Physical Vapor Deposition (PVD) is a vacuum-based thin-film coating process used to deposit materials at an atomic level onto substrates. It involves vaporizing a solid precursor material under high vacuum and low-temperature conditions, transporting the vaporized atoms to a substrate, and condensing them to form a thin, durable, and highly resistant coating. The process typically includes stages such as evaporation, transportation, reaction, and deposition. PVD is widely used in industries requiring high-performance coatings due to its ability to produce precise, uniform, and durable thin films.
Key Points Explained:
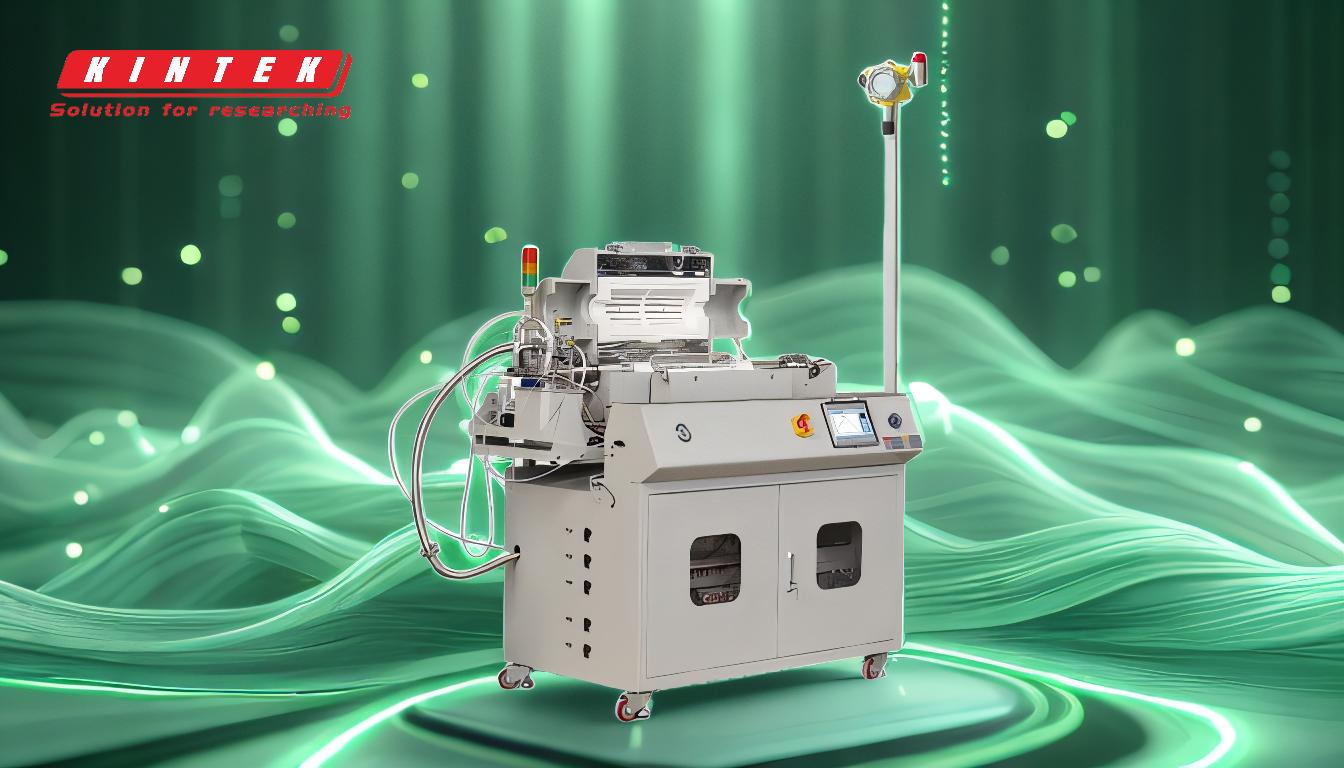
-
Definition and Purpose of PVD:
- PVD is a vacuum-based thin-film deposition technique.
- It is used to create highly durable, resistant, and precise coatings on substrates.
- The process is an alternative to electroplating and is favored for its ability to produce coatings with superior properties.
-
Core Steps in the PVD Process:
- Evaporation: A solid precursor material is vaporized using high-power electricity, lasers, or plasma generation.
- Transportation: The vaporized atoms are transported through a vacuum environment to the substrate.
- Reaction: In some cases, the vaporized atoms react with gases in the chamber to form compound coatings.
- Deposition: The atoms condense on the substrate, forming a thin, uniform film.
-
Key Conditions for PVD:
- High Vacuum: The process occurs in a low-pressure environment to ensure minimal contamination and precise control over deposition.
- Low Temperatures: Compared to other deposition methods, PVD operates at relatively low temperatures, making it suitable for heat-sensitive substrates.
-
Types of PVD Techniques:
- Sputtering: A target material is bombarded with ions, causing atoms to be ejected and deposited onto the substrate.
- Thermal Evaporation: The source material is heated until it vaporizes, and the vapor condenses on the substrate.
- Arc Vapor Deposition: An electric arc is used to vaporize the source material, which is then deposited onto the substrate.
- Laser Ablation: A high-energy laser vaporizes the source material, and the vapor is deposited onto the substrate.
-
Advantages of PVD:
- High Precision: PVD allows for the deposition of very thin and uniform coatings, often at the nanometer scale.
- Durability: The coatings are highly resistant to wear, corrosion, and oxidation.
- Versatility: PVD can deposit a wide range of materials, including metals, alloys, and ceramics.
- Environmentally Friendly: Unlike electroplating, PVD does not involve hazardous chemicals, making it a cleaner process.
-
Applications of PVD:
- Electronics: Used for depositing conductive and insulating layers in semiconductors and microelectronics.
- Optics: Applied in the production of anti-reflective and reflective coatings for lenses and mirrors.
- Automotive: Enhances the durability and appearance of components like engine parts and decorative trims.
- Medical Devices: Provides biocompatible and wear-resistant coatings for surgical instruments and implants.
- Aerospace: Used for protective coatings on turbine blades and other high-stress components.
-
Comparison with Other Deposition Methods:
- PVD vs. CVD (Chemical Vapor Deposition): PVD operates at lower temperatures and does not involve chemical reactions, making it suitable for heat-sensitive materials. CVD, on the other hand, relies on chemical reactions and often requires higher temperatures.
- PVD vs. Electroplating: PVD produces coatings with better adhesion, uniformity, and environmental friendliness compared to electroplating, which can involve toxic chemicals and produce less durable coatings.
In summary, PVD is a versatile and precise thin-film deposition method that offers numerous advantages in terms of durability, precision, and environmental impact. Its applications span across various industries, making it a critical technology for modern manufacturing and material science.
Summary Table:
Aspect | Details |
---|---|
Definition | Vacuum-based thin-film deposition technique for durable, precise coatings. |
Core Steps | Evaporation, Transportation, Reaction, Deposition. |
Key Conditions | High vacuum, low temperatures. |
Types of PVD | Sputtering, Thermal Evaporation, Arc Vapor Deposition, Laser Ablation. |
Advantages | High precision, durability, versatility, environmentally friendly. |
Applications | Electronics, optics, automotive, medical devices, aerospace. |
Comparison | PVD vs. CVD: Lower temperatures, no chemical reactions. |
PVD vs. Electroplating: Better adhesion, uniformity, eco-friendly. |
Discover how PVD can enhance your manufacturing process—contact our experts today!