The rotary kiln process is a high-temperature thermal treatment method used for processing granular or powdered materials. It involves heating materials in a rotating drum to facilitate chemical reactions such as calcination, oxidation, reduction, or sintering. Electric rotary kilns are a specific type of rotary kiln that use electric heating elements to achieve the required temperatures. These kilns are designed with multiple heating zones, each independently controlled, and are equipped with cooling systems to manage the material's discharge temperature. The process is highly customizable, with the kiln's size, heating elements, and rotation speed tailored to the specific material and production requirements. Electric rotary kilns are particularly effective for applications requiring precise temperature control and uniformity.
Key Points Explained:
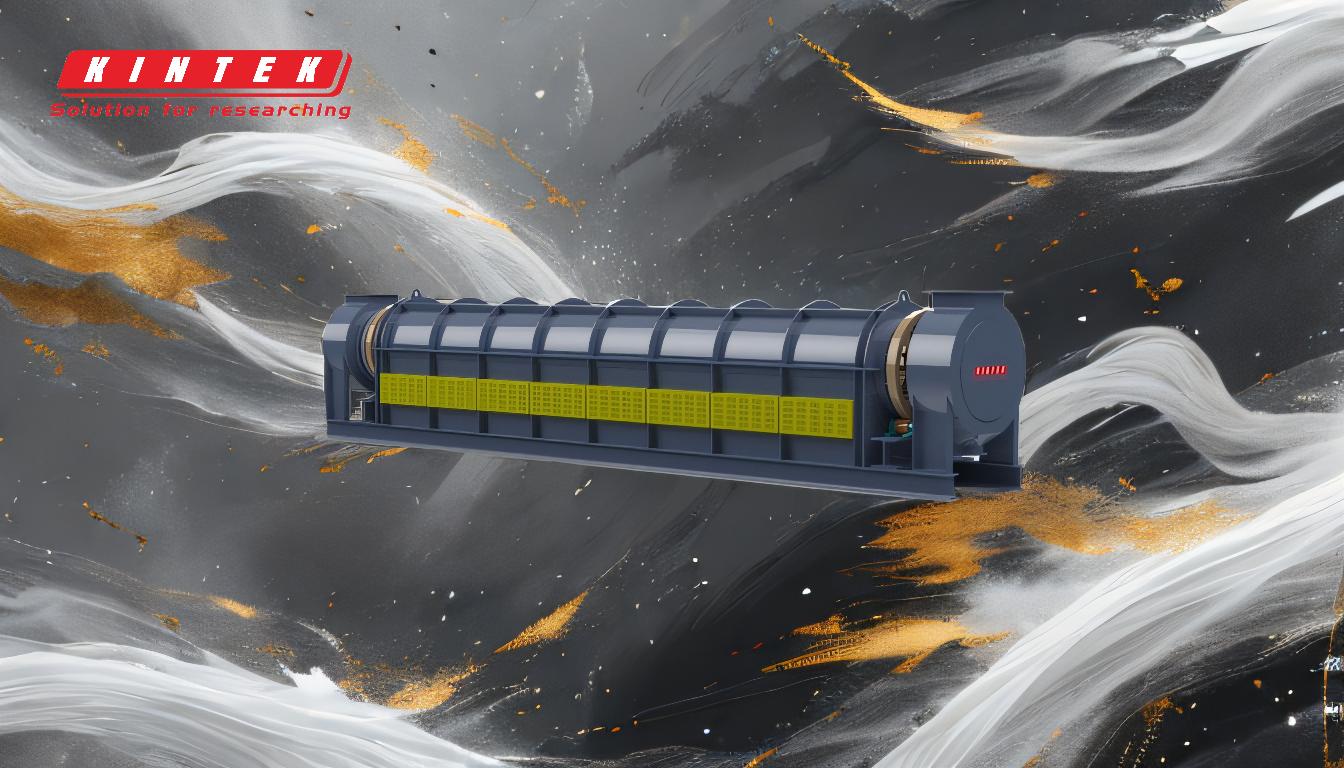
-
Types of Rotary Kilns:
- Rotary kilns can be direct-fired or indirect-fired (calciners). Direct-fired kilns use direct contact between the material and process gas to induce reactions, while indirect-fired kilns rely on heat from the externally heated drum shell.
- Electric rotary kilns are a specialized type that uses electric heating elements to achieve high temperatures, making them ideal for precise thermal processing.
-
Applications of Electric Rotary Kilns:
- Electric rotary kilns are used for calcining granular or powdered materials and facilitating high-temperature reactions such as oxidation and reduction.
- They are also employed in sintering, a process where materials are heated just below their melting point to increase strength, commonly used in iron ore pelletizing and proppant production.
-
Heating System:
- The heating elements in an electric rotary kiln are typically made from nickel-chromium alloys (e.g., 1Cr18Ni9Ti, Cr25Ni20Si2) or iron-chromium aluminum alloys (e.g., 0Cr13A14, 0Cr25A15).
- These spiral-shaped elements are installed on the sides and bottom of the kiln, divided into four heating zones, each with independent temperature control.
-
Cooling Process:
- Cooling is achieved using a drum cooler, where water is sprayed on the outside of the cylinder to indirectly cool the material as it passes through the drum.
- This ensures the material meets the required discharge temperature.
-
Rotation Mechanism:
- The kiln is rotated by a Girth Gear connected to a variable-speed electric motor. For example, a 6 x 60 m kiln requires around 800 kW to rotate at 3 rpm.
- A variable-speed drive controls the material flow rate, and an auxiliary drive (e.g., small electric motor or diesel engine) is used during power failures to prevent damage.
-
Kiln Construction:
- The rotary tube is made from nickel-based alloys, capable of withstanding temperatures up to 1100℃.
- The drum diameter and length can be customized based on material handling capacity, and multiple independent heating zones can be designed to meet production needs.
-
Sizing and Design:
- Sizing a rotary kiln involves engineering principles, thermal and chemical analyses, and experience to meet processing objectives.
- Key factors include capacity, heat generation, maximum feed rate, retention time, and bed profile, which determine the kiln's diameter and length.
-
Customization and Flexibility:
- Electric rotary kilns offer high flexibility, with customizable heating zones, rotation speeds, and cooling systems tailored to specific materials and production requirements.
- This makes them suitable for a wide range of industrial applications, from calcination to sintering.
By combining precise temperature control, efficient cooling, and customizable design, electric rotary kilns provide a reliable and versatile solution for high-temperature material processing.
Summary Table:
Aspect | Details |
---|---|
Types of Rotary Kilns | Direct-fired, indirect-fired (calciners), and electric rotary kilns. |
Applications | Calcination, oxidation, reduction, and sintering. |
Heating System | Nickel-chromium or iron-chromium aluminum alloy heating elements. |
Cooling Process | Drum cooler with water spray for indirect cooling. |
Rotation Mechanism | Girth gear and variable-speed electric motor for precise control. |
Kiln Construction | Nickel-based alloy tubes, customizable diameter and length. |
Customization | Adjustable heating zones, rotation speeds, and cooling systems. |
Discover how electric rotary kilns can optimize your material processing—contact us today for expert advice!