A vacuum plays a critical role in deposition processes, particularly in Physical Vapor Deposition (PVD), by creating an environment that minimizes contamination and enhances the quality of the deposited material. In a vacuum, the density of atoms is significantly reduced, which increases the mean free path of atoms, allowing for better control over the deposition process. This environment also facilitates high thermal evaporation rates and prevents unwanted reactions with atmospheric gases, ensuring a cleaner and more precise deposition. Additionally, vacuum systems, such as those in vacuum cleaning furnaces, contribute to environmental sustainability by eliminating waste emissions and reducing pollution.
Key Points Explained:
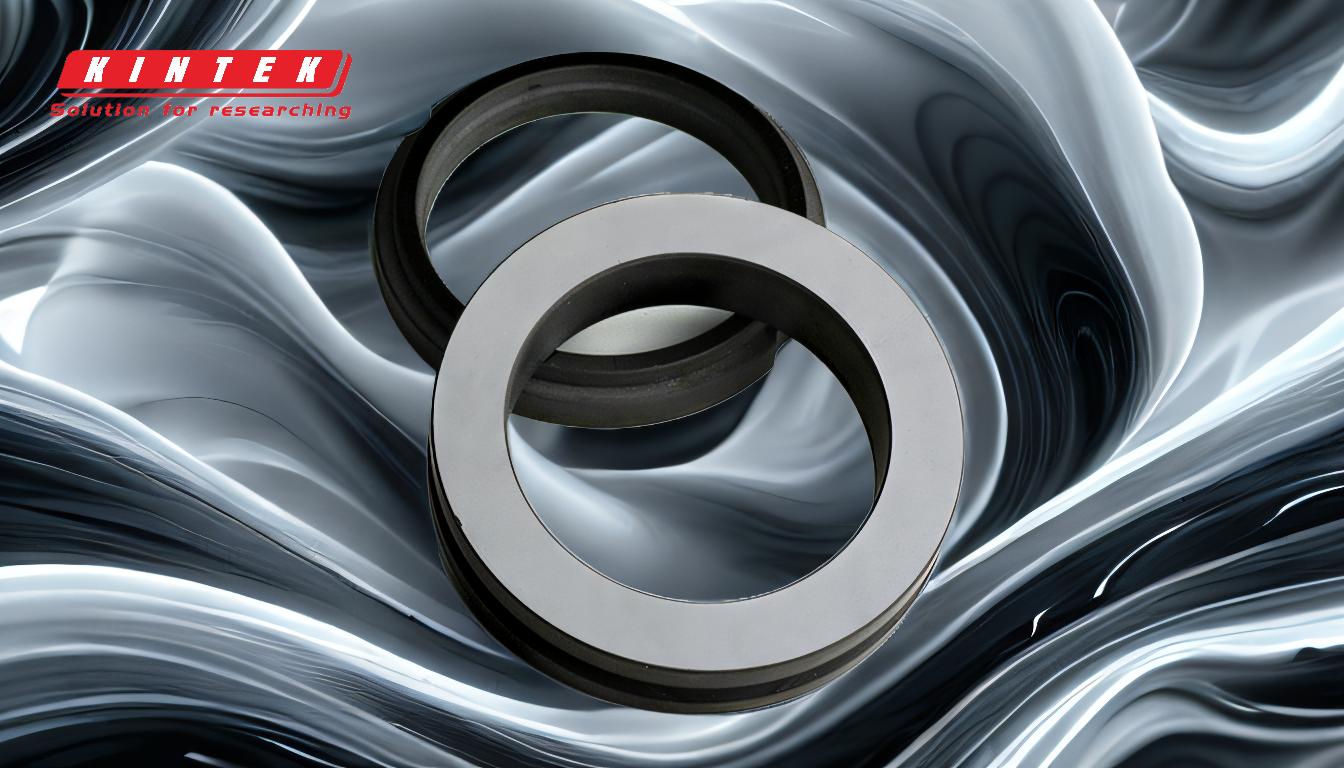
-
Reduction of Atomic Density and Increased Mean Free Path:
- In a vacuum environment, the density of atoms is drastically reduced. This reduction increases the mean free path of atoms, meaning they can travel longer distances without colliding with other atoms. This is crucial in PVD processes, as it allows for more controlled and uniform deposition of materials onto the substrate.
-
High Thermal Evaporation Rates:
- A vacuum enables higher thermal evaporation rates by reducing the pressure within the chamber. This is essential for processes like PVD, where materials need to be vaporized and then deposited onto a substrate. The absence of atmospheric gases ensures that the vaporized material can travel unimpeded to the substrate, resulting in a more efficient and effective deposition process.
-
Minimization of Gaseous Contamination:
- One of the primary roles of a vacuum in deposition is to minimize contamination from atmospheric gases. In a vacuum, the density of undesirable atoms (such as oxygen or nitrogen) is significantly reduced, preventing unwanted chemical reactions that could degrade the quality of the deposited material. This is particularly important in processes like sintering, where oxidation can negatively impact the final product's properties.
-
Environmental Benefits of Vacuum Systems:
- Vacuum systems, such as those used in vacuum cleaning furnaces, are environmentally friendly. They operate without emitting waste gases or water, reducing the need for waste treatment and lowering air pollution. This aligns with modern environmental standards and supports sustainable industrial practices.
-
Prevention of Oxidation and Contamination:
- In processes like sintering, a vacuum environment prevents oxidation and contamination by atmospheric gases. This ensures better control over the sintering process, leading to improved physical and mechanical properties of the final product. The absence of atmospheric gases facilitates atomic diffusion, which is essential for forming high-density solid products.
-
Automated Control in Vacuum Brazing:
- In vacuum brazing furnaces, the vacuum system ensures the required vacuum level for the brazing process, while the heating system melts the brazing material. The process is controlled automatically by temperature control instruments, ensuring precision and consistency. This automated control is critical for achieving high-quality brazed joints without oxidation or contamination.
-
Long-Term Operational Reliability:
- The use of vacuum systems in industrial processes, such as deposition and sintering, helps ensure long-term operational reliability. By protecting against wear and contamination, vacuum environments extend the lifespan of equipment and maintain consistent performance over time.
In summary, the role of vacuum in deposition processes is multifaceted, encompassing improved material quality, environmental sustainability, and enhanced process control. By creating a controlled environment free from contamination, vacuum systems enable precise and efficient deposition, sintering, and brazing processes, ultimately leading to superior final products and reduced environmental impact.
Summary Table:
Key Role of Vacuum in Deposition | Benefits |
---|---|
Reduction of Atomic Density | Increases mean free path for controlled deposition |
High Thermal Evaporation Rates | Enables efficient material vaporization |
Minimization of Gaseous Contamination | Prevents unwanted reactions for cleaner results |
Environmental Benefits | Reduces waste emissions and pollution |
Prevention of Oxidation | Ensures high-quality final products |
Automated Control | Guarantees precision and consistency |
Long-Term Reliability | Extends equipment lifespan and performance |
Learn how vacuum systems can optimize your deposition processes—contact our experts today!