The cracking furnace is a critical piece of equipment in the petrochemical industry, primarily used to break down large hydrocarbon molecules into smaller, more valuable ones through a process called pyrolysis or thermal cracking. This process occurs at high temperatures and often in the presence of steam, converting heavy hydrocarbons like naphtha, ethane, or gas oil into lighter olefins such as ethylene and propylene, which are essential building blocks for plastics, chemicals, and other industrial products. The cracking furnace operates under carefully controlled conditions to maximize yield, ensure safety, and minimize environmental impact.
Key Points Explained:
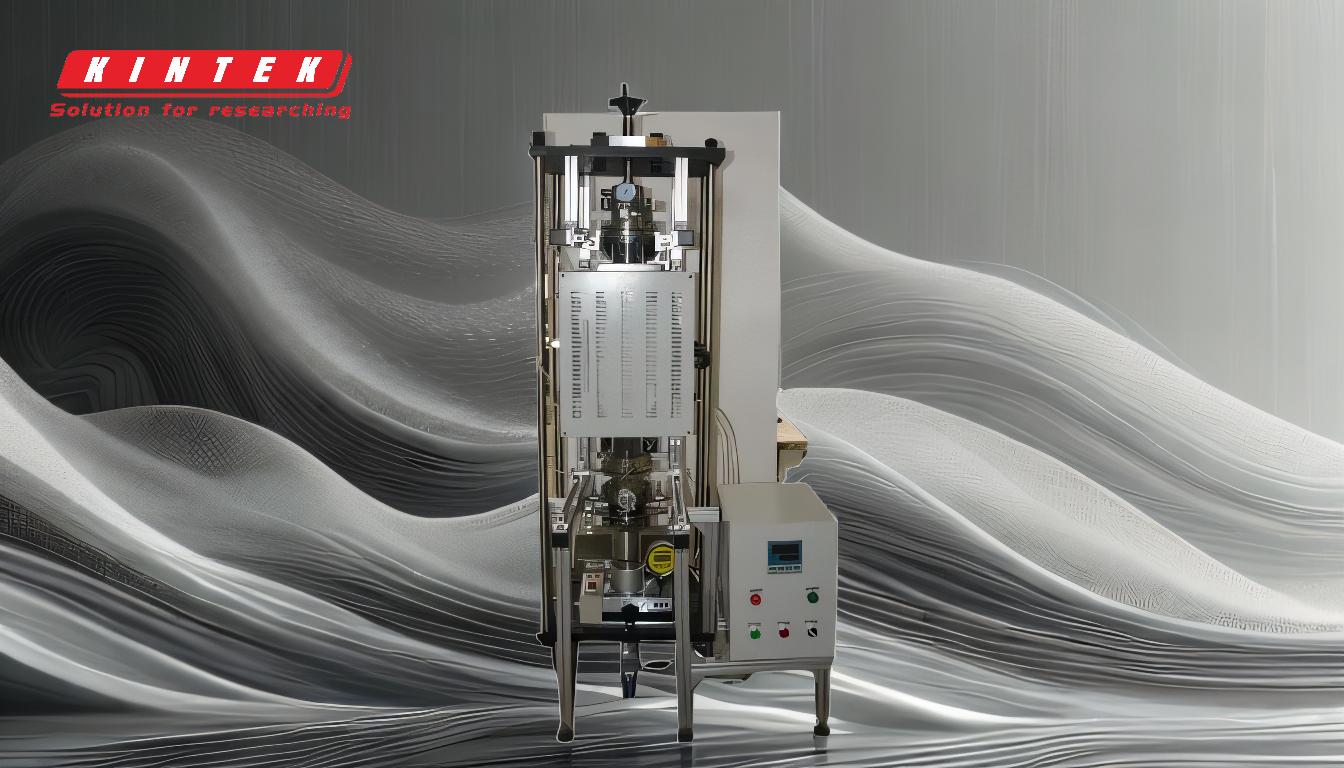
-
Purpose of the Cracking Furnace:
- The primary role of the cracking furnace is to perform thermal cracking, a process that breaks down large hydrocarbon molecules into smaller, more useful ones. This is achieved by heating the feedstock to extremely high temperatures (typically between 750°C and 950°C) in the presence or absence of steam.
