The role of vacuum in deposition methods is multifaceted and critical to the success of thin film deposition processes. A vacuum environment ensures a high mean free path for evaporated or sputtered materials, minimizing collisions and contamination. It reduces the presence of undesirable gases and impurities, allowing for the deposition of high-quality, defect-free films. Additionally, vacuum conditions enable precise control over gas and vapor composition, facilitate mass flow control, and create a low-pressure plasma environment essential for processes like Physical Vapor Deposition (PVD) and Electron Beam (E-beam) deposition. Overall, vacuum conditions are indispensable for achieving the desired film properties, purity, and uniformity in deposition methods.
Key Points Explained:
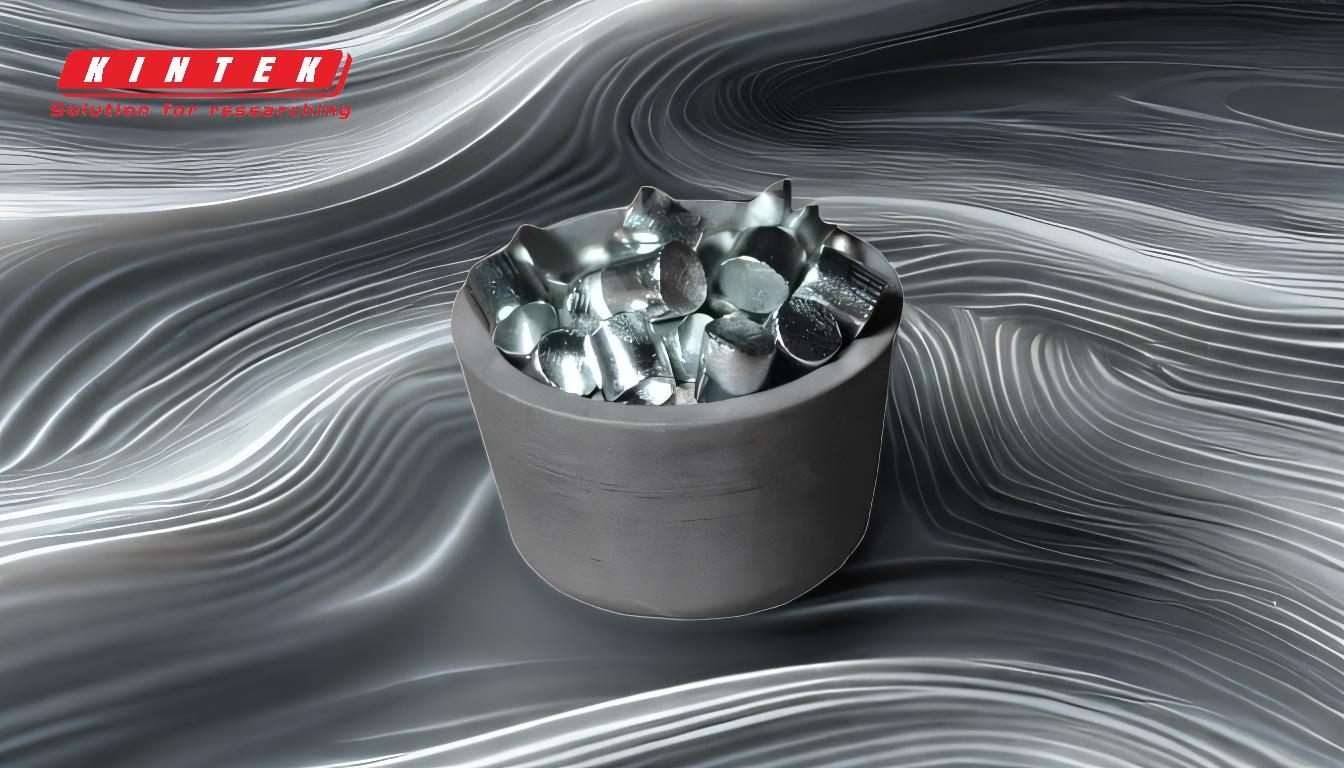
-
High Mean Free Path for Evaporated Material:
- In vacuum deposition, the reduced gas pressure significantly increases the mean free path of atoms and molecules. This means that the evaporated or sputtered material can travel longer distances without colliding with other particles, ensuring that most of the material reaches the substrate. This minimizes losses and contamination, leading to higher deposition efficiency and better film quality.
