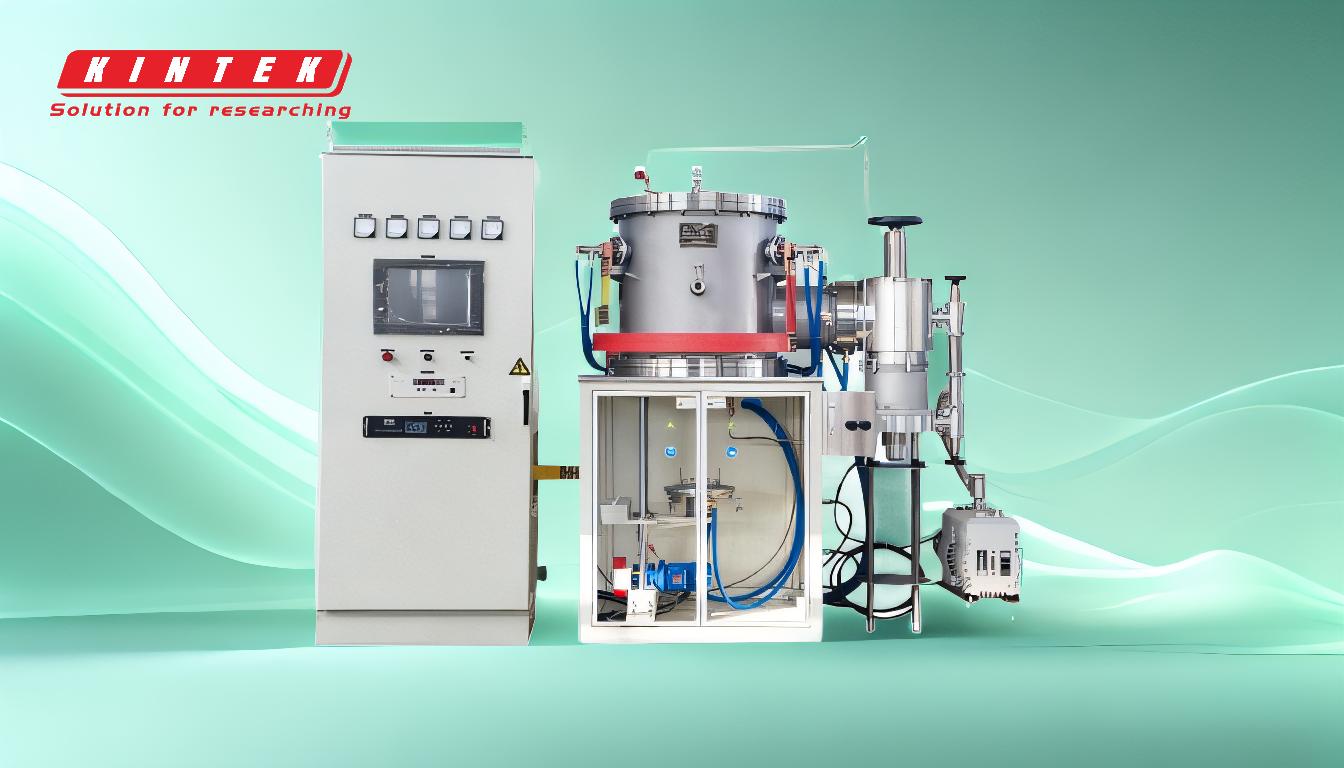
-
Primary Purpose: Melting Metals
- Induction furnaces are designed to melt a wide range of metals, including ferrous (iron, steel) and non-ferrous (copper, aluminum, precious metals) alloys.
- The molten metal is then poured into molds to create castings, which are used in various industrial applications.
- This process is crucial in foundries for producing high-quality metal components.
-
Preservation of Alloying Elements
- One of the key advantages of induction furnaces is their ability to regulate melting temperatures precisely.
- This ensures that valuable alloying elements within the metal are retained, maintaining the material's desired properties and quality.
- Unlike traditional furnaces, induction furnaces minimize the risk of oxidation and decarburization, which can degrade the metal's integrity.
-
Energy Efficiency and Environmental Benefits
- Induction furnaces are highly energy-efficient, as they generate heat directly within the metal charge using electromagnetic induction.
- This method eliminates the need for combustion or arcs, reducing energy consumption and minimizing greenhouse gas emissions.
- The absence of dust and other pollutants makes induction furnaces a cleaner and safer option for both workers and the environment.
-
Controlled and Clean Melting Process
- The induction furnace's design ensures a contained and controlled melting process, reducing the risk of contamination from external heat sources.
- The electromagnetic stirring action creates a homogeneous mixture of liquid metals, eliminating the need for manual sampling and ensuring consistent quality.
- This precision makes induction furnaces ideal for applications requiring high-temperature control accuracy and minimal material loss.
-
Operational Advantages
- Induction furnaces heat metals rapidly, increasing production efficiency and reducing downtime.
- They are versatile and can operate in various environments, including atmospheric or vacuum conditions, depending on the application.
- The lack of combustion or open flames makes the temperature safer to work with, improving overall workplace safety.
-
Replacing Traditional Furnaces
- Many older foundries are transitioning from cupolas and gas furnaces to induction furnaces due to their superior efficiency, cleanliness, and control.
- This shift reflects the growing emphasis on sustainable and high-quality manufacturing processes in modern industry.
-
Economic and Practical Benefits
- Induction furnaces save material and forging die costs by reducing oxidation and material waste.
- They provide a superior working environment by eliminating pollution and improving conditions for workers.
- The small temperature difference between the core and surface of the metal ensures uniform heating, further enhancing the quality of the final product.
In summary, the purpose of an induction furnace is to provide a clean, efficient, and precise method for melting metals, ensuring high-quality castings while minimizing environmental impact and operational costs. Its advanced technology and numerous advantages make it an indispensable tool in modern foundries and industrial settings.
Summary Table:
Key Features | Benefits |
---|---|
Melts Various Metals | Iron, steel, copper, aluminum, and precious metals. |
Preserves Alloying Elements | Maintains material quality by minimizing oxidation and decarburization. |
Energy Efficiency | Reduces energy consumption and greenhouse gas emissions. |
Clean Melting Process | Minimizes contamination and pollution, ensuring a safer working environment. |
Fast Heating Speed | Increases production efficiency and reduces downtime. |
Versatile Applications | Operates in atmospheric or vacuum conditions for diverse industrial needs. |
Upgrade your foundry with an induction furnace—contact us today to learn more!