- The process is fundamental in producing olefins like ethylene and propylene, which are key raw materials for manufacturing plastics, synthetic rubber, and other petrochemical products.
-
Components of a Cracking Furnace:
- Radiant Section: This is where the actual cracking reaction takes place. The feedstock is heated by burners that generate high temperatures, causing the hydrocarbon molecules to break apart.
- Convection Section: This section preheats the feedstock and superheats the steam before they enter the radiant section, improving energy efficiency.
- Burners: These provide the necessary heat for the cracking process. They are designed to ensure uniform heating and efficient fuel combustion.
- Tubes: The feedstock flows through specially designed tubes in the radiant section, where the cracking reaction occurs. These tubes are made from high-temperature-resistant alloys to withstand the harsh conditions.
- Quench System: After cracking, the hot gases are rapidly cooled (quenched) to stop further reactions and preserve the desired products.
-
Types of Feedstock:
- The cracking furnace can process a variety of feedstocks, including:
- Naphtha: A light distillate from crude oil refining, commonly used in regions with limited access to natural gas.
- Ethane: A component of natural gas, favored for its high ethylene yield.
- Propane: Another natural gas component, used to produce both ethylene and propylene.
- Gas Oil: A heavier feedstock used in some regions, though it yields less ethylene compared to lighter feedstocks.
- The cracking furnace can process a variety of feedstocks, including:
-
Process Conditions:
- Temperature: The cracking reaction requires extremely high temperatures, typically between 750°C and 950°C, to break the strong carbon-carbon bonds in the hydrocarbon molecules.
- Pressure: The process is usually carried out at low pressures to favor the formation of lighter olefins.
- Steam: Steam is often added as a diluent to reduce the partial pressure of hydrocarbons, minimize unwanted side reactions, and prevent coke formation inside the tubes.
-
Importance of Ethylene and Propylene Production:
- Ethylene: One of the most important petrochemicals, used to produce polyethylene (the most common plastic), ethylene oxide, and other chemicals.
- Propylene: Used to manufacture polypropylene, acrylonitrile, and other industrial chemicals. Both ethylene and propylene are essential for a wide range of consumer and industrial products.
-
Safety and Environmental Considerations:
- Safety: The high temperatures and flammable nature of the feedstocks require stringent safety measures, including advanced control systems, fire detection, and emergency shutdown mechanisms.
- Environmental Impact: Modern cracking furnaces are designed to minimize emissions of greenhouse gases and other pollutants. Technologies like flue gas treatment and energy recovery systems are employed to reduce the environmental footprint.
-
Energy Efficiency and Optimization:
- Cracking furnaces are energy-intensive, so optimizing energy use is critical. Techniques such as heat integration, advanced burner designs, and improved insulation are used to enhance efficiency.
- Operators also focus on maximizing the yield of desired products while minimizing the formation of by-products like methane and heavier hydrocarbons.
-
Role in the Petrochemical Value Chain:
- The cracking furnace is a cornerstone of the petrochemical industry, enabling the conversion of raw hydrocarbons into valuable intermediates. These intermediates are further processed into a wide range of end products, from plastics and resins to solvents and synthetic fibers.
- Without cracking furnaces, the production of many modern materials and chemicals would not be economically viable.
In summary, the cracking furnace plays a pivotal role in the petrochemical industry by enabling the production of essential chemicals like ethylene and propylene. Its design, operation, and optimization are critical to ensuring high yields, safety, and environmental sustainability in the production of these valuable building blocks for countless industrial and consumer products.
Summary Table:
Aspect | Details |
---|---|
Purpose | Breaks down large hydrocarbons into smaller, valuable olefins like ethylene and propylene. |
Key Components | Radiant section, convection section, burners, tubes, quench system. |
Feedstock Types | Naphtha, ethane, propane, gas oil. |
Process Conditions | High temperatures (750°C–950°C), low pressure, steam as a diluent. |
Key Products | Ethylene, propylene—essential for plastics and chemicals. |
Safety & Environment | Advanced safety systems, emission control, and energy recovery technologies. |
Energy Efficiency | Heat integration, advanced burners, and insulation for optimization. |
Learn how cracking furnaces can optimize your petrochemical processes—contact us today for expert advice!