Induction furnaces are versatile melting devices used primarily in the metallurgical industry to produce steel, alloys, and non-ferrous metals. The raw materials used in induction furnaces vary depending on the type of metal being produced. For steel production, the primary raw material is sponge iron, often constituting 85-90% of the charge mix, supplemented by pig iron (10-15%). Sponge iron is derived from iron ore. For non-ferrous metals like copper and aluminum, the furnace can process pure metals, alloys, or alloyed waste. Induction furnaces are also used for high-purity metals and alloys, particularly in vacuum induction furnaces, which are ideal for materials with high gas affinity or strict chemical composition requirements.
Key Points Explained:
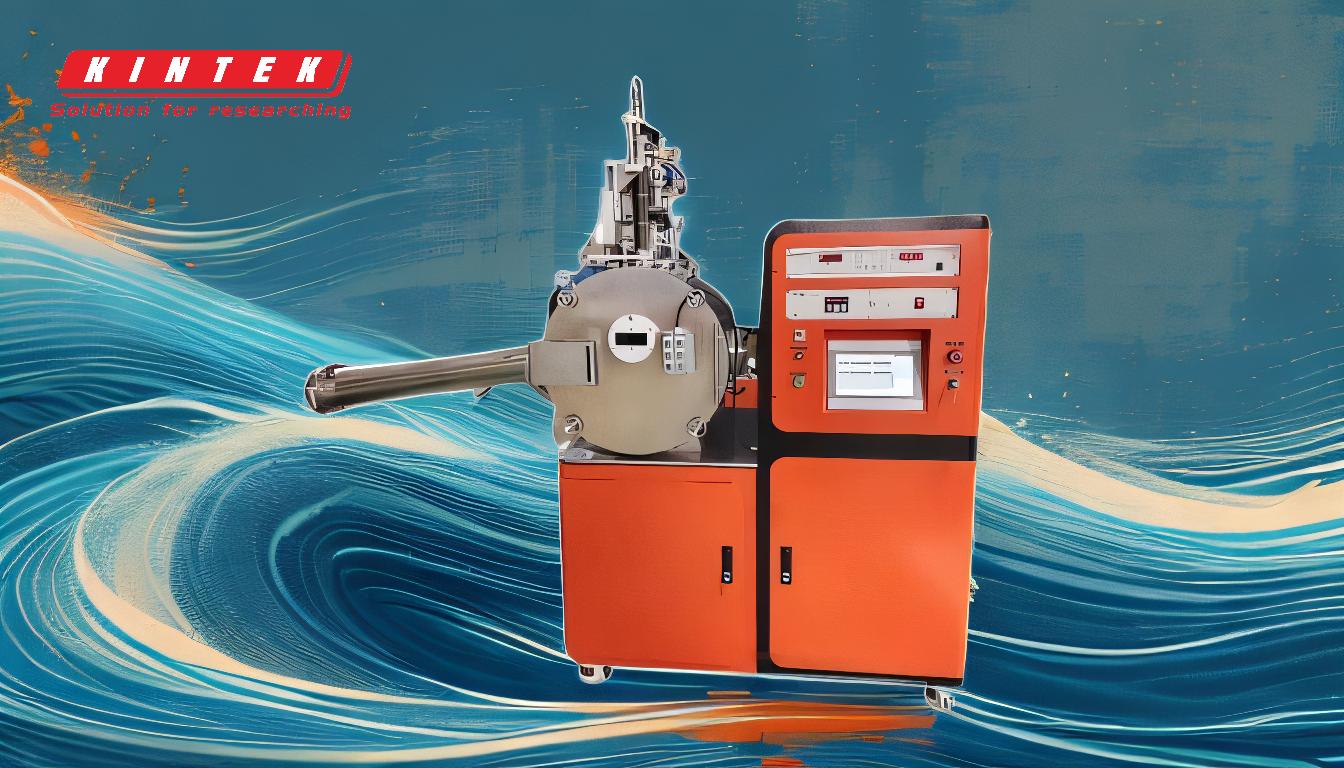
-
Primary Raw Material for Steel Production: Sponge Iron
- Sponge iron is the main raw material used in induction furnaces for steel production, making up 85-90% of the charge mix.
- It is produced from iron ore through a direct reduction process, which removes oxygen from the ore without melting it.
- Sponge iron is preferred due to its high purity and consistency, which ensures better control over the steel's chemical composition.
-
Supplementary Material: Pig Iron
- Pig iron is added to the charge mix in smaller quantities (10-15%) to provide additional carbon and other alloying elements.
- It acts as a balancing agent to achieve the desired properties in the final steel product.
-
Non-Ferrous Metal Raw Materials
- Induction furnaces can also process non-ferrous metals such as copper and aluminum.
- The raw materials for these metals include pure metals, alloyed waste, and ferroalloys.
- This versatility makes induction furnaces suitable for a wide range of applications beyond steel production.
-
High-Purity Materials and Vacuum Induction Furnaces
- Vacuum induction furnaces are used for metals and alloys with high affinity for gases like nitrogen and oxygen.
- These furnaces are ideal for producing high-purity materials or materials with tight chemical composition tolerances.
- Examples include specialty steels, superalloys, and precious metals like gold, silver, and platinum group metals.
-
Components of an Induction Furnace
- The furnace consists of a power supply, an induction coil (or ring), and a crucible made of refractory materials.
- The crucible holds the metal charge, which acts as the secondary winding of a transformer, allowing efficient heating through electromagnetic induction.
-
Applications Beyond Steel
- Induction furnaces are not limited to steel production; they are also used for refining and processing precious metals.
- This includes gold, silver, and platinum group metals, where precise control over melting and alloying is critical.
By understanding the raw materials and their roles in the induction furnace process, purchasers can make informed decisions about the types of materials and furnaces needed for their specific applications. Whether producing steel, refining non-ferrous metals, or working with high-purity alloys, induction furnaces offer a flexible and efficient solution.
Summary Table:
Material Type | Role in Induction Furnace | Percentage/Usage |
---|---|---|
Sponge Iron | Primary raw material for steel production; ensures high purity and consistency. | 85-90% of charge mix |
Pig Iron | Supplementary material; adds carbon and alloying elements for desired steel properties. | 10-15% of charge mix |
Non-Ferrous Metals | Includes copper, aluminum, alloys, and alloyed waste; processed for diverse applications. | Varies by application |
High-Purity Materials | Used in vacuum induction furnaces for metals with high gas affinity or strict composition needs. | Specialized processes |
Discover how induction furnaces can optimize your metal production—contact our experts today!