Calcination is a critical thermal process used in metallurgy and material science to purify ores and other solid materials by heating them below their melting point in a controlled environment, typically with limited air or oxygen. This process removes volatile impurities, induces thermal decomposition, or facilitates phase transitions, making it essential for extracting metals from ores and preparing materials for further processing. Its significance lies in its ability to enhance the purity and usability of materials, making it indispensable in industries like mining, ceramics, and chemical manufacturing.
Key Points Explained:
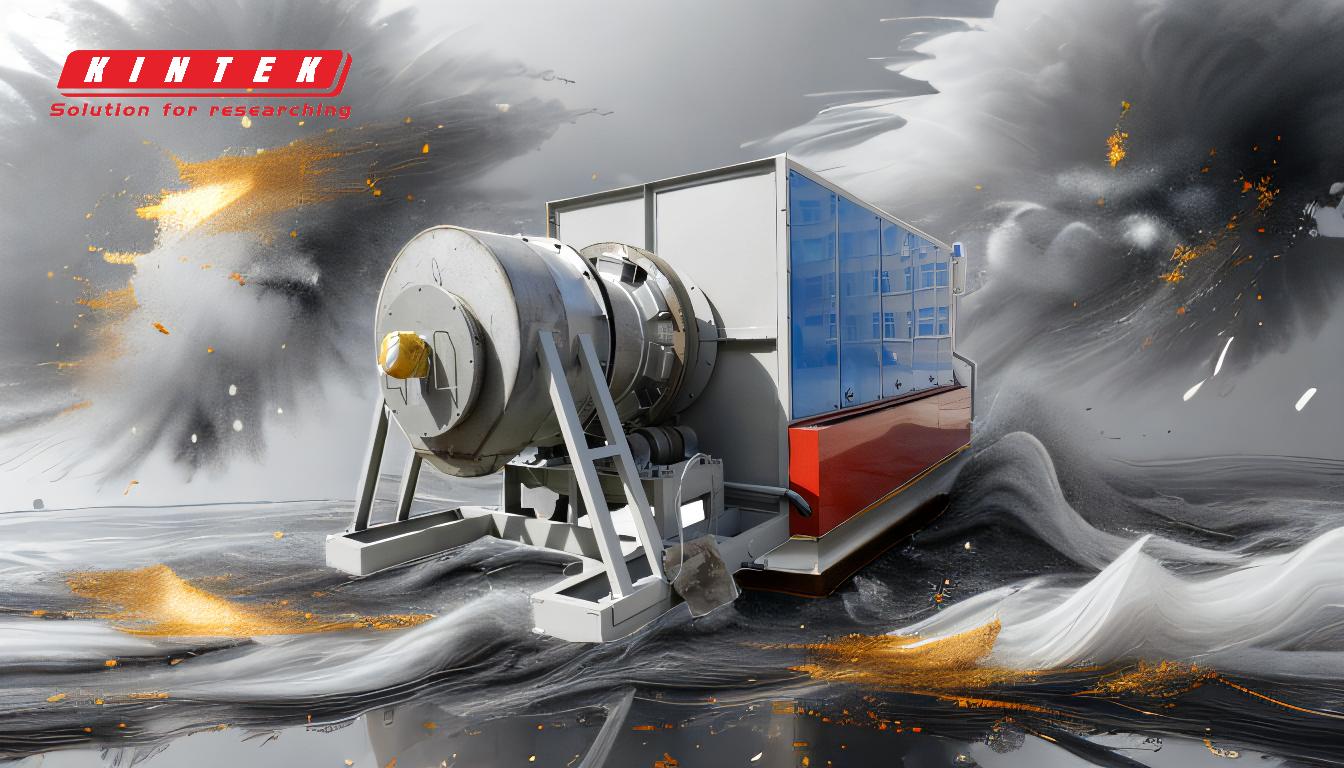
-
Definition and Purpose of Calcination:
- Calcination involves heating metal ores or solid materials below their melting point, often in the absence or limited supply of air or oxygen.
- The primary purpose is to remove volatile impurities, such as water, carbon dioxide, or organic compounds, from the material.
- This process is crucial for purifying ores and preparing them for subsequent metallurgical processes.
-
Thermal Decomposition and Phase Transitions:
- Calcination induces thermal decomposition, breaking down complex compounds into simpler forms.
- For example, carbonate ores decompose into oxides and release carbon dioxide gas.
- It can also cause phase transitions, altering the physical or chemical structure of the material to make it more suitable for further processing.
-
Applications in Metal Extraction:
- Calcination is widely used in pyrometallurgy to extract metals from their ores.
- For instance, heating limestone (calcium carbonate) produces lime (calcium oxide), a key material in cement production and steelmaking.
- It is also used to remove sulfur and other impurities from sulfide ores.
-
Role in Material Purification:
- By eliminating volatile substances, calcination enhances the purity of materials, making them more suitable for industrial applications.
- This is particularly important in industries like ceramics, where impurities can compromise the quality of the final product.
-
Environmental and Economic Benefits:
- Calcination reduces the need for chemical reagents in downstream processes, making it more environmentally friendly.
- It also improves the efficiency of metal extraction, reducing costs and energy consumption in industrial operations.
-
Examples of Calcination in Industry:
- In cement production, calcination of limestone is a key step in producing clinker, the intermediate product used to make cement.
- In the production of alumina from bauxite, calcination removes water and other impurities, yielding a high-purity aluminum oxide.
-
Comparison with Other Thermal Processes:
- Unlike roasting, which involves heating in the presence of excess air or oxygen, calcination typically occurs in a controlled or limited oxygen environment.
- Calcination is distinct from sintering, which involves heating materials to just below their melting point to bond particles without melting them.
-
Challenges and Considerations:
- The process requires precise temperature control to avoid melting the material or causing undesirable reactions.
- Energy consumption and emissions are key considerations, especially in large-scale industrial applications.
In summary, calcination is a vital process in metallurgy and material science, enabling the purification, decomposition, and transformation of ores and solid materials. Its applications span industries, from mining to ceramics, and its significance lies in its ability to enhance material purity and efficiency in industrial processes.
Summary Table:
Key Aspect | Description |
---|---|
Definition | Heating ores below melting point in limited air/oxygen to remove impurities. |
Purpose | Purifies ores, induces thermal decomposition, and facilitates phase transitions. |
Applications | Metal extraction, cement production, alumina refining, and ceramics. |
Benefits | Enhances material purity, reduces costs, and improves industrial efficiency. |
Challenges | Requires precise temperature control and energy management. |
Discover how calcination can optimize your industrial processes—contact our experts today!