Hot isostatic pressing (HIP) is a manufacturing process used to densify materials, eliminate porosity, and improve mechanical properties. It involves applying high temperature and uniform pressure using inert gases like argon. The scale of hot isostatic pressing depends on the size of the equipment, the materials being processed, and the desired outcomes. While HIP operates at higher temperatures and pressures, warm isostatic pressing (WIP) operates at lower temperatures (typically below 500°C) but still applies uniform pressure, making it suitable for specific applications like material densification and diffusion. The scale of HIP can range from small laboratory setups to large industrial systems, depending on the requirements of the process.
Key Points Explained:
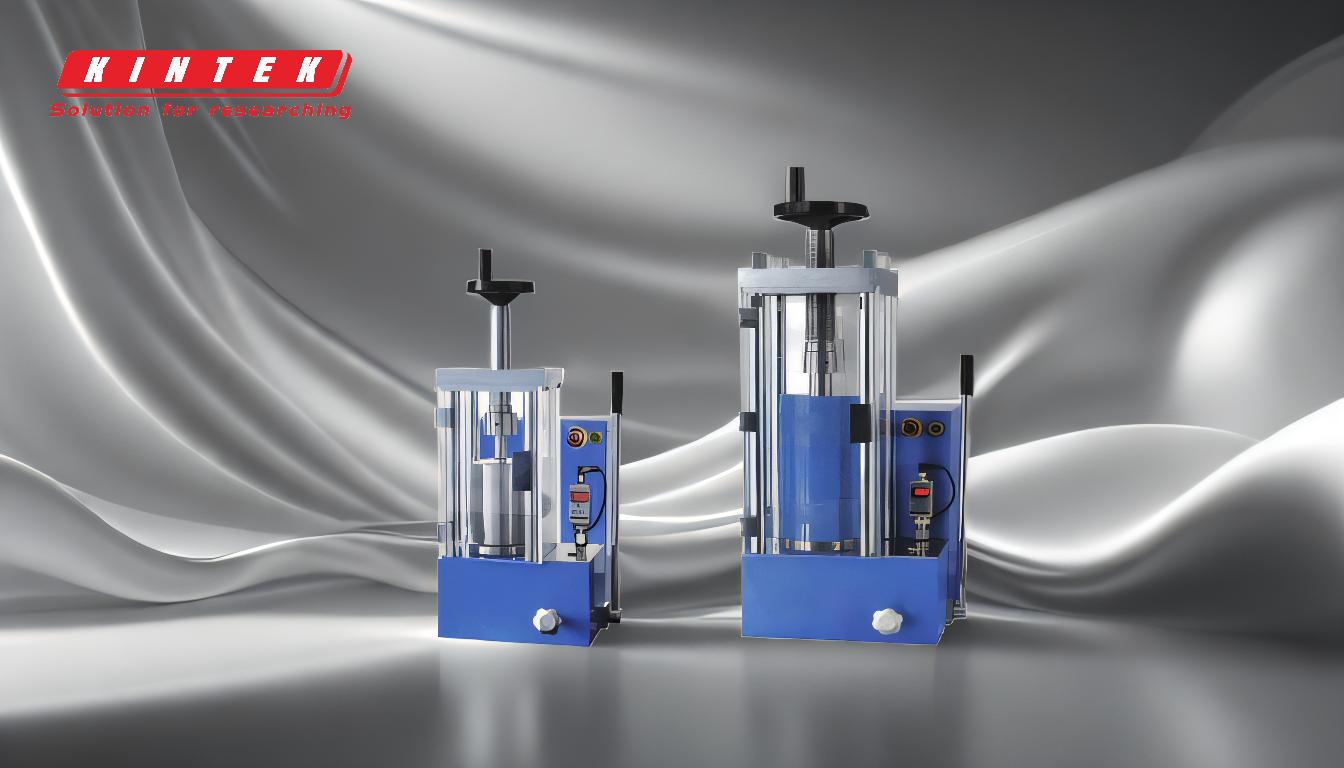
-
Process Overview of Hot Isostatic Pressing (HIP):
- HIP involves loading parts into a heating chamber where inert argon gas is applied under high pressure and temperature.
- The temperature, pressure, and process time are closely monitored to ensure optimal results.
- The process concludes with a depressurization and cool-down phase to safely remove the parts.
-
Scale of HIP Equipment:
- The scale of HIP systems varies widely, from small laboratory units for research and development to large industrial systems for mass production.
- Industrial-scale HIP systems can handle large components, such as aerospace parts or turbine blades, with chamber sizes exceeding several meters in diameter.
- Laboratory-scale HIP units are more compact, designed for smaller samples and experimental purposes.
-
Comparison with Warm Isostatic Pressing (WIP):
- While HIP operates at high temperatures (often above 1000°C), warm isostatic press systems operate at lower temperatures, typically below 500°C.
- WIP is used for processes like material densification, diffusion, and phase changes, where high temperatures are not required.
- WIP systems are generally smaller in scale compared to HIP systems, as they are designed for specific applications that do not require extreme temperatures.
-
Applications and Industrial Scale:
- HIP is widely used in industries like aerospace, automotive, and medical devices for producing high-strength, defect-free components.
- The scale of HIP systems is tailored to the size and complexity of the components being processed. For example, aerospace applications may require large-scale HIP systems to handle turbine disks or engine components.
- WIP, on the other hand, is often used for smaller-scale applications, such as producing high-quality ceramic or composite materials.
-
Techniques and Flexibility:
- Both HIP and WIP use isostatic pressing techniques, such as the wet-bag or dry-bag method, to apply uniform pressure.
- The wet-bag technique involves submerging a flexible mold in a pressure vessel, while the dry-bag technique uses a fixed mold within the vessel.
- These techniques allow for scalability, as the size of the pressure vessel and molds can be adjusted based on the application.
-
Advantages of Isostatic Pressing:
- Both HIP and WIP produce components with superior mechanical properties compared to conventional pressing methods.
- The uniform pressure application ensures consistent density and eliminates defects like porosity.
- The scale of the process can be adapted to meet specific production needs, from small batches to large-scale manufacturing.
In summary, the scale of hot isostatic pressing depends on the application, with systems ranging from small laboratory units to large industrial setups. Warm isostatic pressing, while operating at lower temperatures, shares similarities in terms of uniform pressure application but is generally used for smaller-scale, specialized applications. Both processes offer significant advantages in terms of material quality and versatility.
Summary Table:
Aspect | Details |
---|---|
Process Overview | High temperature and uniform pressure using inert gases like argon. |
Scale of HIP Equipment | Ranges from small lab units to large industrial systems. |
Applications | Aerospace, automotive, medical devices, and more. |
Comparison with WIP | WIP operates at lower temperatures (<500°C) and is used for smaller-scale applications. |
Advantages | Eliminates porosity, improves mechanical properties, and ensures uniform density. |
Discover how hot isostatic pressing can transform your manufacturing process—contact our experts today!