Brazing is a versatile joining process that uses filler metals to bond two dissimilar materials without melting the base materials. The process involves heating the filler metal to its melting point, allowing it to flow into the joint by capillary action, and then cooling to form a strong, durable bond. Key factors in brazing include the selection of appropriate filler materials, maintaining a controlled atmosphere to prevent oxidation, and ensuring proper joint design. Furnace brazing is a common method that allows for the simultaneous creation of multiple joints under controlled conditions. Understanding the rules and principles of brazing ensures high-quality, reliable joints in various industrial applications.
Key Points Explained:
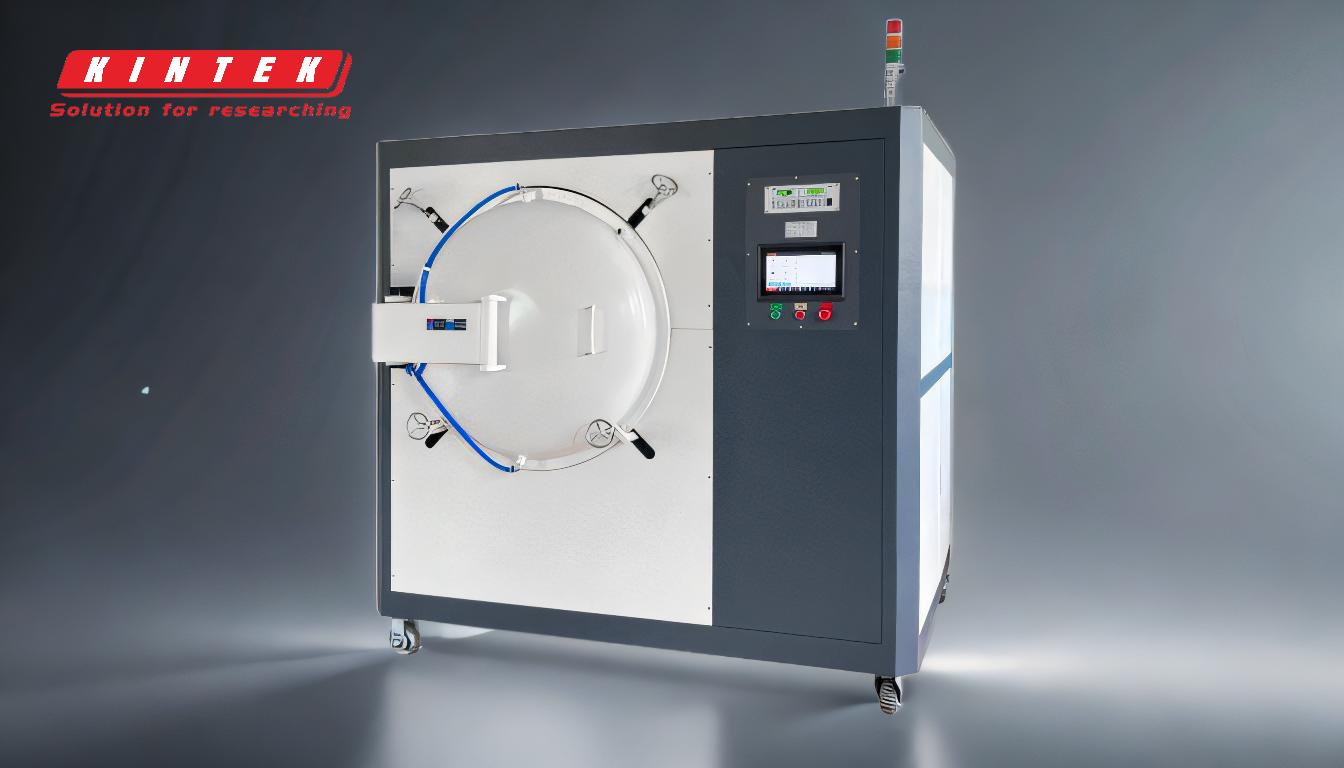
-
Definition and Process of Brazing:
- Brazing is a metal-joining process that uses a filler metal with a melting point above 450°C but below the melting point of the base materials being joined.
- The filler metal is heated until it melts and flows into the joint by capillary action, creating a strong bond upon cooling.
- Unlike welding, brazing does not melt the base materials, making it suitable for joining dissimilar metals or materials with different thermal properties.
-
Types of Brazing:
- Furnace Brazing: The entire assembly is heated in a furnace to a temperature where the filler metal melts and flows into the joint. This method is ideal for mass production and ensures uniform heating.
- Torch Brazing: A handheld torch is used to heat the joint and filler metal. This method is more flexible and suitable for small-scale or repair work.
- Induction Brazing: Uses electromagnetic induction to heat the joint and filler metal. It is fast and precise, often used for high-volume production.
- Dip Brazing: The assembly is immersed in a molten salt or metal bath to achieve the required temperature for brazing.
-
Importance of Atmosphere Control:
- Brazing requires a controlled atmosphere to prevent oxidation and ensure a clean, strong joint.
- The atmosphere must be free of oxidants, oxygen, and moisture. Typical conditions include:
- Neutral gas (e.g., pure nitrogen).
- Oxygen content < 100 ppm.
- Humidity < -40°C dew point.
- Proper atmosphere control prevents contamination and ensures the filler metal flows smoothly into the joint.
-
Selection of Filler Materials:
- Filler metals used in brazing include alloys of nickel, silver, copper, and other metals.
- The choice of filler material depends on the base materials being joined, the required joint strength, and the operating environment.
- Common filler metals include:
- Silver-based alloys for high-strength joints.
- Copper-based alloys for high-temperature applications.
- Nickel-based alloys for corrosion resistance.
-
Joint Design and Preparation:
- Proper joint design is critical for successful brazing. Joints should be designed to allow capillary action to draw the filler metal into the gap.
- Common joint types include lap joints, butt joints, and T-joints.
- Surfaces must be clean and free of contaminants such as oil, grease, and oxides to ensure proper bonding.
-
Advantages of Brazing:
- Brazing can join dissimilar materials, including metals and ceramics.
- It produces strong, leak-tight joints with minimal distortion.
- The process is suitable for complex assemblies and high-volume production.
- Brazed joints often have excellent corrosion resistance and thermal conductivity.
-
Applications of Brazing:
- Brazing is widely used in industries such as aerospace, automotive, HVAC, and electronics.
- Common applications include joining heat exchangers, electrical components, and structural assemblies.
By adhering to these rules and principles, brazing can produce high-quality, reliable joints that meet the demands of various industrial applications. Proper material selection, atmosphere control, and joint design are essential for achieving optimal results.
Summary Table:
Key Aspect | Details |
---|---|
Filler Metal | Melting point >450°C, below base materials; alloys of nickel, silver, copper. |
Atmosphere Control | Neutral gas (e.g., nitrogen), O₂ <100 ppm, humidity < -40°C dew point. |
Joint Design | Lap, butt, or T-joints; clean, contaminant-free surfaces for capillary flow. |
Types of Brazing | Furnace, torch, induction, dip brazing for varied applications. |
Advantages | Joins dissimilar materials, leak-tight, minimal distortion, corrosion-resistant. |
Applications | Aerospace, automotive, HVAC, electronics, heat exchangers, and more. |
Need expert guidance for your brazing projects? Contact us today for tailored solutions!