Rotary kilns are high-temperature processing equipment used in industries like cement production, iron ore reduction, and chemical processing. Their refractory lining is a critical component, as it protects the kiln shell from extreme heat and chemical reactions while ensuring efficient heat transfer to the material being processed. The choice of refractory material depends on the specific process, temperature, and chemical environment within the kiln. Common refractory materials include low-iron alumina, magnesium-spinel bricks, and magnesite bricks, with the selection influenced by factors like wear resistance, thermal conductivity, and chemical stability. Refractories are either castable (poured into place) or brick (manually laid), each offering distinct advantages in terms of installation ease and durability.
Key Points Explained:
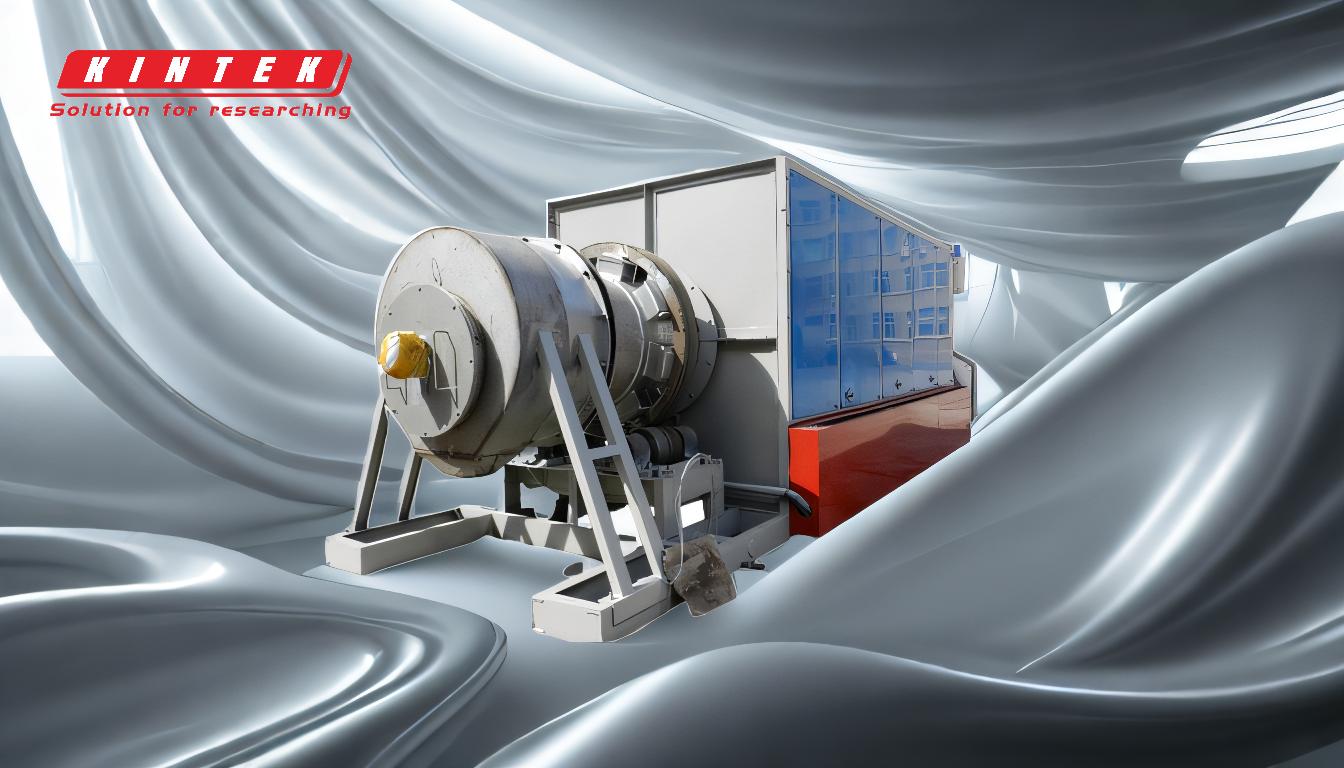
-
Purpose of Refractory Lining in Rotary Kilns:
- The refractory lining serves as a protective barrier between the kiln shell and the high-temperature environment inside the kiln.
