The refractory materials used in muffle furnaces are primarily selected for their ability to withstand high temperatures, resist chemical corrosion, and provide effective insulation. The most common materials include alumina ceramic, quartz glass, ceramic fiber, and refractory bricks. Alumina ceramic is highly valued for its durability, high-temperature resistance, and corrosion resistance, making it ideal for the furnace chamber. Quartz glass, on the other hand, is chosen for its transparency, allowing for observation of the experimental process. Ceramic fiber and refractory bricks are used for insulation, with ceramic fiber being lightweight and offering excellent heat preservation, while refractory bricks provide robust structural support and general heat retention. Multi-layer insulation designs often combine these materials to optimize energy efficiency and thermal performance.
Key Points Explained:
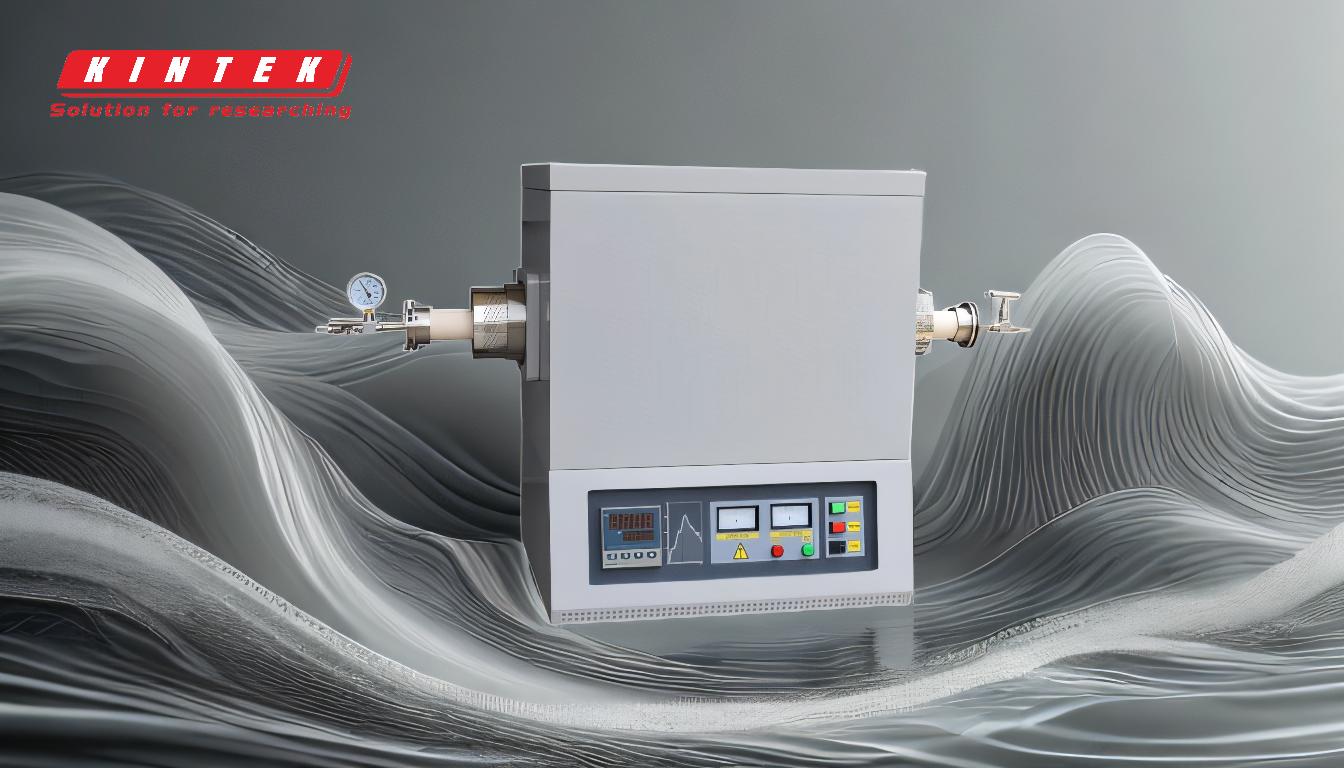
-
Alumina Ceramic:
- Alumina ceramic is a widely used refractory material in muffle furnaces due to its exceptional properties.
- It can withstand extremely high temperatures, often exceeding 1600°C, making it suitable for high-temperature applications.
- Its resistance to chemical corrosion ensures durability, even when exposed to aggressive substances during experiments or industrial processes.
- Alumina ceramic is also known for its mechanical strength, which prevents deformation or cracking under thermal stress.
-
Quartz Glass:
- Quartz glass is another material used in muffle furnaces, particularly in applications where visibility into the furnace chamber is required.
- It has a high melting point and excellent thermal stability, making it suitable for high-temperature environments.
- Its transparency allows users to monitor the progress of experiments without opening the furnace, reducing heat loss and improving efficiency.
- However, quartz glass is less commonly used than alumina ceramic due to its higher cost and lower mechanical strength.
-
Ceramic Fiber:
- Ceramic fiber is a lightweight insulation material that is soft and easy to handle.
- It provides excellent heat preservation, reducing energy consumption by minimizing heat loss.
- Ceramic fiber is often used in multi-layer insulation designs, where it is combined with other materials to enhance thermal efficiency.
- Its lightweight nature makes it ideal for applications where reducing the overall weight of the furnace is important.
-
Refractory Bricks:
- Refractory bricks are heavier and harder compared to ceramic fiber, offering robust structural support for the furnace chamber.
- They provide general heat preservation and are often used in combination with other materials to improve insulation.
- Refractory bricks are made from materials like alumina or silicon carbide, which enhance their thermal and chemical resistance.
- While they are less efficient at insulation compared to ceramic fiber, their durability makes them suitable for high-stress environments.
-
Multi-Layer Insulation Design:
- Modern muffle furnaces often use a multi-layer insulation design to optimize thermal performance.
- This design typically combines lightweight alumina ceramic fiber with high-quality insulation boards, creating a barrier that minimizes heat loss.
- The absence of asbestos in these designs ensures safety and compliance with environmental regulations.
- Multi-layer insulation not only improves energy efficiency but also ensures uniform temperature distribution within the furnace chamber.
-
Material Selection for Specific Applications:
- The choice of refractory material depends on the specific requirements of the application, such as temperature range, chemical exposure, and the need for observation.
- For example, alumina ceramic is preferred for high-temperature and corrosive environments, while quartz glass is chosen for applications requiring visibility.
- Ceramic fiber is ideal for lightweight insulation, whereas refractory bricks are used for structural integrity and general heat retention.
By carefully selecting and combining these materials, muffle furnaces achieve optimal performance, ensuring durability, energy efficiency, and precise temperature control.
Summary Table:
Material | Key Properties | Common Uses |
---|---|---|
Alumina Ceramic | High-temperature resistance, corrosion resistance, durability | Furnace chamber, high-temperature applications |
Quartz Glass | Transparency, thermal stability | Applications requiring visibility |
Ceramic Fiber | Lightweight, excellent heat preservation | Insulation, multi-layer designs |
Refractory Bricks | Structural support, general heat retention | High-stress environments, insulation |
Need help selecting the right refractory material for your muffle furnace? Contact our experts today!