-
Reduction of Contaminants:
- A vacuum environment drastically reduces the presence of undesirable gases and impurities that can cause defects in thin films. By eliminating or minimizing these contaminants, the deposited films achieve higher purity and better performance characteristics. This is particularly important in applications requiring high precision, such as semiconductor manufacturing or optical coatings.
-
Control Over Gas and Vapor Composition:
- Vacuum conditions allow for precise control over the composition of gases and vapors within the deposition chamber. This control is essential for processes like Chemical Vapor Deposition (CVD) and Plasma-Enhanced Chemical Vapor Deposition (PECVD), where specific gas mixtures are required to achieve the desired film properties. It also enables the introduction of reactive gases in controlled amounts to modify film characteristics.
-
Low-Pressure Plasma Environment:
- Many deposition methods, such as PVD and E-beam deposition, rely on a low-pressure plasma environment. The vacuum facilitates the generation and maintenance of this plasma, which is crucial for processes like sputtering and ion-assisted deposition. The plasma environment enhances the energy of the deposited particles, improving film adhesion and density.
-
Mass Flow Control:
- Vacuum systems enable precise mass flow control of gases and vapors into the deposition chamber. This is critical for maintaining consistent deposition rates and ensuring uniform film thickness. Mass flow controllers (MFCs) are often used in conjunction with vacuum systems to achieve this level of control.
-
Thermal Evaporation Rate:
- In thermal evaporation processes, a vacuum environment allows for higher evaporation rates by reducing the pressure and minimizing the presence of residual gases. This is particularly important in E-beam deposition, where high evaporation rates are necessary to achieve efficient material transfer to the substrate.
-
Reduction of Gaseous Contamination:
- By maintaining a vacuum, the density of undesirable atoms and molecules is minimized. This reduction in gaseous contamination is crucial for achieving high-quality films with minimal defects. It also prevents the formation of soot or other unwanted by-products that can occur at higher pressures.
-
Influence on Plasma Properties:
- The vacuum environment influences the enthalpy, density of charged and uncharged particles, and energy distribution within the plasma. These factors are critical for controlling the deposition process and achieving the desired film properties, such as adhesion, density, and uniformity.
-
Elimination of Residual Gases:
- Achieving ultra-high vacuum (UHV) conditions prior to deposition eliminates residual gases that can cause defects in thin films. This is especially important in high-precision applications where even trace amounts of contaminants can significantly impact film performance.
-
Enhanced Film Properties:
- Overall, the vacuum environment enhances the properties of the deposited films, including their purity, uniformity, adhesion, and density. These improvements are essential for meeting the stringent requirements of advanced technological applications, such as microelectronics, optics, and nanotechnology.
In summary, the vacuum environment is indispensable in deposition methods, providing the necessary conditions for high-quality, defect-free film deposition. It ensures a controlled, contamination-free environment, facilitates precise process control, and enhances the properties of the deposited films.
Summary Table:
Key Role of Vacuum in Deposition | Benefits |
---|---|
High Mean Free Path | Minimizes collisions, reduces contamination, and improves deposition efficiency. |
Reduction of Contaminants | Ensures high-purity films, critical for precision applications. |
Control Over Gas Composition | Enables precise gas and vapor control for tailored film properties. |
Low-Pressure Plasma Environment | Facilitates processes like PVD and E-beam deposition for better film adhesion. |
Mass Flow Control | Maintains consistent deposition rates and uniform film thickness. |
Thermal Evaporation Rate | Increases evaporation rates, enhancing material transfer efficiency. |
Reduction of Gaseous Contamination | Minimizes defects and unwanted by-products. |
Influence on Plasma Properties | Controls particle energy and distribution for optimal film characteristics. |
Elimination of Residual Gases | Removes trace contaminants, ensuring defect-free films. |
Enhanced Film Properties | Improves purity, uniformity, adhesion, and density of deposited films. |
Ready to optimize your thin film deposition process? Contact us today to learn more about vacuum solutions!