- It prevents heat loss, protects the shell from thermal and chemical damage, and ensures efficient heat transfer to the material being processed.
- The lining must withstand extreme temperatures, mechanical stress, and chemical reactions during operation.
-
Factors Influencing Refractory Material Selection:
-
Process Requirements: The type of material being processed (e.g., cement, iron ore, or chemicals) dictates the choice of refractory. For example:
- Low-iron alumina or magnesium-spinel bricks are used in iron ore reduction kilns due to their resistance to reducing atmospheres.
- Magnesite bricks are preferred in cement kilns for their high thermal stability and resistance to alkaline environments.
- Temperature: Refractories must withstand the operating temperature of the kiln, which can exceed 1,400°C in cement kilns.
- Chemical Environment: The refractory must resist chemical reactions with the processed material, gases, and slag.
- Mechanical Stress: The lining must endure abrasion, impact, and thermal cycling.
-
Process Requirements: The type of material being processed (e.g., cement, iron ore, or chemicals) dictates the choice of refractory. For example:
-
Types of Refractory Materials:
-
Brick Refractories:
- Made from pre-formed bricks, typically composed of materials like magnesite, alumina, or spinel.
- Highly wear-resistant, making them suitable for abrasive materials.
- Labor-intensive to install but offer longer service life in harsh conditions.
-
Castable Refractories:
- Composed of refractory aggregates and binders, poured into place to form a monolithic lining.
- Easier and faster to install compared to bricks.
- Less wear-resistant but suitable for less abrasive environments or areas with complex geometries.
-
Brick Refractories:
-
Common Refractory Materials Used in Rotary Kilns:
- Low-Iron Alumina: Used in iron ore reduction kilns due to its resistance to reducing atmospheres and high thermal stability.
- Magnesium-Spinel Bricks: Offer excellent thermal shock resistance and are used in high-temperature applications.
- Magnesite Bricks: Preferred in cement kilns for their resistance to alkaline environments and high thermal conductivity.
-
Installation Methods:
-
Brick Lining:
- Bricks are laid manually, often with mortar or specialized adhesives.
- Provides a durable and wear-resistant lining but requires skilled labor and longer installation time.
-
Castable Lining:
- Poured into place and cured to form a monolithic structure.
- Faster installation and better adaptability to complex shapes but may require additional curing time.
-
Brick Lining:
-
Performance Considerations:
- Thermal Conductivity: Refractories must balance heat retention and transfer to ensure efficient processing.
- Wear Resistance: The lining must withstand abrasion from the material being processed.
- Chemical Stability: Resistance to reactions with processed materials, gases, and slag is critical.
- Thermal Shock Resistance: The ability to withstand rapid temperature changes without cracking.
-
Maintenance and Lifespan:
- Regular inspection and maintenance are required to monitor refractory wear and prevent failures.
- The lifespan of the refractory lining depends on the material, operating conditions, and maintenance practices.
- Damaged or worn refractory sections can be replaced individually, minimizing downtime.
In summary, the refractory material in a rotary kiln is a vital component that ensures efficient and safe operation. The choice of material depends on the specific process, temperature, and chemical environment, with options like low-iron alumina, magnesium-spinel, and magnesite bricks being commonly used. Both brick and castable refractories have their advantages, with bricks offering superior wear resistance and castables providing easier installation. Proper selection, installation, and maintenance of the refractory lining are essential for maximizing the kiln's performance and lifespan.
Summary Table:
Key Aspect | Details |
---|---|
Purpose | Protects kiln shell, ensures heat transfer, and withstands extreme conditions. |
Material Selection Factors | Process type, temperature, chemical environment, and mechanical stress. |
Common Materials | Low-iron alumina, magnesium-spinel bricks, magnesite bricks. |
Installation Methods | Brick (manual, durable) or castable (poured, faster installation). |
Performance Considerations | Thermal conductivity, wear resistance, chemical stability, thermal shock. |
Maintenance | Regular inspections and replacements to maximize lifespan. |
Optimize your rotary kiln's performance with the right refractory lining—contact our experts today!